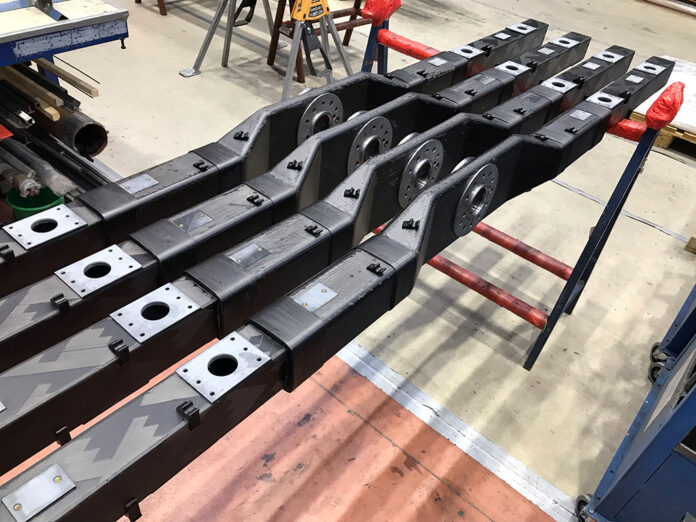
Im Rahmen des jüngsten Entwicklungsprojekts von CompoTech PLUS und Bilsing Automation (Attendorn, Deutschland) haben die beiden Unternehmen ein End-Of-Arm-Tooling (EOAT) aus Kohlefaser-Verbundwerkstoff für eine Tandem-Pressenlinie mit Saugvorrichtungen für die Automobilindustrie produziert.
Dieser EOAT-Typ wird im Englischen wegen seiner Geometrie normalerweise als „Gondola Beam“ (Gondelträgerbalken) bezeichnet. Er verfügt über zwei symmetrische quadratische Balken, die an einem flachen Mittelkörper angebracht sind. Die Arme, die die Saugvorrichtungen halten, werden am Gondelträgerbalken mithilfe von Werkzeugnestern befestigt.
Das Projekt wurde von einem führenden Hersteller von Automobil-Karosserieplatten ins Leben gerufen, der nach einem alternativen maßgeschneiderten Gondelträgerbalken suchte, um einen vorhandenen hybriden Balken aus Aluminium-Kohlefaser-Verbundwerkstoff zu ersetzen.
Das Hauptziel des Projektteams war die Vereinfachung der Werkzeugverwaltung. Zu diesem Zweck sollte ein steiferes, längeres EOAT entwickelt werden, welches die nötige Austauschbarkeit der standardmäßigen Saugvorrichtungs-Werkzeugnester in der gesamten Fabrik ermöglichen würde.
Der neue ausschließlich aus Kohlefasern hergestellte, 2,6 Meter lange, niedrige Gondelträgerbalken ermöglicht eine höchst vorteilhafte Standardisierung der One-Touch-Adapter- (OTA) Werkzeugnester in der gesamten Fabrik zwischen den verschiedenen zum Einsatz kommenden EOAT-Typen. Als Folge konnten die Montagezeiten der Werkzeugnester sowie die mit dem OTA zusammenhängenden Wartungs-, Teile- und Lagerkosten um die Hälfte reduziert werden.
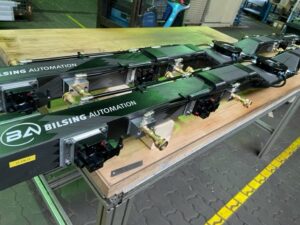
Zu den wichtigsten Produktionsvorteilen des Projekts gehören eine höhere Tragfähigkeit sowie eine dramatisch verbesserte Produktivität, so dass die bei der ursprünglichen Gondel aus hybridem Metall-Verbundwerkstoff bestehende Begrenzung von neun Hüben pro Minute überwunden werden konnte. Dank der steiferen komplett aus Verbundwerkstoff bestehenden Gondel konnten Pressenlinien nun mit einer um über 75 % erhöhten Geschwindigkeit – mit bis zu 16 Hüben pro Minute – betrieben werden.
CompoTech verfügt über bewährtes Design- und Herstellungs-Know-how, wenn es um den Bau innovativer Werkzeugmaschinen aus Kohlefaser-Verbundwerkstoff und Automatisierungslösungen zum Ersetzen von Stahl und Aluminium geht. Mit der proprietären Technologie zur automatischen Faserverlegung kann CompoTech steifere und leichtere alternative Bauelemente mit besserer natürlicher Frequenzdämpfung anbieten, die die Produktivität beträchtlich erhöhen, während die allgemeinen Herstellungskosten gesenkt werden.
Bilsing Automation ist weltweiter Marktführer in den Bereichen Automobilstanzen und EOAT-Werkzeuge für Karosseriewerkstätte sowie Entwicklung innovativer modularer industrieller Werkzeugsysteme. Das Unternehmen hat eine führende Position auf dem Markt für automatische Werkzeuge, in denen Kohlefaser-Verbundwerkstoffe zum Einsatz kommen, kollaborativ entwickelt und hergestellt von CompoTech.
Neues Design zur Erfüllung der Gondelparameter
CompoTech hat ein neues Laminatdesign entwickelt. Bei diesem Design werden zwei Typen von Kohlefasern verwendet, um die erforderlichen Designparameter für standardisierte EOAT für Tandem-Pressenlinien in der Fabrik zu erfüllen. Die Designspezifikation basierte auf realen Pressenlinien-Daten aus der Fabrik. Im KF-Epoxidlaminat für jeden Abschnitt der neuen Gondel wird eine Kombination aus PAN-Gewebe und axialen Pechfasern verwendet. Diese werden mittels der AFL-Technologie des Unternehmens an genau festgelegten Stellen platziert.

Die neue Gondel hat eine Gesamtbreite von 2,6 m, muss mit Nutzlasten von bis zu 100 kg fertig werden und mit einer Beschleunigung von 2 G (~20 m/s2) bei minimaler Verformung betrieben werden können – sowohl vertikal, als auch horizontal (senkrecht zur Strahlachse).
Beim Anbringen unterhalb einer linearen Achse wird die Pressenlücke dank der niedrigen Struktur minimiert, was zu einer Verkürzung der Verarbeitungszeit führt. Dabei ist die lineare Bewegung eine maßgeschneiderte 7. Achse der 6-achsigen Tandem-Zuführroboterarme, die an den vorhandenen Pressenlinien installiert sind. Sie ermöglicht eine schnellere und effizientere Plattenübertragung und verbessert die Reichweite der 6-Achsen-Basis-Robotereinheit.
Kombinierte Kohlefaser-Technologien
Der Gondelträgerbalken aus Kohlefaser-Verbundwerkstoff besteht aus drei Abschnitten: zwei hohlen quadratischen KF-Balken (80 mm x 80 mm) mit einem verjüngten mittigen KF-Körperabschnitt, der sich aus zwei Hälften (oben und unten) zusammensetzt. Die einzelnen drei Abschnitte werden daraufhin miteinander verklebt und an den kritischen Stellen mit zusätzlichen Fasern umwickelt, um zusätzliche Verstärkung zu gewährleisten.
Das Gewicht des gesamten Verbundwerkstoff-Gondelträgerbalkens beträgt nur 14 kg. Nach dem Zusammenbau und nachdem die Armatur zum schnellen Werkzeugwechsel und die standardmäßigen Saugvorrichtungs-Werkzeugnester angebracht wurden, beträgt das Gewicht des betriebsbereiten EAOT 35 kg.
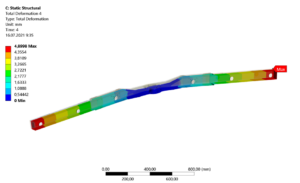
In jedem Kohlefaser-Abschnitt kommen sowohl unidirektionale axiale Pech-Kohlefasern mit hohen Elastizitätsmodulen, als auch hochfeste PAN-Fasern mit unterschiedlichen Laminatschicht-Kombinationen im oberen und unteren Teil sowie an den Seiten zum Einsatz.
Pads aus Verbundwerkstoff werden an Schlüsselstellen entlang der Strukturträger verklebt und bearbeitet, um für die Montage des EOAT-Werkzeugnestes eine präzise Oberfläche zu gewährleisten. Im Rahmen dynamischer Belastungsprüfungen der vollständig zusammengebauten KF-Gondel wurde die hohe Steifigkeit des Laminatsystems bei einer maximalen Verformung von nur 4,9 mm bestätigt.
Gabriel Martinot, leitender Konstrukteur von CompoTech, erklärte, wie das Unternehmen das Projekt anging, um sicherzustellen, dass alle Konstruktionsparameter erfüllt wurden: „Die Herausforderung bestand darin, eine Gondel mit dem Mittelteil zu entwickeln, der eine ähnliche Biegesteifigkeit wie die 80 mm x 80 mm Profilträger hätte, und Bereiche mit Spannungskonzentration zu vermeiden. Ultradichte Pechfasern sollten den geometrischen Steifigkeitsverlust ausgleichen.“
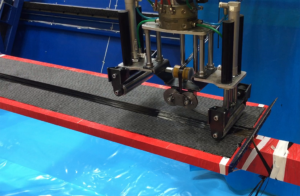
„Zu diesem Zweck haben wir Vorformen aus Kohlefaser-Gewebe mit ultrahohem Elastizitätsmodul für den Mittelkörper entwickelt. Mit unserem AFP-Verfahren können wir ultrahohe XN-80 Pechfasern automatisch und präzise auf dem PAN-Gewebe stapeln, um axiale 0-Grad-Pech-Kohlefasern mit standardmäßigem +/-45°-PAN-Gewebe zu kombinieren. So konnte die maximale Steifigkeit im Mittelbalken genau dort gewährleistet werden, wo sie benötigt wurde.“
Gabriel erklärte die anderen Herstellungsetappen der neuen Gondel aus Kohlenfaser-Verbundwerkstoff: „Die Hälften des Mittelkörpers sowie die zwei quadratischen Balkenabschnitte wurden zunächst miteinander verklebt und anschließend wieder in der AFL-Maschine platziert, in der zusätzliche 90-Grad-Kohlefasern gewickelt wurden, um den Träger an der am stärksten belasteten Stelle noch besser zu verstärken. Auf diese Weise wird eine zuverlässige und langfristige Leistung selbst bei extrem schweren Belastungen sichergestellt und jegliches Risiko einer Rissausbreitung zwischen den Bauteilen der Gondel-Baugruppe reduziert.“
Die in den Bereichen Maschinenbau und Automatisierung gewonnene Erfahrung sowie der neue Denkansatz von CompoTech, wenn es um die Verwendung der einzigartigen automatisierten Faserverlegungs-Technologie zur Lösung von Designproblemen geht, werden in anderen Branchen wie z. B. Verteidigung, Verkehr, Landwirtschaft, Radfahren und Freizeitschifffahrt eingesetzt.
Kontakt: