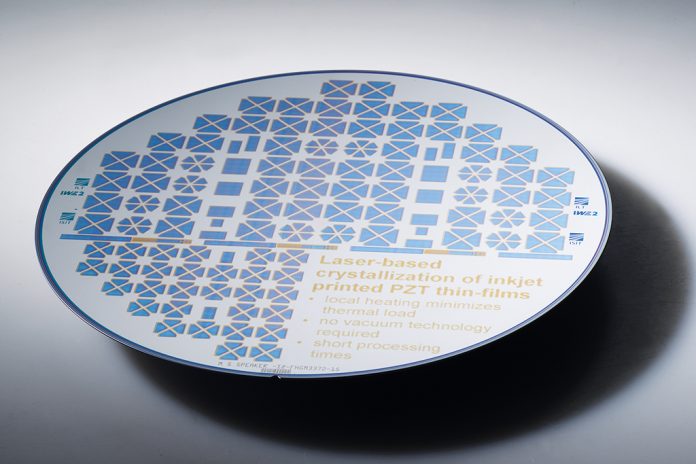
Piezoelektrische, mikroelektromechanische Systemen – sogenannten Piezo-MEMS – sind wahre technische Alleskönner, denn die hauchdünnen piezoelektrischen Schichten erfüllen wahlweise aktorische oder sensorische Funktionen: Entweder dehnen sie sich beim Anlegen eines elektrischen Feldes aus oder sie wandeln mechanische Bewegung in elektrische Spannung um.
Entsprechend gefragt sind sie u.a. in der Kommunikations- oder Medizintechnik zum Beispiel als Sensor oder Aktor in Pumpen, Ventilen oder Lautsprechern – jeweils im Miniaturformat. Die Dünnschichten bestehen in der Regel aus Blei-Zirkonat-Titanat (PZT), der derzeit leistungsfähigsten piezoelektrischen Funktionskeramik. Es kommen bevorzugt piezoelektrische, wenige μm dünne Schichten zum Einsatz, welche sich beispielsweise durch Ätzen oder direktes Drucken sehr genau strukturieren lassen.
Laserunterstützte Druckverfahren als Alternative zur konventionellen Hochvakuumbeschichtung
Bislang wurden in der Produktion von Piezo-MEMS konventionelle vakuum- und maskenbasierte Herstellungsmethoden eingesetzt, die allerdings insbesondere bei der Produktion von Kleinserien sehr zeit- und kostenintensiv sind. Im Rahmen des vom Bundesministerium für Bildung und Forschung (BMBF) geförderten Projekts GENERATOR entwickelte das Fraunhofer ILT gemeinsam mit dem Fraunhofer ISIT und dem IWE2 der RWTH Aachen daher als günstige Alternative eine Verfahrenskombination aus digitalem Tintenstrahldruck und Laserkristallisation: Nach dem Auftragen von PZT-Spezialtinte auf 8“-Silizium-Wafern folgt die Kristallisation mittels Laserstrahlung bei lokalen Temperaturen von über 700°C. Für Qualität sorgt ein temperaturgeregelter Prozess, der die Temperaturschwankungen auf ± 5°C begrenzt.
Trend zum Multi-Material-Stack
Aus mehreren 20 bis 30 nm dünnen PZT-Schichten wird ein mehrlagiger Aktuator mit einer Gesamtschichtdicke von 2 bis 3 µm aufgebaut. »Anfangs brachten wir nur eine einfache Schicht auf, mittlerweile entsteht Schicht um Schicht ein Multi-Material-Stack«, erklärt ILT-Wissenschaftler Samuel Fink. Abwechselnd bauen sich übereinander insgesamt bis zu 30 Schichten aus Funktionskeramik- und Elektroden zu einem Mikrolautsprecher auf. Dank dieser Konstruktion soll der Aktuator eine bessere Performance und höhere Wiedergabequalität als übliche Aktuatoren aufweisen.
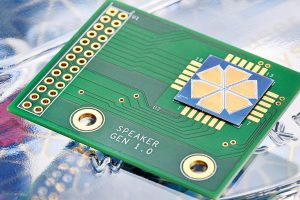
Dabei greifen PZT-Schichten und Elektroden-Schichten wie zwei sehr feine Kämme ineinander. Durch die schnelle Laserbearbeitung der Schichten sinkt die sonst minutenlange Bearbeitungszeit je Schicht auf wenige Sekunden. Als Elektrodenmaterial verwenden die Wissenschaftler statt des gängigen und sehr teuren Platins die elektrisch leitende Keramik Lanthan-Nickel-Oxid (LNO). Durch den Verzicht auf metallische Komponenten kann die Haltbarkeit dieser rein keramischen Multi-Material-Stacks deutlich gesteigert und die Materialkosten gleichzeitig gesenkt werden.
Legt man nun eine Wechselspannung an diesen Multi-Material-Stack an, verformen sich die PZT-Schichten in Bruchteilen von Sekunden und regen dadurch den ganzen Stack zur Schwingung an. Da das ganze System nur wenige µm dick ist und dadurch eine sehr geringe Masse hat, lassen sich so akustische Signale vor allem im Hochton-Bereich ausgezeichnet übertragen.
»Das Schöne an dieser Fertigungsmethode sind die digital steuerbaren Druck- und Laserverfahren, die eine instantane Designänderung der hergestellten Schichten ohne Mehrkosten für Masken oder Werkzeuge und somit auch die Produktion kleinerer Losgrößen ermöglichen«, so Dr. Christian Vedder, Leiter der Gruppe Thin Film Processing am Fraunhofer ILT.
Chance für kleine und mittlere Unternehmen
Konventionelle Anlagen zum Herstellen von Dünnschicht-Elektronik kosten mehrere Millionen Euro und lohnen sich daher nur für die Großserienproduktion. Bei kleineren Losgrößen wird das additive Hybridverfahren interessant, vor allem wenn das Bauteil wie der Mikrolautsprecher aus mehreren Schichten besteht.
Das Verfahren eignet sich daher besonders für kleine und mittlere Unternehmen (KMU), denn die Investition in die Anlagentechnik fällt im Vergleich zu konventioneller Technik deutlich günstiger aus. Fink: »Der Anwender benötigt dazu entsprechende Druck- und Lasersystemtechnik sowie speziell angepasste PZT- und LNO-Tinten. Sogar sehr kleine Job-Shops könnten sich daher in Zukunft eine Kleinserienproduktion für Mikroaktorik aufbauen.«
Es geht einfacher: Glas statt Silizium
Bisher wurde das Verfahren für die Beschichtung von Siliziumsubstraten verwendet. Diese müssen nach dem Aufbau des Multi-Stack-Systems bisher noch relativ aufwändig nachbearbeitet werden, um einsatzfähige Bauteile zu erzeugen. Durch die Eigenschaften des laserbasierten Herstellungsverfahrens sind aber auch andere Substrate wie z.B. Dünnstglas denkbar, welche die Fertigung noch erheblich vereinfachen und vielfältige Anwendungsmöglichkeiten erschließen würden.
»Im Laufe des Projekts konnten wir neben der Verfahrensentwicklung sehr spannende Ergebnisse zu den grundlegenden Mechanismen der Laserkristallisation von Keramiken erarbeiten, die im Millisekundenbereich ablaufen. Hier bahnen sich neue Möglichkeiten an, die mich persönlich sehr interessieren und sich bald hoffentlich auch auf andere Materialien und damit Einsatzgebiete übertragen lassen«, blickt Fink in die Zukunft.
Das diesem Bericht zugrundeliegende Vorhaben wurde mit Mitteln des Bundesministeriums für Bildung und Forschung unter dem Förderkennzeichen 03VP02223 gefördert.
Kontakt: