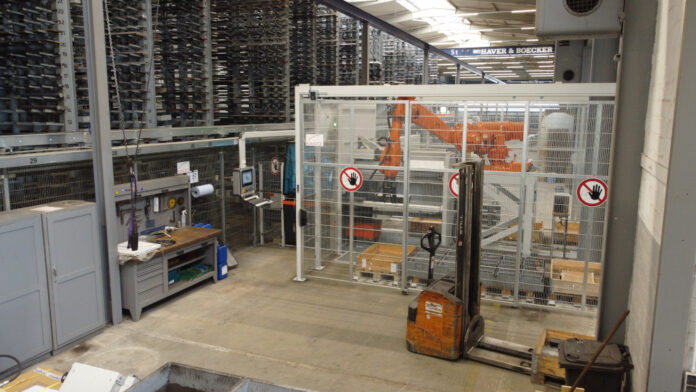
Aufbereiten, transportieren, lagern, mischen, abfüllen, verpacken, palettieren und verladen: Die HAVER & BOECKER Maschinenfabrik ist auf sämtliche Prozesse rund um die Handhabung und Verarbeitung von Schüttgütern spezialisiert. Das Portfolio des Unternehmens, dessen Wurzeln bis ins Jahr 1887 reichen, umfasst Pack- und Verladeanlagen für pulverförmige und granulierte Materialien, Packmaschinen für die Abfüllung von Lebensmitteln und Tiernahrung sowie Füllstationen und ganze Abfülllinien für flüssige und pastöse Produkte.
Hinzu kommen Siebmaschinen, Waschsysteme und Pelletierteller, Rührwerke und Mischer, Palettier- und Verladetechnik, Silos sowie Schiffsbe- und -entlader. Die einzelnen Prozessschritte werden zudem im eigenen Haus zu effizienten und integrierten Komplettlösungen vernetzt.
Die Maschinenfabrik ist einer von zwei Geschäftsbereichen des Unternehmens. Auch als Drahtweberei zählt HAVER & BOECKER zu den wichtigsten internationalen Adressen. Der familiengeführte Mittelständler mit Hauptsitz im westfälischen Oelde ist mittlerweile mit mehr als 50 Tochterunternehmen und 150 Vertretungen auf allen fünf Kontinenten tätig und beschäftigt weltweit rund 3.000 Mitarbeiterinnen und Mitarbeiter.
Eine knappe Autostunde von der Zentrale entfernt befindet sich der Unternehmenscampus von HAVER & BOECKER in Münster: Hier ist unter anderem der Metallbau der Maschinenfabrik ansässig, der für die Fertigung der Maschinen und Anlagen eine zentrale Rolle spielt. Der Standort beinhaltet die Blechverarbeitung, den Gestellbau, eine Strahl- und eine Lackieranlage – und ein Sägezentrum, bestehend aus einem automatischen Langgutlager und zwei nahtlos daran angeschlossenen Kreissägen.
Hohe Materialvielfalt und geringe Losgrößen
In dem sechs Meter hohen System lagern in 1.037 Fächern Rund- und Flachmaterialien, Rohre, Hohlprofile und Winkel in zahlreichen Querschnitten und Werkstoffen. „Als Sondermaschinenbauer haben wir es mit einer sehr großen Materialvielfalt, aber nur sehr geringen Losgrößen zu tun“, erklärt Christian Hinse, Work Preparation Manager bei HAVER & BOECKER OHG, bei einem Rundgang durch das Sägezentrum.
„Knapp ein Drittel der bei uns gesägten Teile sind Einzelstücke, bei 90 Prozent bewegen wir uns zwischen Losgröße eins und zehn.“ Verarbeitet werden hauptsächlich Stahl und Edelstahl, aber auch Aluminium und andere Metalle. „Das erfordert ein hohes Maß an Flexibilität und Effizienz, sowohl auf organisatorischer als auch auf technischer Seite“, führt Hinse weiter aus.
Das Sägezentrum stammt aus dem Hause KASTO Maschinenbau und wurde bereits 1998 installiert. Nach mehr als 20 Jahren im Einsatz war es jedoch in vielerlei Hinsicht nicht mehr auf dem aktuellen Stand. „Die damals verbaute SPS war unter anderem abgekündigt; die Ersatzteilversorgung gestaltete sich immer schwieriger“, erinnert sich Claudia Bürger, Projektmanagerin bei HAVER & BOECKER OHG.
„Auch hatten wir mittlerweile SAP im Unternehmen eingeführt, jedoch wurde das bestehende System nur mittels FTP an SAP IM angebunden. Es fehlte dadurch an Transparenz bei den aktuellen Lagerbeständen.“
Die damalige voll integrierte Sägemaschine, eine Produktionskreissäge von KASTO, war ebenfalls stark verschlissen und am Ende ihrer Lebenserwartung angekommen. „Die Maßhaltigkeit beim Sägen war nicht mehr gegeben, somit hatten wir Qualitätseinbußen bei den Ergebnissen und einen hohen Nacharbeitsaufwand zu verzeichnen“, beschreibt Bürger. „Es war also klar, dass wir hier etwas tun mussten.“
Modernisierung wirtschaftlicher als Neubau
Nachdem im Frühjahr 2019 die konkreten Anforderungen intern definiert wurden, setzten sich die Verantwortlichen von HAVER & BOECKER mit KASTO zusammen. Gemeinsam entschieden sie, das Sägezentrum umfassend zu modernisieren, damit dieses den aktuellen Ansprüchen wieder gerecht wird. „Der Stahlbau des Langgutlagers war nach wie vor einwandfrei, ein kompletter Austausch wäre daher wirtschaftlich nicht sinnvoll gewesen“, erläutert Christian Hinse.
„Allerdings haben wir im Rahmen des Projekts einen zweiten Lagerbereich mit 320 Kassetten abgebaut. In diesem wurden Materialien aufbewahrt, die nicht in einem Kragarmlager gelagert werden können. Durch die Reduktion wurde zusätzlicher Platz in der Halle geschaffen und die teils doppelte Lagerhaltung eliminiert.“ Das Stangenlager erweiterte KASTO um drei Ständerreihen sowie um 60 Kassettenplätze innerhalb des Stangenlagers – so war die nötige Kapazität weiterhin gegeben.
Bei dem Regalbediengerät (RBG), das die bis zu 6,5 Meter langen Materialien selbstständig ein- und auslagert, war hingegen eine Modernisierung erforderlich. Die KASTO-Experten tauschten unter anderem die Schaltschränke, die Energiezuführung, die Mess- und Regeltechnik sowie die Hub- und Fahrwerksmotoren durch neue und zeitgemäße Komponenten aus. Auch die veraltete SPS ersetzten sie durch eine moderne S7-Steuerung.
„Die Modernisierung des RBG verdoppelte die Geschwindigkeiten von 30 auf 60 Meter pro Minute“, freut sich Bürger. Für die Lagerverwaltung kommt nun das KASTO-eigene Warehouse Management System KASTOlogic zum Einsatz. Dieses ist über eine gemeinsam definierte Schnittstelle an das bei HAVER & BOECKER eingesetzte ERP-System von SAP angebunden. „Das beschleunigt und verschlankt unsere Prozesse ungemein, da zum Beispiel Sägeaufträge nun auch an die Gehrungssäge elektronisch übermittelt werden“, verdeutlicht Bürger.
Aus drei mach zwei: Bessere Performance trotz weniger Anlagen
In Sachen Sägetechnik nutzte die Maschinenfabrik den Umbau nicht nur zur Erneuerung, sondern auch zur Optimierung: Anstelle von zwei manuellen Sägen, eine für Gerad- und eine für Gehrungsschnitte, die an das ehemalige Kassettenlager angebunden waren, und einer automatischen, an das Langgutlager angebundenen Kreissäge, sind nun zwei Sägemaschinen an das Langgutlager angebunden.
Eine davon ist die KASTOflex A, eine universell einsetzbare Kreissägemaschine für Materialien bis 150 Millimeter Durchmesser. „Mit diesem Modell können wir automatisch sowohl Gerad- als auch Gehrungsschnitte durchführen. Bei der Gehrungsinformationen gibt es dabei die Besonderheit der Datendurchgängigkeit vom 3D-Modell über das ERP-System bis in die KASTOlogic und die materialoptimierte Abarbeitung der Sägeaufträge. Das hat unsere Performance deutlich verbessert“, hebt Hinse hervor.
Die Materialzufuhr erfolgt über eine Übergabestation (Verfahrwagen mit Wechselstation). Auf dieser können Materialien für die abzuarbeitenden Sägeaufträge vorgelagert werden, während die Säge noch arbeitet. „Das spart Zeit und erleichtert die Arbeit“, weiß Hinse zu berichten. Von Hand oder per Hallenkran entnimmt der Bediener die zu sägenden Stangen, Rohre oder Profile aus der Übergabestation des RBG und legt sie auf die Rollenbahn der Säge.
Direkt daneben ist mit der KASTOvariospeed SC 15 eine CNC-gesteuerte, vollautomatisierte Produktionskreissäge aufgebaut. Sie ist zum Trennen von Vollmaterial, Profilen und Rohren in allen Qualitäten einschließlich schwer zerspanbarer Werkstoffe geeignet. Ihre schwere Bauart und die leistungsfähigen Komponenten ermöglichen dabei besonders präzise Sägeergebnisse. Das Material wird automatisch über eine Fördertechnikstrecke zugeführt.
Für die Entnahme und Ablage der Abschnitte ist die Säge mit dem Roboter-Handlingsystem KASTOsort verbunden. Ein Industrieroboter entnimmt mithilfe einer Kippvorrichtung die Werkstücke aus dem Arbeitsbereich der KASTOvariospeed und legt sie mit einem Löffel in einem von mehreren Behältern ab. Mit einem Vakuumgreifer holt der Roboter zudem Etiketten von einem Drucker ab und platziert diese in den jeweiligen Behältern, welche vorab durch die Mitarbeiter auf Paletten neben dem Roboter bereitgestellt wurden.
„Dadurch sind die Abschnitte direkt auftragsbezogen sortiert – ein Arbeitsschritt, den wir früher mit viel Aufwand manuell durchführen mussten“, erklärt Christian Hinse. Damit sind die Sägeteile sortiert, identifizierbar und bereit für den Weitertransport zum nächsten Bearbeitungsschritt.
Reibungsloser Umbau im laufenden Betrieb
Der Umbau fand im Herbst 2020 statt – im laufenden Betrieb und mitten in der Corona-Pandemie. „Vor dem Projektmanagement durch KASTO kann ich nur den Hut ziehen“, lobt Hinse. „Trotz der widrigen Umstände konnten wir unseren eng gesteckten Zeitplan einhalten, ohne dass es währenddessen zu Engpässen in unserer Fertigung kam.“
HAVER & BOECKER richtete für die Übergangsphase einen provisorischen Sägebereich mit einem provisorischen manuellen Lager ein. „Bis zu 15 KASTO-Mitarbeiter waren gleichzeitig bei uns und haben es ermöglicht, dass die neue Anlage schon nach drei Wochen in Betrieb gehen konnte“, ist Hinse beeindruckt. „Auch danach waren noch Service-Techniker vor Ort, um unsere Kollegen in die Bedienung einzuweisen und vereinzelte Startschwierigkeiten aus dem Weg zu räumen.“
Die beiden Sägen können über ein Terminal per Touch-Steuerung bedient werden – „und zwar so intuitiv und einfach, dass wir uns schnell damit zurechtgefunden haben“, schildert Claudia Bürger. Auch die Sicherheitstechnik ist mit modernen Lichtvorhängen und Einhausungen auf dem neuesten Stand, so dass Unfälle und Verletzungen nahezu ausgeschlossen sind.
Bei einer Störung kann KASTO sich per Remote-Zugriff auf die Anlage schalten und schnell Abhilfe schaffen. Als Alternative besteht mit KASTO VisualAssistance die Möglichkeit, die Mitarbeiter vor Ort per Smart Glasses und Livestream bei Reparatur- und Wartungsaufgaben zu unterstützen. „Bisher haben wir das aber nicht gebraucht, das System läuft problemlos und absolut zuverlässig“, hebt Claudia Bürger hervor.
Das Ergebnis kann sich sehen lassen
Mit dem Retrofit und der Erweiterung seines Sägezentrums konnte HAVER & BOECKER gleich mehrere Fliegen mit einer Klappe schlagen: „Wir haben unsere Prozesse optimiert und effizienter gemacht, wodurch wir nachhaltig Kosten einsparen“, zählt Claudia Bürger auf. „Wir haben mehr Überblick über unsere Bestände, können flexibler auf kurzfristige Änderungen reagieren und haben weniger Stillstandszeiten zu verzeichnen.“
Bei der Sägetechnik machen sich laut der Projektmanagerin vor allem die Möglichkeit für automatische Gehrungsschnitte, die präziseren Ergebnisse durch den Einsatz von Hartmetallsägeblättern und der reduzierte Kühlmittelverbrauch positiv bemerkbar. „Gemeinsam mit KASTO haben wir alles, was wir uns vorgenommen hatten, erreicht“, resümiert sie. „Ich bin mit der Zusammenarbeit und dem Ergebnis rundum zufrieden.“
Kontakt: