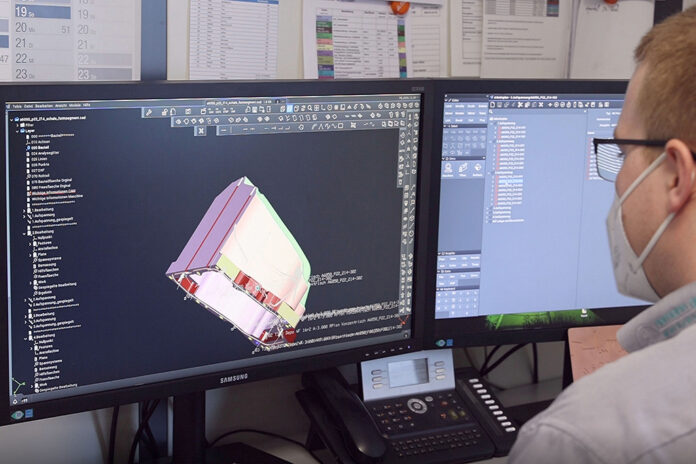
Bei Umformwerkzeugen für die Automotive-Industrie, aber auch bei Teilen für den Maschinenbau geht der Trend zu immer komplexeren Geometrien. Beim Riemann Werkzeugbau in Georgsmarienhütte sieht man das am Maschinenpark: Im Unternehmen besteht er nahezu ausschließlich aus fünfachsigen DMG-Maschinen.
Die jüngste ist erst Ende vergangenen Jahres in die Werkshallen des Unternehmens im Osnabrücker Land eingezogen. In diesem Jahr kommt eine MTE-Fahrständerfräsmaschine dazu, denn die wachsenden Dimensionen der Werkstücke sind ebenfalls ein Trend, den die Werkzeugbauer seit einigen Jahren beobachten.
„Der Trend geht ganz klar zur 5-Achs-Bearbeitung“, erklärt Michael Riemann, der das Unternehmen zusammen mit seinem Bruder Peter und seinem Vater Klaus Riemann leitet. „Noch vor einigen Jahren fertigten wir zu 80 Prozent auf 3-Achs-Maschinen. Heute kommt man aufgrund der immer anspruchsvolleren Geometrien an 5-Achs-Maschinen nicht mehr vorbei.“
Als in den vergangenen Jahren die zu bearbeitenden Werkstücke immer komplexer wurden und zudem auch ein immer größeres Volumen an Fräsbearbeitung erforderten, machten sich die Grenzen des bislang eingesetzten weit verbreiteten CAD/CAM-Systems schmerzhaft bemerkbar.
„Wo wir früher Aufträge mit 200 bis 300 h Fräsbearbeitung hatten, sind es heute Aufträge mit 5000, 6000, ja sogar bis zu 10 000 h Fräsbearbeitung“, erinnert sich Michael Riemann. „Abgesehen davon, dass das System Defizite in einigen Bereichen aufwies, wurden zusätzlich zum größeren Fräsvolumen auch die Rechenzeiten aufgrund hochkomplexer Geometrien immer länger. Das wurde bereits dann spürbar, wenn wir ein Werkstück auf dem Bildschirm um 180° drehen wollten. Da konnte der Konstrukteur gleich Kaffeepause machen.“
Das Verhältnis von Programmierzeit zu Spindellaufzeit stand nicht mehr in einem wirtschaftlichen Verhältnis zueinander. Komplexere Berechnungen liefen oft die ganze Nacht. Hinzu kam, dass das bislang eingesetzte System keine Schablonen etwa für wiederkehrende Programmieraufgaben unterstützte. „Wir mussten handeln“, schildert Michael Riemann die damalige Lage. „Für uns wäre eine Aktualisierung des bestehenden Systems das Einfachste gewesen. Doch mit dem einfachsten Weg geben wir uns nicht immer zufrieden, vor allem dann nicht, wenn bessere Alternativen verfügbar sind. Wie in diesem Fall Tebis.“
Einerseits war Tebis bei einem Großteil der Riemann-Kunden im Einsatz. Andererseits hielten die Geschäftsführer und das Programmiererteam Tebis immer für eine High-End-Lösung. Auch andere Unternehmen, bei denen sich das Riemann-Team zuvor informiert hatte, teilten diese Meinung.
Letztendlich lief es auf einen Show-down zwischen den beiden CAD/CAM-Systemen hinaus. Beide Softwarehersteller wurden damit beauftragt, identische Werkstücke zu programmieren. Das erste Teil sollte ohne jeglichen Zeitdruck über mehrere Wochen programmiert und bis zum „Geht-nicht-mehr“ optimiert werden. Ein zweites Werkstück sollte vor Ort programmiert und umgesetzt werden. Eigens dafür hatten die Werkzeugbauer ein Beispielwerkstück kreiert – eine Warmumformbacke, die alle Merkmale typischer Bauteile sehr gut abbildet.
Um es kurz zu machen: In beiden Disziplinen hieß der klare Sieger Tebis, insbesondere auch deshalb, weil das Team der Martinsrieder Softwareschmiede exzellent vorbereitet und äußerst kompetent besetzt war, um die Live-Aufgabe mit Bravour zu lösen. Für die Geschäftsführung bei Riemann zählte der Gesamteindruck. Und der passt bei Tebis.
Die Entscheidung zahlte sich schnell aus: Ein Vierteljahr nach Implementierung und Schulung lief das erste mit Tebis regulär selbst programmierte Kundenteil auf der Maschine. Nach einem weiteren halben Jahr waren alle Programmierabläufe auf Tebis umgestellt. Einer der bisher im alten System aktiven Programmierer erlernte den Umgang mit der neuen Software. Zudem konnte das Unternehmen einen weiteren jungen Tebis-Programmierer einstellen.
Wie sich schnell herausstellte, war dies die ideale Kombination aus Berufserfahrung und Kompetenz: „Unser bisheriger Programmierer kennt ja unsere Teile aus dem Effeff, und der Neue war fit in Tebis“, berichtet Michael Riemann. „Beide konnten sich gegenseitig unterstützen und weiter voranbringen.“
Der Unterschied zwischen dem alten System und Tebis war deutlich. „Kurz nach der Umstellung kam einer der für uns bislang größten Lohnfertigungs-Aufträge ins Haus“, erinnert sich der Geschäftsführer. „Da sahen wir das erste Mal sehr deutlich, wie viel Zeit wir mit Tebis sparen – und das im Alltagsgeschäft.“
Nach der ersten Implementierungsphase – zwei Programmierlizenzen sowie sechs Viewer – kam sehr bald ein weiterer Programmierplatz hinzu. Inzwischen sind die neueste Tebis-Version 4.1 sowie diverse Zusatzpakete im Einsatz. Auch personell hat das Unternehmen in der Folge aufgestockt: So wurde für Tebis zwei neue Programmierer zusätzlich eingestellt. Derzeit ist eine weitere Aufstockung der Abteilung in Planung.
Der Unternehmer freut sich darüber, dass Tebis das verlässliche und belastbare Rückgrat hochpräziser Werkzeuge ist. „Mit unseren komplizierten Werkstücken treiben wir die Maschinen und auch die Programmierung durchaus in Grenzbereiche“, so Michael Riemann. „Umso wichtiger ist es für uns und unsere Konstrukteure, auch in den Experten der Tebis-Hotline erfahrene Sparringspartner gefunden zu haben, die gemeinsam mit uns proaktiv nach Lösungen suchen, wenn wir an Grenzen stoßen.“
Angesichts zunehmender Komplexität sind die umfassenden Simulationsmöglichkeiten bei Tebis ein großer Pluspunkt für die Werkzeugmacher. Sich auf die vom Hersteller vorinstallierten ‚virtuellen Maschinen‘ der Bearbeitungszentren zu verlassen, kommt für das Familienunternehmen nicht in Frage. Das Arbeiten mit sehr progressiven Parametern und das Fahren millimetergenauer Eilgänge erfordern absolute Sicherheit und Verlässlichkeit in der Software hinsichtlich der hundertprozentigen Umsetzung der Maschinenmodellmaße in die Realität.
Deshalb haben die Werkzeugmacher einen kompletten 3D-Scan über ihre Maschinen laufen lassen. Dazu wurden auch sämtliche Spannmittel und andere relevanten Komponenten digitalisiert. Für Michael Riemann ist dies unabdingbar, denn nur so kann sichergestellt werden, dass auch in der virtuellen Welt die komplette Realität bis zur letzten Schraube exakt abgebildet wird.
Auch bei den eingesetzten Präzisionswerkzeugen arbeiten die Werkzeugmacher mit Ist-Daten. Und das gilt letztlich auch für den Rohling. So können sich die Zerspaner darauf verlassen, dass die Bearbeitungsergebnisse exakt dem entsprechen, was sie vorher simuliert haben. „Unsere Programmierer ‚fräsen‘ letztendlich mit dem ‚echten‘ Fräser auf der ‚echten‘ Fläche des ‚echten‘ Bauteils“, erläutert Michael Riemann. „Die Arbeit mit Echtdaten schafft eine hohe Prozesssicherheit – und das ist ein großes Plus auch in Sachen Termintreue dem Kunden gegenüber.
Ganz papierlos ist die Fertigung bei Riemann noch nicht. Aber die Papierzeichnungen tragen beispielsweise keine Informationen mehr zu den Maßen. Gültig und aktuell sind ausschließlich die in Tebis hinterlegten Datensätze. Tebis-Viewer sind daher an allen Maschinen im Einsatz.
Die sehr gut ausgebildeten Mitarbeiter, die teilweise die 2,5D-Programmierung direkt an den Maschinen ausführen, weiß Michael Riemann sehr zu schätzen. „Es kommt durchaus vor, dass die Programme ins System geladen werden und dann der Bediener beispielsweise noch die DXF-Kurven ableitet. Das Gute ist: Tebis bietet das alles in einem einzigen durchgängigen System.“
Im Normalfall aber sind die Programme fertig. Toleranzen und weitere Parameter werden in der Regel über die Farbcodierungen der OEMs bestimmt. Da die meisten von ihnen in ihrer Arbeitsvorbereitung ebenfalls mit Tebis arbeiten, ist das Konvertieren von Daten nicht notwendig. Darin sieht das Unternehmen einen wichtigen Vorteil.
„Wenn ein Kunde beispielsweise als Notiz hinzufügt: ‚Achtung! Nicht 10H7, sondern 8H7‘, dann ist jetzt auch sicher, dass das alle sehen, die es betrifft“, erklärt Michael Riemann. Bei konvertierten Daten ist das nicht immer gewährleistet. Deshalb bringt die durchgängige Arbeit mit Tebis auch den Kunden ein gutes Plus an Stabilität in den Gesamtprozessen. Sicher war dies auch ein Grund, warum die OEMs dazu geraten haben, dieses CAD/CAM-System einzusetzen.
Tebis ist für die Werkzeugmacher der Türöffner für viele neue Möglichkeiten. Im Vergleich zum alten CAD/CAM-System haben sich die Spindellaufzeiten im Verhältnis zu den Programmierzeiten drastisch erhöht. Mit Tebis schaffen die Programmierer viel mehr Teile pro Person als vorher. Die Programmierzeiten haben sich bezogen auf vergleichbare Teile in etwa halbiert. Das ist gerade angesichts des Zeitdrucks im Werkzeugbau ein nicht zu unterschätzender Vorteil, denn insbesondere in der Automotive-Industrie ist die Durchlaufzeit der Werkzeuge in der Vergangenheit immer relevanter geworden.
Das Riemann-Team fertigt dank Tebis nicht nur deutlich komplexere Teile als vorher, sondern traut sich inzwischen auch deutlich mehr zu. Aufgrund der Möglichkeiten des Programmpakets können andere Aufträge annehmen, bei denen die Werkzeugbauer nicht so leicht zu ersetzen sind. „In der Arbeit mit den Möglichkeiten des CAD/CAM-Systems haben wir uns bisher eine Menge Know-how erarbeitet“, erklärt Michael Riemann. „Das setzen wir für unsere Auftraggeber ein und versuchen, die Grenzen des Systems auszuloten.“
Deshalb treiben die Programmierer ihre Maschinen, aber auch das CAD/CAM-System, nicht selten in Grenzbereiche, gehen bei ihren Programmen durchaus ans Eingemachte. Der große Vorteil: „In der Tebis-Hotline sitzen Experten, die wir fordern können“, bestätigt der Unternehmer. „Unsere Programmierer nehmen es sehr genau. Bei Tebis finden sie Ansprechpartner, die genau denselben Ehrgeiz entwickeln und mit denen zusammen sie die optimale Lösung finden können. Und das ist für die eigene Entwicklung und die künftige Wettbewerbsfähigkeit in unserer Branche sehr viel wert.“
Kontakt: