
Viele Branchen sind bereit, mit dem Laser neue Produktionswege zu gehen. Dazu müssen Anwender und Anbieter Digitalisierung und Nachhaltigkeit, Ökologie und Ökonomie in Einklang bringen. Ein wichtiges Mittel zum Zweck: Integration der Laser in die entstehenden Prozessketten, damit sie mit den vor- und nachgelagerten Prozessen ganzheitlich zusammenwirken. Wie proaktiv die Laser-Community diese Aufgaben bereits angeht, erfuhren die über 520 Teilnehmenden des AKL’22 International Laser Technology Congress in Aachen.
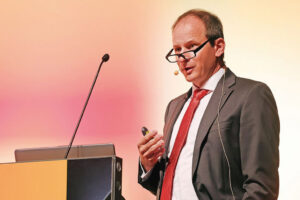
Deep Learning, Cloud Computing, Virtual Commissioning – drei von vielen neuen Begriffen auf dem AKL’22, die auf den Wandel des Lasereinsatzes hinweisen. Digitalisierung kam früher zwar auch auf den Aachener Insidertreffen der Lasercommunity vor, doch plötzlich war sie stets präsent: Überall entdeckten die AKL-Teilnehmenden ansatzweise, wie die digitale photonische Produktion (DPP) der Zukunft aussehen könnte.
Welche Eigenschaften zeichnet aber das Herstellen unter dem Kennzeichen DPP besonders aus – ist es effizient, prozesssicher, wettbewerbsfähig und zugleich selbstlernend? Einen neuen Begriff brachte Prof. Constantin Häfner, Leiter des Fraunhofer ILT, ins Spiel: »Nachhaltigkeit wird immer wichtiger als Entscheidungsattribut im Fertigungsumfeld. Nachhaltige digitale photonische Produktion ist ein Türöffner für Technologie-Souveränität, Innovation, Resilienz und Agilität.« Für die nachhaltige digitale photonische Produktion spreche viel: Sie helfe beim Umsetzen nachhaltiger Ziele und Regularien und stärke Europas Rolle als Hightech-Standort.
Laser – just for fun: Droht Konkurrenz durch Google & Co.?
Es ist Eile geboten, denn es droht der Laserindustrie Konkurrenz von den Großen der Digitalbranche. So sollen Apple, Google und Facebook momentan im großen Stil Laserphysiker einstellen, um »just for fun« nicht nur Autos, Raketen oder Satelliten, sondern demnächst auch Laser zu bauen. Diese erstaunliche Nachricht erfuhren die AKL-Teilnehmenden auf der traditionellen Gerd Herziger Session »Laserstrahlquellenentwicklung – Quo vadis?«.
Grund genug für die Laserhersteller, ihre Marktposition zu verbessern. So sprachen sich auf der Session Dr. Christian Schmitz (CEO Laser Technology, Trumpf), Mark Sobey (Executive Vice President und COO, Coherent) und Volker Krause (Geschäftsführer, Laserline) für sehr weitgehende Digitalisierung aus, ohne die kein Laserhersteller überleben könne. Großes Interesse daran zeigen auch ihre Kunden, die mithilfe von Daten aus den Laseranwendungen das perfekte Prozessfenster finden wollen, um die Wertschöpfung weiter zu erhöhen. Der Laser muss künftig klüger, einfacher in der Integration und im Gebrauch sein.
Gezielt den KI-Einsatz planen
Erstaunliche Erkenntnisse bot auch die anschließende Session zur »Digitalisierung in der photonischen Produktion« mit Dr. Joachim Döhner (Senior Director Global Sales, KUKA Systems), Dr. Jens Ottnad (R&D Head Data and AI, TRUMPF Werkzeugmaschinen) und Dr. Tobias Kamps (Corporate Technology, Siemens). Unisono stellten die Referenten fest, dass sich Unternehmer nicht mehr fragen sollten, ob sie digitale Tools wie KI einsetzen wollen. Nun gehe es nur noch um das Wann und Wie, denn nur mit gezielter, cleverer Digitalisierung lasse sich die Anwendbarkeit und der Nutzwert von photonischer Produktion weiter ausreizen.
Das Ziel ist attraktiv, der Weg dahin sei aber eine gefährliche Gratwanderung: Zum einen sollten Einsteiger das Thema nicht halbherzig angehen, sondern beim Digitalisieren auch die vor- und nachgelagerten Prozesse einbeziehen. Zum anderen sollten sie die Aufgabe aber auch nicht blauäugig angehen und übertreiben. Denn es drohe sonst die Gefahr, in »einem Meer von Daten zu ersaufen«.
Gefragt ist Digitalisierung vor allem, wenn Anwender Neuland betreten. Das betrifft in besonderem Maße die Additive Fertigung, die kurz davorsteht, nun auch die größte Hürde – den Einstieg in die automobile Großserie – zu nehmen. Aus den unterschiedlichen Blickwinkeln beleuchteten Hersteller u.a. von Raumfahrt-Triebwerken, Automobilen, Werkstoffen und Software auf dem Forum Additive Fertigung den Stand der Dinge. Ihre Kernbotschaft: Additive Fertigung ist zwar erwachsen, doch jetzt ist Feintuning angesagt.
Drei Tipps aus der 3D-Druck-Praxis
Schließt die Regelkette, empfahl Dr. Bart van der Schueren, CTO, Materialise NV, Leuven: »Obwohl der 3D-Druck von Natur aus ein digitaler Prozess ist, wird oft nur der Weg »CAD-to-Print« genutzt. Wenn der Anwender aber den Kreislauf schließt, kann er dank des Feedbacks effektiv in einen kontinuierlichen »plan-do-check-learn«-Prozess einsteigen.«
Senkt mit Simulation den Materialeinsatz, schlug Keno Kruse, Account Manager CADFEM GmbH, Hannover, vor: »Durch den Einsatz von Simulation können kritische Bereiche im Vorfeld identifiziert und Maßnahmen vor dem Druck ergriffen werden – das spart Zeit und Geld. Ansys bietet eine erstklassige Simulationssoftware zur Optimierung der LPBF-, DED- und Metal Binderjet Sintering-Prozesse.«
Achtet auf die Pulverauswahl und Steifigkeit, sagte Raphael Koch, Additive Manufacturing Research Engineer bei der Ford-Werke GmbH in Aachen mit Blick auf erste Erfahrungen beim Entwickeln von funktionellen LPBF-Prototypen für den Fahrwerksbereich: »Der Einsatz von Pulver vom Markt senkt den Aufwand an Entwicklungszeit und Kosten. Die gedruckten Bauteile sollten ähnliche Eigenschaften aufweisen wie herkömmliche Bleche für Fahrgestelle. Die Streckgrenze sollte 700 bis 800 MPa betragen, die Dehnung mehr als 10 Prozent und die Dichte 7,85 g/cm³.«
Zusammenspiel von EHLA und Parallelkinematik
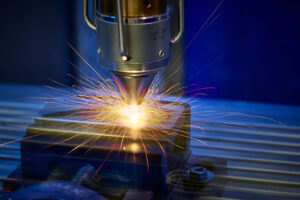
Interessante Perspektiven werden Anwendern durch Weiterentwicklungen geboten wie das Extreme Hochgeschwindigkeits-Laserauftragschweißen EHLA des Fraunhofer ILT, das sich bereits seit 2015 als schnelle, nachhaltige und hochpräzise Alternative zum konventionellen Beschichten von rotationssymmetrischen Bauteilen mehrfach im industriellen Einsatz bewährt hat.
Hochproduktiven 3D-Druck ermöglicht seit Kurzem der Einsatz der EHLA-Technik in einer Parallelkinematik (max. Vorschub: 200 m/min; max. Beschleunigung: 50 m/s²) der Firma Ponticon GmbH und in einem modifizierten 5-Achs CNC-Prototypen (30 m/min.; 20 m/s²). Mit der Ponticon-Maschine ließen sich z. B. erste Komponenten aus Edelstahl 316L mit 1,7 kg/h bei einem Vorschub von 40 m/min. schnell und zuverlässig drucken.
Sehr beeindruckend sind auch Kennwerte der CNC-Anlage: Auf ihr entstand z. B. ein Bauteil aus dem bekannten Luftfahrtwerkstoff Inconel 718 mit hoher Dichtigkeit (> 99,7 %) und einer Auftragrate von 2,3 kg/h. »Die Materialeigenschaften sind vergleichbar zu konventionell hergestellten oder mit anderen 3D-Druckverfahren hergestellten Bauteilen«, konstatierte Min-Uh Ko, Gruppenleiter Systemtechnik am Fraunhofer ILT.
»Die exakten Materialkennwerte der untersuchten Materialien, darunter Aluminiumlegierungen für die Leichtbauanwendung, sind ähnlich hoch und fallen sogar teilweise höher aus als beim konventionellen Verfahren.« Interessanterweise lässt sich übrigens auch recyceltes bzw. aufgesammeltes Pulver mit ähnlich guten Resultaten verwenden.
LPBF: XXL im Visier
Große Bauteile entstehen auch auf einer anderen Maschine, auf die Jasmin Saewe, Leiterin der Abteilung Laser Powder Bed Fusion (LPBF) am Fraunhofer ILT hinwies: »Die auf Gantry-Bauweise basierende Prototypmaschine zeigt, wie sich nicht nur die Produktivität, sondern auch die Skalierbarkeit unseres patentierten laserbasierten Pulverbettverfahrens deutlich erhöhen lässt.« Die Aachener erhöhten die Produktivität durch die Vervielfachung der Laserstrahlen, um die Zeit für den 3D-Druck-Prozess zu verkürzen.
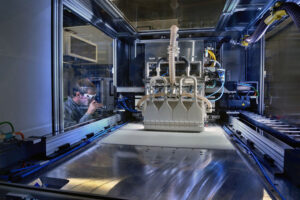
Das Konstruktionsprinzip erläuterte Tim Lantzsch, Leiter der Gruppe Process & Systems Engineering am Fraunhofer ILT: »Statt einer festen Position für die Laserscanner verwenden wir einen beweglichen Bearbeitungskopf mit integriertem Schutzgas- und Optiksystem, der mit einem Portalsystem über dem Pulverbett verfahren wird.«
Mit der Anlage lassen sich sehr große Bauteile bis zu einer Größe von 800 mm mal 1.000 mm drucken, die bis zu 350 mm hoch sind. »Für uns ist es wichtig, zu zeigen, dass sich mit ihr auch industrielle Anwendungen adressieren lassen und außer Edelstahl auch viele weitere metallische Werkstoffe verarbeitet werden können«, betonte Lantzsch. »Wir wollen nun mit industriellen Partnern neue Anwendungen für das LPBF entwickeln.«
Mit dem Einstieg vieler Branchen in den 3D-Druck gewinnt dessen Integration in konventionelle Produktionslinien zunehmend an Relevanz. Doch diese neuen hybrid-additiven Prozesse sind nicht nur vielversprechend hinsichtlich Flexibilität und Resilienz der Lieferketten – es stellen sich auch neue Herausforderung in der Automatisierung. Auf adaptive Fertigung setzt Jan Bremer, Leiter für Forschung und Entwicklung (FuE) bei der BCT GmbH in Dortmund.
In Verbindung mit maschinenintegrierter Messtechnik verwandelt sich eine Produktionsanlage in eine Messmaschine, welche die Geometrie der Bauteile und prozessparallel auch Prozessdaten erfasst und mithilfe von optimierten Algorithmen auswertet.
Inline-Qualitätssicherung: Analyse während des Fertigungsprozesses
Wie eine solche Lösung aussehen kann, zeigt das Forschungsprojekt »DigitalCMM – Digital Coordinate Measurement Machine«, in dem ein Konsortium mit den Firmen Camaix, Point 8, oculavis sowie BCT und dem Fraunhofer-Institut für Produktionstechnologie IPT ein Konzept für Auswertung von maschinenintegrierten Messdaten in der Frästechnik entwickelte.
Dabei konnte mit einer gemeinsamen Lösung der Partner BCT als Softwarehersteller und Point 8 als KI-Spezialist im Konsortium die ortsaufgelöste und hochfrequente Erfassung von Prozessdaten in einer 5-achsigen Fräsmaschine demonstriert werden. Eine KI-basierte Analyse der erfassten Daten erlaubt dabei Rückschlüsse auf die Prozessqualität der individuellen Bauteile.
Durch die ebenfalls an die Software angebundene, geometrische Messtechnik innerhalb der Maschine, im Projekt ein Messtaster, können so Prozesseigenschaften und Bauteilgeometrie automatisiert erfasst und analysiert werden.
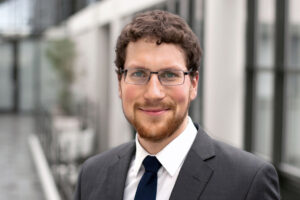
Doch wie geht man generell mit dem ständig wachsenden Datenvolumen um, welches z.B. in Sensornetzwerken gesammelt wird? »Durch geeignete Datenerfassungs-Strategien wächst der auswertbare Informationsgehalt und eine zunehmende Automatisierung der Auswertung wird möglich« blickte der Entwicklungsleiter Jan Bremer zuversichtlich in die Zukunft. »Vielleicht brauchen wir künftig in der Produktion nur noch deutlich geringere Datenmengen, da geeignete Algorithmen und maschinenintegrierte Datenerfassung Hand in Hand gehen, um relevante Aussagen mit gesteigerter Effizienz zu treffen.«
Aktuell laufende Forschungsprojekte wie das Projekt »ProSLAM« untersuchen die Einbindung einer Großzahl verschiedener Sensoren für Prozess und Geometrie sowie deren Zusammenführung mit externen Messdaten wie beispielweise CT-Aufnahmen additiv gefertigter Bauteile. Bremer erwartet dabei große Fortschritte für das Prozessverständnis und die darauf aufbauende benutzerfreundliche Automatisierung von Entwicklungs- und Produktionsprozessen durch die Etablierung maschinenintegrierter Sensornetzwerke.
Aufwändige Big Data-Analyse demnächst überflüssig?
Die intelligente und adaptive Erfassung der gesamten Prozesskette könne auch helfen, Lieferketten zuverlässiger zu machen. »Wenn jedes einzelne Modul der Prozesskette adaptiv und intelligent arbeitet, kann beispielsweise der Ausfall eines Gießprozesses problemlos durch ein additives Verfahren ersetzt werden«, nannte Bremer die spannende Alternative. »Der Ausfall ist dann unproblematisch, da die adaptive Prozesskette automatisch auf den Ersatz reagiert und sich darauf einstellt, um das gewünschte Endergebnis zu erzielen.«
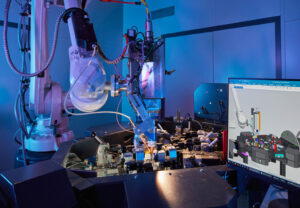
Um hybrid-additives Neuland geht es auch im EFRE.NRW-Projekt MultiPROmobil. Unter der Koordination des Fraunhofer ILT entstanden multifunktionale Laserwerkzeuge zum Schneiden, Schweißen und Auftragschweißen mit Draht (w-LMD), die bei den Vorführungen am Fraunhofer ILT während des AKL’22 für viel Interesse sorgten: Zum Einsatz kommen sie in einer Zelle für multifunktionale Laserroboter-Technologie, die im Zusammenspiel mit digitalem Zwilling für die flexible und wirtschaftliche Fertigung von Blechbaugruppen für Elektrofahrzeuge ausgelegt ist.
Treibender Faktor ist der Trend zu kleinen Losgrößen, vielen Varianten und dynamischen Produktlebenszyklen. Dies hat zur Folge, dass die Komplexität in der Konstruktion und beim Funktionsumfang steigt. Daher setzen die Projektpartner auf die Vorteile der digitalen Transformation. »Das Ganze mündet in einer flexiblen und rekonfigurierbaren Arbeitszelle mit skalierbaren Fertigungssystemen und Profinet-Anbindung zum digitalen Zwilling«, beschrieb ILT-Wissenschaftler Martin Dahmen das Ziel.
Multifunktionaler Bearbeitungskopf passt sich an
Im Mittelpunkt steht ein multifunktionaler Bearbeitungskopf, der sich bereits bei der Testproduktion bei einem semi-bionischen Leichtbauteil bewährt hat: Der Kopf schneidet, schweißt und verstärkt mit additiven Strukturen den konstruktiv optimierten Dreieckslenker eines Elektrofahrzeugs. Das alles geschieht sehr schnell ohne Werkzeugwechsel dank des luftgekühlten Kombikopfes, der sich mit autonomer Düse und einer adaptiven Strahlformungsoptik an die drei unterschiedlichen Bearbeitungsvorgänge schnell anpasst.
In einer virtuellen Inbetriebnahme (VIBN) optimierten die Projektpartner das Zusammenspiel der Bearbeitungsschritte. Für diese Vorgehensweise spricht laut Dahmen, dass sich dank VIBN die Zeitaufwände für die Ablaufplanung des Fertigungsprozesses und die Inbetriebnahme verkürzen, die Kosten senken und die Qualität der Steuerungssoftware erhöhen lassen.
Doch zuvor steht dann stets virtuelle Fleißarbeit an: Im Detail schilderte Dahmen den anspruchsvollen Konfigurationsprozess auf der Siemens-Simulations-Plattform SIMIT. Dieser reicht von der SPS- und Roboter-Programmierung, der Abbildung der Sensor-Kommunikation, umfangreichen Schnittstellen-Experimenten bis hin zu virtuellen Probeläufen mithilfe simulierter Testprozeduren (Software/Hardware in the loop).
Schnittstelle zum Menschen
Eine besondere Herausforderung ist das Zusammenspiel von Mensch und Roboter, denn der Betrieb läuft nicht nur automatisch, sondern teilweise auch manuell ab. »Wir müssen manuelle Funktionen mit dem Automatikbetrieb zusammenbringen«, erklärte Dahmen. »Dazu steht vor der Bearbeitungszelle als Benutzerschnittstelle ein Bedienpanel, auf dem das Bedienungspersonal manuell eingreifen kann oder den Prozess z. B. bei Werkstückwechsel starten kann.«
Gestern ILT, heute IoL
Auf diesen einfachen Nenner lässt sich das neueste Engagement von Professor Reinhart Poprawe, bis 2019 Leiter des Fraunhofer ILT, bringen. Vor fünf Jahren meldete Poprawe als Miterfinder ein Patent zum laserbasierten Herstellen von Kunststoff-Linsen (intraokulare Linsen IoL) an.
Auf dieser Basis entstand in Alsdorf bei Aachen die Firma AIXlens GmbH, die individuell angepasste Linsen materialunabhängig aus Kunststoff in einem volldigitalisierten und komplett laserbasierten Prozess herstellt. Der Patient erhält just-in-time ohne Lagerung direkt aus der Produktion in Losgröße eins seine persönliche Linse, die alle Fehlsichtigkeiten patientenspezifisch korrigiert.
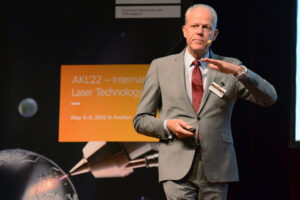
Hier kommt die Stärke des Lasers ins Spiel: die präzise, produktive und nachhaltige Herstellung von Bauteilen in hoher Komplexität und in kleinen Stückzahlen. Nach dem Vermessen des Auges und der Generierung der Daten entsteht die Linse innerhalb von wenigen Minuten: Ein Ultrakurzpuls (UKP)-Laser erzeugt per Abtragen die Linse, die dann mit einem CW-laser poliert wird.
Anschließend schneidet ein UKP-Laser die sogenannte Haptik zum Befestigen der Linse. »Es ist eine komplett digital geregelte Prozesskette, in der nichts mehr angefasst wird«, erklärte Poprawe. »Wenn jemand die Linse bestellt, hängt der Liefertermin nun im Prinzip nur noch von der Versandzeit ab.«
Produktion ohne Mitarbeiter
Ungewöhnlich ist auch das Geschäftsmodell: Bei AIXlens gibt es keine Mitarbeiter, denn die Entwicklung des Prozesses und die Einrichtung einer Demonstrationslinie erledigt im Auftrag das Fraunhofer ILT. Sehen lassen können sich die Eckdaten: In Losgröße eins entstehen Linsen mit einer Oberflächenrauheit im Bereich einzelner Nanometer und sehr genau eingehaltenen Dioptrienwerten.
AIXlens musste bei dem national und international patentierten Prozess allerdings ein besonderes technisches Problem lösen: Es bilden sich beim Laserpolieren von Duroplasten winzige Polymerketten, wegen denen die Linsen den Biokompatibilitäts-Test zunächst nicht bestanden. Für Abhilfe sorgt die Bestrahlung der laserpolierten Linsen mit Elektronen, welche die gebrochenen Molekülketten wieder miteinander verbindet. Seitdem bestehen die Linsen auch den Biokompatibilitäts-Test.
Der Aufwand hat sich gelohnt, denn die so entstandene neue Form der IoL-Produktion bietet völlig neue Möglichkeiten. »Bei der konventionellen Produktion müssen die Hersteller Linsen in 400 verschiedenen Größen ständig auf Lager haben, das sie wegen des Verfallsdatums der Produkte ständig auffüllen müssen«, erläuterte Poprawe. »Das entfällt alles bei uns.«
Während die IoL-Linsen für Menschen mit grauem Star infrage kommen, brauchen wegen Augenhochdruck an grünem Star (Glaukom) leidende Patienten Mikro-Stents, die das Kammerwasser in den natürlichen Abflusskanal ableiten. Auch diese nur 300 µm hauchdünnen Bauteile lassen sich mit dem Laser herstellen: Zum Einsatz kommt bei der aixtent GmbH, ebenfalls aus Alsdorf, das Laserätzen von Glas (Selective Laser-induced Etching SLE). Details verriet der ehemalige Fraunhofer ILT-Chef nicht, aber auch das Laserätzen dürfte in einen Prozess integriert sein, der wie die IoL-Herstellung agil und voll digitalisiert im engen Zusammenspiel mit dem Fraunhofer ILT abläuft.
Auf einen für den Erfolg entscheidenden Faktor ging der Physiker nicht konkret ein: den Preis. Weil die Serienproduktion noch nicht angelaufen ist, will Unternehmer und Miterfinder Poprawe noch keine exakten Zahlen nennen, doch er ist mit Blick auf den bisherigen komplexen Herstellprozess und den hohen Aufwand für Logistik und Lagerung optimistisch: »Ich bin sicher, dass unsere Linsen deutlich preiswerter sein werden. Wir profitieren bei dem gesamten Prozess extrem von der Struktur auf dem RWTH Aachen Campus, ohne sie wäre das alles gar nicht möglich.«
Kontakt: