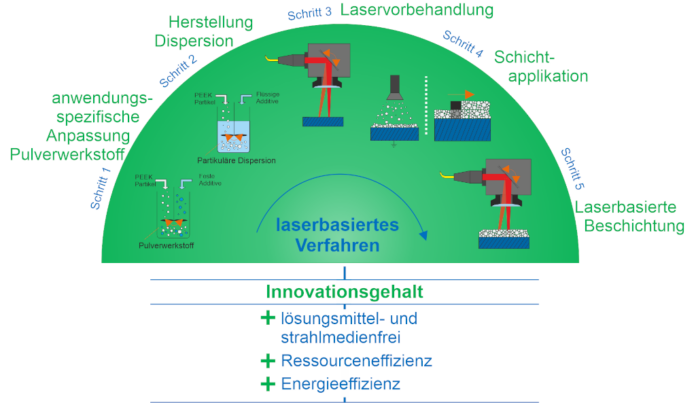
Das industrielles Partnernetzwerk aus Nordrhein-Westfalen hat ein neues effizientes Verfahren für tribologische Beschichtungen entwickelt. Das laserbasierte Beschichtungsverfahren senkt den Energieverbrauch gegenüber konventionellen Ofenprozessen um bis zu 90 Prozent. Es beweist zudem eine nachhaltige Reduktion des Materialverlustes bei der Schichtapplikation sowie den Verzicht auf chemische Reinigungsmittel und Strahlmedien.
Das neue Verfahren resultiert aus der Zusammenarbeit der Unternehmen BECHEM, cleanLASER, Evonik und Fraunhofer ILT im Abschluss des von der Landesregierung Nordrhein-Westfalen und der Europäischen Union geförderten Forschungsprojekts „ENLAPRO“.
Das übergeordnete Ziel des von Evonik konsortial geführten Projekts bestand in der Ausarbeitung eines energieeffizienten, laserbasierten Produktionsverfahrens für PEEK-basierte (Polyetheretherketon) tribologische Beschichtungen. Damit können metallische Komponenten beschichtet werden, die hohen mechanischen Belastungen ausgesetzt sind – etwa Kolben oder Lagerschalen in Verbrennungsmotoren oder Metallbauteile in Klimakompressoren.
Neues Beschichtungsverfahren verbraucht weniger Energie
Der zentrale Innovationsgehalt des neuen Verfahrens besteht in der signifikanten Verbesserung der Energieeffizienz, da lediglich das Beschichtungsmaterial und eine dünne Randschicht des Bauteils mittels Laserstrahlung erwärmt werden. Erste Berechnungen zeigen einen um bis zu 90 Prozent reduzierten Energieverbrauch gegenüber Ofenprozessen – je nach Größe des Bauteils und der Beschichtungsfläche. Mit dem neuen Beschichtungsverfahren kann außerdem der Materialverlust bei der Schichtapplikation nachhaltig reduziert sowie auf chemische Reinigungsmittel und Strahlmedien dank einer Laservorbehandlung verzichtet werden.
Mit der Entwicklung neuer Hochleistungsmaterialen auf Basis von VESTAKEEP PEEK legte Evonik die Grundlage für die Projektarbeit. Daraufhin stellte BECHEM eine wasserbasierte PEEK-Dispersion als eine notwendige Bedingung für den Einsatz von Tauch-, Druck- und Sprühverfahren (exkl. elektrostatischem Sprühen) her.
Mittels des neuen laserbasierten Schmelzverfahrens können haftfeste PEEK-Schichten auf Aluminium und Stahl sowohl mit dem VESTAKEEP PEEK-Pulver von Evonik als auch mit den Dispersionen von BECHEM hergestellt und charakterisiert werden. Dafür setzte das Fraunhofer ILT einen aufgebauten Prozesskopf samt Prozessregelung um und führte umfangreiche Wärmeleitungs-Simulationen zur Generierung von Prozessverständnis parallel durch. Schließlich wurde ein Aluminium- und ein Stahldemonstrator in dem neuen Verfahren mit PEEK in den drei Hauptprozessschritten – Laservorbehandlung, Beschichtung, Laserschmelzen – erfolgreich beschichtet.
Für laserbasierte Beschichtungsverfahren ist eine Vorerwärmung der Bauteiloberfläche notwendig, um haftfeste Schichten zu erzeugen. Im Rahmen des „ENLAPRO“ Projekts ermittelte cleanLASER geeignete Parameter für die Laservorbehandlung von Stahl und Aluminium, um die Haftfestigkeit zwischen PEEK-Schicht und Bauteil zu erhöhen und somit die notwendige Vorwärmtemperatur zu senken. Das Unternehmen entwickelte zudem ein neues miniaturisiertes Optikkonzept. Es ermöglicht nicht nur, das Gewicht um 20 Prozent zu reduzieren, sondern verbessert hauptsächlich die Energieeffizienz der Vorbehandlung.
Mehr Effizienz durch weniger Reibung
Eine Vielzahl von Anwendungen, insbesondere im Maschinen- und Automobilbau, ist durch Reib- und Verschleißbeanspruchungen bei gleichzeitig höchsten Anforderungen bezüglich Temperaturbelastung und Korrosionsbeständigkeit geprägt. Dies erfordert oftmals den Einsatz spezieller Beschichtungen. Hinsichtlich der Materialeigenschaften sind insbesondere Hochleistungspolymere für solche Anwendungsfälle prädestiniert.
Konventionelle Beschichtungsverfahren umfassen typischerweise mehrere Schritte: eine chemische Bauteilreinigung sowie eine Vorbehandlung des Bauteils mittels Strahlmedien, einen Schichtauftrag in Pulverform mit einem Materialverlust von bis zu 70 Prozent und einen anschließenden, energieaufwendigen Ofenprozess. Darin wird das komplette Bauteil auf typischerweise 400 °C erwärmt, um das Beschichtungsmaterial aufzuschmelzen und so eine haftfeste Beschichtung zu erhalten.
Kontakt: