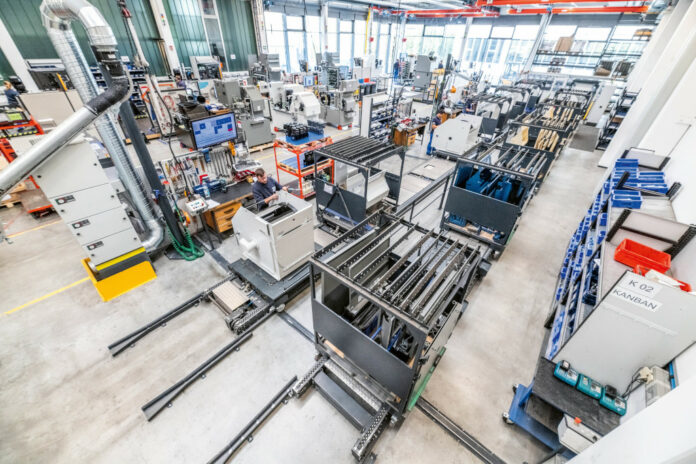
Damit kleine und mittelständische Maschinenbauunternehmen in Deutschland und Europa im globalen Wettbewerb bestehen können, müssen sie permanent nach Optimierungsmöglichkeiten suchen, sie bewerten und gegebenenfalls möglichst schnell umsetzen. Ein Bereich mit großem Potential sind Montage- bzw. Produktionsprozesse sowie die gesamte Intralogistik. Denn dort wird häufig viel Zeit, Platz und Energie verschwendet.
KNOLL Maschinenbau, Bad Saulgau, bekannt als Spezialist fürs Kühlschmierstoff- und Spänemanagement bei zerspanenden Produktionsanlagen, hat das Potential der Automatisierung in diesen Bereichen schon vor über zehn Jahren erkannt. Geschäftsführer Matthias Knoll blickt zurück: „Wir haben damals ein geeignetes Transportsystem gesucht, um eine Fließmontage unserer Kompaktfilter aufzubauen. Da wir am Markt nichts Passendes gefunden haben, entschlossen wir uns, selbst ein solches System zu entwickeln, das auf Kettenförderern basiert.“
2012 installierte KNOLL in Bad Saulgau das erste selbstentwickelte Transportsystem mit Staurollenband zur Montage der Kompaktfilter-Oberteile. Wesentliche Merkmale: eine robuste Stahlkonstruktion, die für hohe Biegesteifigkeit sorgt, sowie der unkomplizierte Umgang mit dem System, der sich unter anderem darin zeigt, dass sich Transportwagen oder andere Vorrichtungen ohne Hilfsmittel ein- und ausschleusen lassen.
Eigene Anwendererfahrung ermöglicht gezielte Beratung
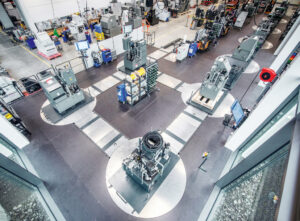
In den vergangenen zehn Jahren ist viel passiert. Die Technik wurde ständig verbessert und neue Komponenten den Kundenbedürfnissen entsprechend entwickelt. KNOLL projektierte, produzierte und installierte zahlreiche Anlagen bei Kunden sowie weitere in der eigenen Produktion in Bad Saulgau. So unterstützt beispielsweise eine weitere Transportanlage die Endmontage der Kleinanlagen – hier auf Basis einer geradlaschigen Kette mit Podest und deutlich mehr technischer Finesse.
„Da wir unsere eigenen Automatisierungsprodukte täglich nutzen, können wir sie praxisorientiert weiterentwickeln und unsere Kunden live detailliert beraten“, erklärt Matthias Knoll. „Diese sind in der Regel ebenfalls mittelständische Anlagen- und Maschinenbauunternehmen, deren Probleme wir sehr genau kennen. Sie müssen automatisieren, um den Mangel an Fachpersonal zu kompensieren. Sie sind an Räumlichkeiten gebunden, die Stück für Stück gewachsen sind und daher speziell angepasste Transport- und Montageanlagen erfordern. Umstände, denen wir mit einer maximalen Modularität entgegenkommen. Zudem können wir unsere Anlagen bei Bedarf jederzeit umbauen und erweitern.“
Vom Transportsystem zur automatisierten Montageanlage
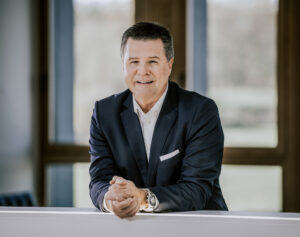
Im Jahr 2019 wurde der Bereich „Transportsysteme“ zu einer eigenen Abteilung, die seit Anfang 2022 den Namen „Automatisierung“ trägt. „Diese Umbenennung war erforderlich, da die Märkte nicht mehr nur nach stationärer Fördertechnik verlangen, sondern nach anspruchsvollen Automatisierungslösungen, möglichst aus einer Hand“, erklärt Matthias Knoll.
„Unser Geschäftsbereich Automatisierung beschäftigt sich schon seit Jahren mit solchen anspruchsvollen Montage- und Logistikaufgaben, für die wir stationäre Transportsysteme auf Basis von Ketten- und Rollenförderern ganz nach Bedarf mit Transportrobotern (FTS) und Handhabungsrobotern (Robots, Cobots) verknüpfen. Wir beraten, projektieren und liefern flexible Gesamtlösungen aus einer Hand, auf Wunsch auch mit entsprechender Netzwerkintegration.“
Christian Spohn ist seit 2021 Abteilungsleiter des KNOLL Geschäftsbereichs Automatisierung. Er verweist auf erfolgreiche, repräsentative Projekte, die KNOLL bei führenden Unternehmen innovativer Branchen umgesetzt hat.
Modularität zahlt sich aus
Dazu zählt zum Beispiel eine Installation bei RIKA Innovative Ofentechnik am Standort Adlwang. Um die wachsenden Auftragszahlen für Pellets- und Kaminöfen zu bewältigen, hat der Hersteller seine dortige Produktion in den Jahren 2019 und 2021 mit Hilfe von KNOLL Maschinenbau teilautomatisiert und digitalisiert. Mit den beiden neuen Montagelinien ist es gelungen, die Produktivität um ca. 15 bis 20 Prozent zu steigern. Außerdem kann RIKA damit seinen Mitarbeiterinnen und Mitarbeitern ein Arbeitsumfeld bieten, das hinsichtlich Ergonomie und Arbeitssicherheit modernsten Gesichtspunkten entspricht.
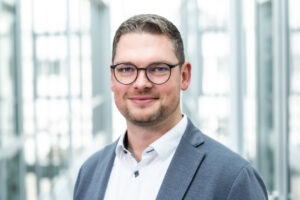
„Eine wesentliche Stärke unserer Anlagen ist ihre Modularität, was bei RIKA in Adlwang besonders deutlich zum Tragen kommt“, betont Christian Spohn. Denn dort stellte sich heraus, dass die beiden Montagelinien mit weniger Stationen auskommen könnten, aber durch die wachsende Auftragslage zwei zusätzliche Linien erforderlich wären.“
Für KNOLL kein Problem. Die Automatisierungsspezialisten entnahmen aus den bestehenden Linien einige Elemente und setzten sie in den beiden neuen ein. „Dank dem modularen Aufbau unserer Systeme war das mechanisch und softwaretechnisch einfach zu lösen“, erklärt Christian Spohn. „Der Kunde profitierte letztendlich von geringeren Kosten und einer schnelleren Inbetriebnahme der Neuanlagen. Dementsprechend ist er sehr zufrieden.“
Hard- und Software aus einer Hand
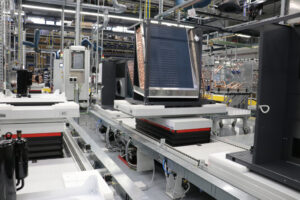
Eine weitere Wachstumsbrache sind Wärmepumpen, wie sie Stiebel Eltron in Holzminden produziert. Hier ging es den Verantwortlichen darum, die Flächenproduktivität in der Montage zu erhöhen. Sie planten daher eine „Multiline“ genannte, hochflexible Produktionsanlage, die stationäre Förderstrecken mit Handarbeitsplätzen und einzelne Arbeits- und Prüfstationen via FTS verbindet.
Eine Kopfsteuerung sorgt dafür, dass die verschiedenen Wärmepumpenmodelle ihren individuellen Weg zu den benötigten Montagestationen finden. Ein wichtiger Partner bei diesem Projekt war KNOLL Maschinenbau. Die Bad Saulgauer lieferten nicht nur die stationäre Fördertechnik, sie kümmerten sich auch um die intelligente Verkettung von Sensoren und Software.
„Hier konnten wir unser breites Angebot und Know-how unter Beweis stellen“, erklärt Christian Spohn. Das betrifft zum einen die gelieferte Hardware in Form der Transportbänder und Handarbeitsplätze, aber auch die Bedienung der Hub- und Drehtische über Steuereinheiten an den Arbeitsplätzen, die einfach und dank Hardwaretaster störungsunanfällig realisiert wurde.
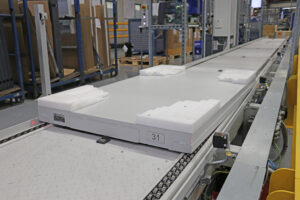
Christian Spohn ergänzt: „Bei der Multiline ist das reibungslose Zusammenwirken von Transportbändern, Montagestationen, FTS und SAP ME mit der integrierten Anlagensteuerung ein zentraler Faktor. Hier konnten wir unter Beweis stellen, dass wir uns SPS-seitig sehr gut auskennen und wichtiges Schnittstellen-Know-how besitzen.“
Auch die Produktionsverantwortlichen bei Stiebel Eltron sind mit dem Ergebnis sehr zufrieden. Sie bestätigen, dass es durch die Implementierung zukunftsgerichteter Systeme und Prozesse gelungen ist, die Produktivität deutlich zu steigern und eine enorme Transparenz zu erreichen. Der Beweis für die Zufriedenheit: ein Folgeauftrag an KNOLL, im Jahr 2023 eine weitere neue Produktionsanlage für Wärmepumpen auszustatten.
Kontakt: