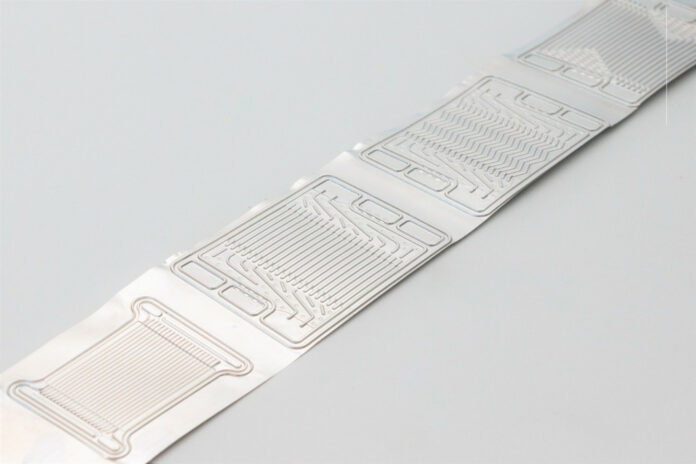
Damit Wasserstoff zu einer tragenden Säule in der klimaneutralen Energieversorgung werden kann, gilt es ihn zu marktwirtschaftlichen Preisen, in ausreichender Menge und klimaneutral herzustellen und mit hoher CO2-Minderungsquote zu verwenden. Wesentliche Wasserstoffsysteme müssen dafür in die industrielle Serienproduktion überführt werden.
Das betrifft insbesondere Elektrolyseure – in ihnen wird Wasser mit Strom z. B. aus Wind oder Sonne in Wasserstoff und Sauerstoff gespalten – und Brennstoffzellen, die den so gewonnenen Wasserstoff in elektrische Energie umwandeln. Als wesentliche Komponenten von Elektrolyseuren und Brennstoffzellen bestimmen Bipolarplatten (BPP) maßgeblich den Wirkungsgrad und die Herstellungskosten von Wasserstoffsystemen.
BPP stellen den eigentlichen Reaktionsraum in Form der Anode bzw. Kathode dar. Im Fokus der Referenzfabrik.H2 stehen Technologien, die eine industrielle Produktion mit erheblichen Fortschritten bei Verfahren, Digitalisierung und Kosten ermöglichen sollen.
Mit Forschung zu günstigeren Werkstoffen, zur Qualität der Bauteile, zur Langlebigkeit, zu besseren Produktionstechnologien, zur Skalierbarkeit der Produktionsverfahren, ihrer Automatisierung, der Vernetzung von Produktionslinien, dem Aufbau effizienter Lieferketten und zur Fabrikplanung soll die Großserienfertigung rentabel werden.
Dr. Ulrike Beyer, Leiterin der Wasserstoff-Taskforce am Fraunhofer IWU und Koordinatorin des Projekts: »Die Produktion muss einen entscheidenden Beitrag leisten, um dem Wasserstoff zum Durchbruch zu verhelfen. Genau daran arbeiten wir in der Referenzfabrik.H2.«
Die vom Fraunhofer IWU auf der EuroBLECH präsentierten Technologien und Exponate weisen allesamt einen Bezug zur Referenzfabrik.H2 auf, einschließlich Prozesssteuerung und Qualitätsüberwachung.
smartTOOL
Für Qualität und Produktivität in der Zerspanung kommt es mehr denn je darauf an, Prozesse möglichst nah an der Wirkstelle überwachen zu können. Der am Fraunhofer IWU entwickelte intelligente Werkzeughalter smartTOOL ist eine sehr wirtschaftliche und wegen seiner unabhängigen Energieversorgung auch zur Nachrüstung geeignete Lösung, um nah am Bearbeitungsgeschehen wertvolle Prozessdaten aufzunehmen.
So können Prozesskräfte, Schwingungen und Temperaturen erfasst, mit den passenden Algorithmen ausgewertet und in Prozesskennwerte überführt werden. Diese Kennwerte dienen wiederum als Basis zur Überwachung oder gar adaptiven Prozessregelung – smartTOOL hilft damit, auch ältere Maschinen datenbasiert fit für die Fertigung der Zukunft zu machen.
smartNOTCH: mit robusten, einfach zu installierenden Sensoren Stillstandszeiten von Pressen minimieren
Neue Werkstoffe, komplexe Geometrien von Bauteilen und kleine Losgrößen stellen hohe Anforderungen an Produktionsanlagen. Konzepte und Systeme für eine höhere Transparenz im Produktionsprozess helfen, die Produktion agiler und die steigende Komplexität besser beherrschbar zu machen. Ein Beispiel dafür ist smartNOTCH, das am Fraunhofer IWU entwickelte Überwachungssystem für Pressen und Umformprozesse.
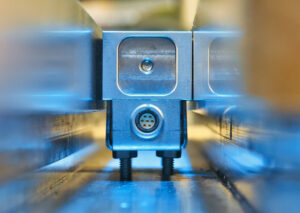
Ohne den Umformprozess oder die Maschineneigenschaften zu beeinträchtigen, können die Werkzeugspannstellen von Pressen dank smartNOTCH zu wertvollen Datenquellen für eine hochanpassungsfähige Produktion werden. Denn ein intelligenter Auswertungsalgorithmus steuert auf Basis dieser Daten sogleich die Prozess- und Qualitätsüberwachung während des Umformvorgangs.
Das Messkonzept von smartNOTCH ist verblüffend einfach. Die kleinen, besonders robusten Sensoren können mit einem Handgriff direkt in die T-Nuten installiert werden und sind für unterschiedliche Nutgrößen verfügbar. Somit wird es möglich, an mehreren Stellen im Pressentisch oder -stößel auch direkt unter dem Umformwerkzeug Informationen zu sammeln. Inline und robust.
smartNOTCH steigert die Transparenz über den Zustand von Anlage und Prozess (Condition Monitoring) und kann so als Digitalisierungsbaustein einen Beitrag zu neuen digitalen Geschäftsmodellen leisten, die Produktionsanlagen für eine agile, vernetzte Produktion fit machen.
XEIDANA: Qualitätskontrolle von Blechbauteilen durch AR-Projektion
Das Fraunhofer-Institut für Werkzeugmaschinen und Umformtechnik IWU präsentiert das Software-Paket XEIDANA, das die Qualitätskontrolle von Oberflächen übernimmt und als KI-basiertes, adaptives Werkzeug auch nicht bekannten Fehlern auf die Spur kommt. Abweichungen stellt es durch Projektionen auf das Bauteil (Augmented Reality) dar. Der Vorteil von XEIDANA: diese Kontrolle kann während der Produktion (inline) stattfinden, ohne dass das Bauteil ausgeschleust werden muss.
Ausblick Konti-BIP: Produktion metallischer Bipolarplatten in einem großserientauglichen Werkzeug- und Automatisierungskonzept
Im vom Bundesministerium für Digitales und Verkehr geförderten Verbund-Projekt Konti-BIP (kontinuierliche Fertigung von Bipolarplatten) entwickelt ein Konsortium aus insgesamt sieben Partnern unter Leitung des Fraunhofer IWU ein Werkzeug- und Automatisierungskonzept für die großserientaugliche Fertigung hochpräziser metallischer Bipolarplatten.
Die Projektpartner werden die komplette umformtechnische Fertigungskette von der Stahlrolle (Coil) bis zur Qualitätssicherung betrachten. Bipolarplatten bestehen aus einer Anoden- und einer Kathodenplatte, die jeweils nur eine Blechdicke von max. 0,10 mm aufweisen. Beide Halbplatten müssen mediendicht gefügt werden, damit kein Kühlmittel bzw. keine Prozessgase (Wasserstoff und Sauerstoff) austreten können.
Im Projekt basiert die Umformung der Halbplatten auf dem Verfahren Hohlprägen. Umgesetzt wird sie in einem mehrstufigen Schneid- und Umformwerkzeug auf einer Tryout-Presse; ein passendes Automatisierungskonzept sorgt für den schnellen Teiletransport. Durch die Integration eines intelligenten Mess- und Prüfsystems sollen auf Basis einer Onlinemessung alle wesentlichen Qualitätsmerkmale erfasst und mittels geeigneter Algorithmen ausgewertet werden, um so frühzeitig auftretende Fehlerbilder erkennen und bei Bedarf aussondern zu können.
Neben einer Senkung der Produktionskosten nehmen sich die Projektpartner auch eine deutliche Erhöhung der Produktionsgeschwindigkeit auf 60 Bipolarplatten pro Minute vor.
Konsortialführer ist das Fraunhofer IWU, weitere Projektpartner sind Albert Schmutzler Schnitt- und Stanzwerkzeuge, die AUTEZ GmbH, die a.i.m. all in metal GmbH, die KMS Technology Center GmbH, die LSA GmbH und die BERND FLACH Präzisionstechnik GmbH & Co.KG als assoziierter Partner.
Das Projekt Konti-BIP wird im Rahmen des Nationalen Innovationsprogramms Wasserstoff- und Brennstoffzellentechnologie mit insgesamt rund 3,2 Millionen Euro durch das Bundesministerium für Digitales und Verkehr gefördert. Die Förderrichtlinie wird von der NOW GmbH koordiniert und durch den Projektträger Jülich (PtJ) umgesetzt.
Kontakt: