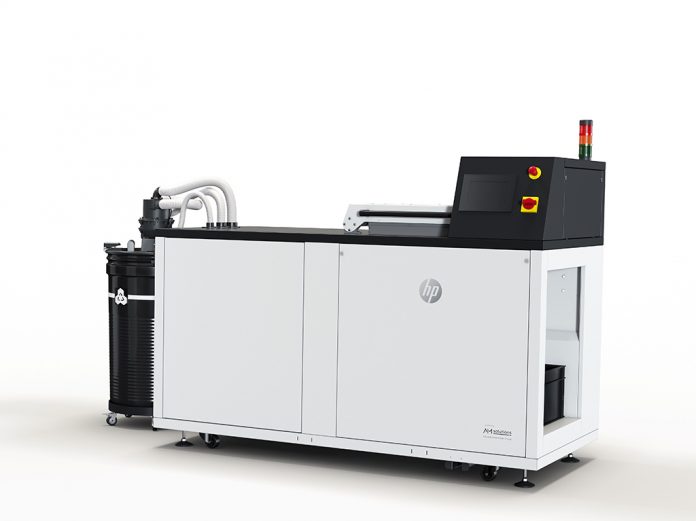
Als Anbieter von industrietauglichen Lösungen für den 3D-Druck und die digitale Fertigung hat HP frühzeitig erkannt, dass die Industrialisierung des 3D-Drucks nur gelingt, wenn Druck und Post Processing in einer automatisierten, skalierbaren Prozesskette abgebildet werden.
Durch die vor rund einem Jahr geschlossene Kooperation mit dem auf Lösungen für die Nachbearbeitung additiv hergestellter Teile spezialisierten Unternehmensbereich von Rösler, AM Solutions – 3D post processing technology, wurden die Voraussetzungen dafür geschaffen.
Denn während bei 3D-Druckern und insbesondere mit der HP Multi Jet Fusion-Technologie heute bereits Lösungen zur Verfügung stehen, die Industriestandards erfüllen, war das Post Processing bisher meist mit vielen manuellen Tätigkeiten verbunden. Dies ändert sich mit der 3D Automatic Unpacking Station für die HP Jet Fusion 5200 Serie.
Eingeflossen in die erste gemeinsame Maschinenentwicklung von HP und AM Solutions – 3D post processing technology sind Druck- und Softwaretechnik sowie Material-Know-how von HP und die über 80-jährige Erfahrung in den Bereichen Oberflächenbearbeitung und Maschinenbau für industrielle Anwendungen von Rösler.
Reproduzierbares, schnelles Entpacken und hohe Pulverrecyclingrate
Der automatische Entpackprozess startet direkt nach dem Abkühlen des Druckjobs in der HP Natural Cooling Unit. Die Cooling Unit wird mit einem Hebelift zur 3D Automatic Unpacking Station transportiert, darauf platziert, automatisch entriegelt und der komplette Druckjob in die Station geladen. Sämtliche Daten zum Druckjob werden per RFID-Tag an die Steuerung der Entpackstation übermittelt. Dadurch wird sichergestellt, dass die baujob- und prozessbezogenen Daten verfolgt und der Prozess mit Hilfe des HP Software 3D Centers fernüberwacht werden kann.
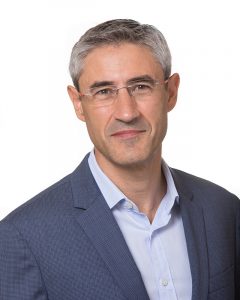
Darüber hinaus lässt sich durch den automatisierten, teilespezifischen Entpackvorgang, abhängig von der jeweiligen Geometrie, deutlich mehr Pulver zurückgewinnen. Das entfernte Pulver wird in der Station kontinuierlich abgesaugt und in einem externen Behälter gesammelt. Die Ausgabe der entpackten Teile erfolgt in eine Entladebox. Der volle Pulverbehälter wird durch einen leeren ersetzt, und das gesammelte Pulver kann mittels Behälter über die 3D Processing Station wieder der HP Build Unit zugeführt werden. Die neue 3D Automatic Unpacking Station minimiert nicht nur manuelle Eingriffe, sondern reduziert auch die Prozesszeit für bestimmte Applikationen, da der Auspackvorgang unmittelbar nach Ablauf der empfohlenen Mindestkühlzeit beginnen kann.
„Neue Lösungen für skalierbares, effizientes Post Processing und die Automatisierung des Workflows sind der Schlüssel, um das Potenzial der additiven Fertigung voll auszuschöpfen und in die industrielle Serienfertigung zu überführen“, erklärt Ramon Pastor, GM and Global Head of HP 3D Printing & Digital Manufacturing. „Mit Rösler/AM Solutions haben wir einen Partner, der mit den Industriestandards verschiedenster Branchen bestens vertraut ist und das notwendige Know-how sowohl im Bereich der Oberflächenbearbeitung als auch im Maschinenbau mitbringt.“
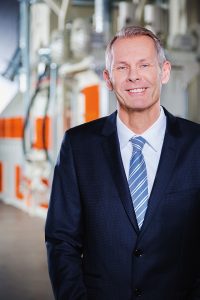
Stephan Rösler, CEO der Rösler Oberflächentechnik GmbH, merkt an: „Die extensive Expertise von HP in den Bereichen 3D-Druck, Software und digitale Fertigung ermöglicht uns, industrietaugliche Innovationen für das 3D Post Processing zu beschleunigen und Produktentwicklungen zielgerichtet an die Anforderungen industrieller Anwender anzupassen“.
Dass dies der Fall ist, bestätigt Matteo Rigamonti, Gründer von Weerg: „Die HP 3D Automatic Unpacking Station hat unsere Erwartungen an eine automatisierte Entpacklösung wirklich erfüllt. Unser Auspackprozess wurde nicht nur wesentlich schneller, sondern wir können jetzt auch mehr Pulver zurückgewinnen. Das Verfahren ist präzise und funktioniert auch bei kleinen und empfindlichen Teilen.“
Das im italienischen Scorzè ansässige Unternehmen fertigt täglich ca. 2.500 Teile im 3D-Druck und hat die neue Maschine bei sich vor Ort im Probebetrieb auf Herz und Nieren getestet. „Mit der Erweiterung unseres Geschäfts sollen diese verbesserten Möglichkeiten uns dabei helfen, die Kundennachfrage zu erfüllen und unsere Durchlaufzeiten für die Serienproduktion zu verbessern,“ ergänzt Matteo Rigamonti.
Kontakt: