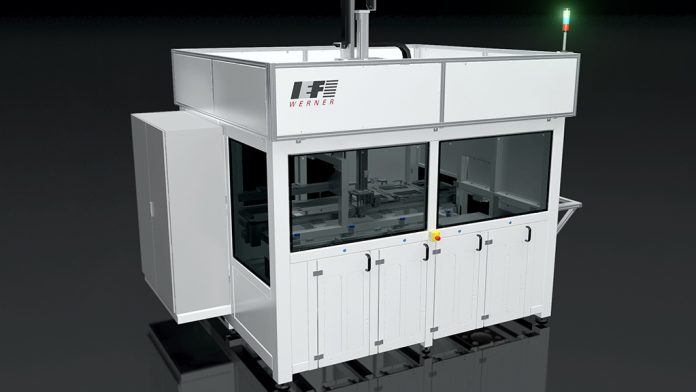
Rolf Kölle, Vertriebsmitarbeiter im Bereich Palettiersysteme bei IEF-Werner, kennt seine Kunden: „Betriebe setzen immer häufiger auf Bodenroller. Diese sind sehr günstig in der Anschaffung und haben sich dadurch in der Industrie durchgesetzt. Bodenroller gehören mittlerweile zum internen Logistikstandard.“ Die Kunden erhalten damit ein durchgehendes und effizientes Transportkonzept für alle Prozessschritte. Zudem lassen sich darauf verschiedene Bauteile in der Produktion lagern und schnell für den nächsten Bearbeitungsschritt bereitstellen.
Und das wird immer wichtiger. Denn um den steigenden Anforderungen der Produktion gerecht zu werden, sind die verschiedenen Komponenten pünktlich, in der erforderlichen Menge und in der geforderten Reihenfolge an die jeweilige Arbeitsstation zu liefern. Dafür würden sich die Bodenroller besonders gut eigenen, ist sich Kölle sicher. Darauf gestapelt werden zum Beispiel Kleinladungsträger (KLT), in denen sich die Roh- und Halbfabrikate sowie Fertigprodukte befinden.
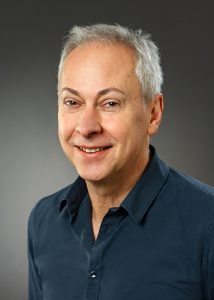
„An den Schnittstellen zur Montage- oder Prüflinie stehen dabei die Palettierer“, beschreibt Kölle. Der Automatisierungsspezialist aus Furtwangen im Schwarzwald entwickelt Palettierer in unterschiedlichen Variationen und sieht ein großes Potenzial in der Kombination aus Bodenrollern und Palettierern. Mit den Bodenrollern können Betreiber diese Maschinen auch ergonomisch beladen ohne schwere Lasten zu heben. Die Palettierer lassen sich zudem von Fahrerlosen Transportsystemen bedienen.
Dazu kommt: Niveauunterschiede durch Unebenheiten in Hallenböden spielen keine Rolle. Genau das sei ein häufiges Problem bei Kunden, weiß Kölle. Die Palettierer gleichen diese Unebenheiten aus – zum Beispiel mit nivellierbaren Bodenschienen. Auch lassen sich unterschiedliche Stapel- und Trayhöhen verarbeiten. „Die Palettierer können so auch angefangene Tray-Stapel verarbeiten“, erläutert Kölle. „Es muss nicht immer ein komplett voller Palettenstapel sein, der in die Schächte geschoben wird.“
Ohne die Produktion zu unterbrechen
„Wichtig bei der automatisierten Produktion ist ein schneller Wechsel, wenn ein Stapel abgearbeitet ist“, sagt Kölle. „Denn die Produktion soll nicht unterbrochen werden.“ Doch genau hier liegt die Herausforderung. Standardpalettierer haben in der Regel zwei Schächte. Einen für die Roh- und einen für die Fertigteile. Arbeitet die Anlage den letzten Tray mit Rohteilen ab, muss der Bediener den Stapel schnell wechseln können, um die Produktion nicht zu lange zu unterbrechen.
Eine Möglichkeit, dieses Problem zu umgehen, ist der Einsatz von zwei oder mehr Palettierern – doch das erfordert nicht nur höhere Investitionskosten, sondern auch Platz in der Halle. Wir bieten nun unsere Baureihe varioSTACK als Mehrschachtpalettierer an“, sagt Kölle. „Je nach Bedarf rüsten wir eine Anlage mit drei, vier, fünf oder sogar sechs Schächten aus.“
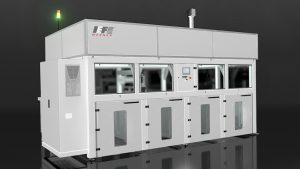
Ein varioSTACK mit drei oder vier Schächten ist breiter als ein Standardpalettierer, nimmt aber nicht so viel Platz in Anspruch wie zwei Standardanlagen dieser Baureihe. Er bietet jedoch die gleiche Autonomie. Mit Mehrschachtpalettierern lassen sich Trays wechseln, ohne den Automatikbetrieb zu unterbrechen. Die Produktion läuft einfach am nächsten freien Schacht weiter. Für den Wagenwechsel hat der Bediener so viel Zeit, bis der nächste Schacht auch voll ist.
Der Betreiber hat zudem die Möglichkeit zum Vorrüsten – er kann damit auf Produktwechsel ohne Zykluszeitverlust souverän reagieren. Rolf Kölle denkt an einen Kunden aus der Zulieferindustrie, der einen IEF-Mehrschachtpalettierer äußerst erfolgreich einsetzt. „Der Betreiber kann jederzeit während der Produktion einen Schacht auf eine neue Produktvariante vorrüsten, ohne die Produktion zu unterbrechen. Damit eignen sich Mehrschachtpalettierer besonders auch für Kunden mit einer hohen Produktvielfalt.“
Sicherer Wagenwechsel
Für den sicheren Wagenwechsel haben die IEF-Entwickler einen Leuchtdrucktaster über jedem Palettenschacht angebracht. Dieser leuchtet, sobald der Schacht für den Wagenwechsel bereit ist. Der Bediener drückt auf den Taster. Die Leuchte blinkt, das Entriegeln des Wagens ist angefordert. Eine Abdeckung fährt über den Schacht, danach erfolgt die Freigabe und die Tür wird entriegelt. Der Bediener kann den Schacht sicher öffnen und den Wagen wechseln.
„Wir haben mit den Mehrschachtpalettierern noch eine Reihe weiterer Vorteile“, beschreibt IEF-Experte Kölle. „Mit einem weiteren Schacht hat der Betreiber unter anderem die Möglichkeit, fehlerhafte Teile separat abzulegen. Dazu integrieren die IEF-Ingenieure einen zweiten Palettentisch. Somit ist eine Durchmischung von Gut- und Schlechtteilen ausgeschlossen.
Mit einem zweiten Palettentisch kann der Mehrschachtpalettierer aber auch Fertigteile in einen separaten Tray ablegen. Dazu werden Rohteile aus dem Behälter, der auf dem ersten Tisch liegt, entnommen und nach der Bearbeitung in einem separaten Tray auf dem zweiten Tisch abgelegt. „Für den Fall, dass aufgrund zu vieler Ausschussteile nicht genügend Trays mit Fertigteilen gefüllt sind, können die leeren Behälter im dritten Schacht gepuffert werden“, erklärt Kölle.
Der Betreiber kann mit einem zweiten Palettentisch aber auch eine zweite Produktvariante in einen separaten Tray vorhalten: Beide Varianten sind je nach Typ auf den jeweiligen Tischen abgelegt. Ohne Taktzeitverlust lässt sich so zwischen den zwei Varianten wechseln. „Wir können im laufenden Betrieb zudem ein zweites Produkt vorrüsten“, beschreibt Kölle. „Der Bediener schiebt einfach ein neues Produkt in einen leeren Schacht ein. In der Steuerung weist er dann dem Schacht das neue Programm zu.“
Auch Europaletten lassen sich handhaben
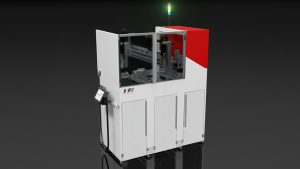
„Es lassen sich mit den genannten Vorteilen aber auch Europaletten sicher handhaben“ sagt Kölle. Dazu bietet IEF-Werner das Palettiersystem euroSTACK. Damit können Betreiber vor allem große Werkstückmengen palettieren. Die Anlage kann ohne Unterbrechung während des Betriebs kontinuierlich bestückt werden. „In der Standardausführung ist die Anlage für Trays im Halben-, Viertel- oder Achteleuromaß mit einem Maximalgewicht von 40 Kilogramm pro Tray ausgelegt. Diese werden der Anlage – auf Europaletten aufgestapelt – zugeführt“, erklärt Kölle.
Im Einsatz bewährt
Einige Anwender setzen bereits erfolgreich auf die Mehrschachtpalettierer von IEF-Werner. „Wir lieferten einen euroSTACK mit vier Schächten an einen Kunden, der für kurze Taktzeiten zwei Schächte für Roh- und zwei Schächte für die Fertigteile benötigte. Bei den Rohteilen handelt es sich um Stanzpakete, die von Paletten in Werkstückträger entladen werden sollen.
Auf den Paletten mit den Maßen 400 x 600 Millimeter liegen 36 Stanzpakete. Diese müssen von der liegenden in eine senkrechte Position gebracht und in Werkstückträger beladen werden. Die Fertigteile sind die Stanzpakete mit Wicklung. Diese kommen auf den Werkstückträgern stehend an und werden wieder liegend einpalettiert. Die Paletten für die Fertigteile können jeweils 24 Stück Aufnehmen.
Für das Teilehandling kommen zwei 4-Achs-Positioniersysteme, mit Linearantrieben aus dem bewährten IEF Portfolio zum Einsatz. Zwei unabhängige Palettentische erlauben einen Palettenwechsel ohne, dass dabei das Teilehandling beeinflusst wird. Der Palettenwechsel von und zur Europalette erledigt ein Portalsystem mit vier Achsen ebenfalls aus dem IEF-Portfolio. „Mit unserer Lösung konnten wir die vielfältige Aufgabe kompakt, sicher und ökonomisch umsetzen“., sagt Kölle.
Kontakt: