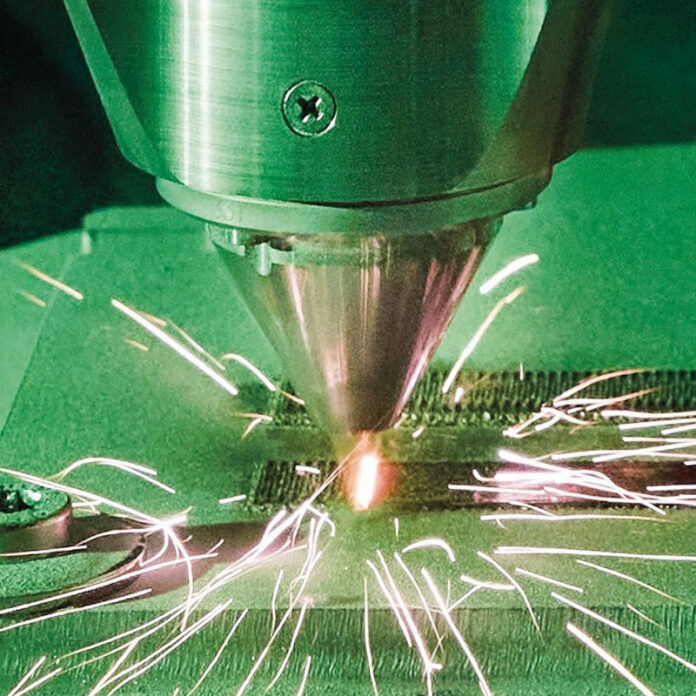
Jahrzehntelang dominierten zwei Laserverfahren beim Drucken und Beschichten von Metallbauteilen. Die dominierende Technologie beim direkten industriellen, metallischen 3D-Druck ist das vor 26 Jahren patentierte laserbasierte Pulverbettverfahren (Laser Powder Bed Fusion LPBF) des Fraunhofer ILT. Die Laserstrahlung schmilzt hier einen kleinen Teil des Basismaterials auf und wandelt das Pulver in eine schmelzmetallurgisch haftende Schicht um. So wächst aus dem Pulverbett Schicht um Schicht ein 3D-Bauteil.
Als effiziente Oberflächentechnik der besonderen Art hat sich außerdem das Laserauftragschweißen (Laser Material Deposition LMD) bewährt. Beim Laserauftragschweißen bildet sich auf der Bauteiloberfläche ein Schmelzbad, in das der Zusatzwerkstoff zum Beispiel per Draht oder Pulver kontinuierlich eingebracht und aufgeschmolzen wird. Damit werden sowohl Substrat als auch Zusatzwerkstoff aufgeschmolzen und es kommt zu einer schmelzmetallurgischen Anbindung zwischen Schicht und Trägerbauteil.
Rettung von teuren Bauteilen
Das wirtschaftliche Potenzial steckt zum einen in der Möglichkeit, Basiskomponenten mit einer Funktionsschicht aufzuwerten oder lokale, additive Bauteilmodifikationen vorzunehmen. Der zweite wichtige Anwendungsbereich des LMD ist das Reparaturschweißen – also das Retten teurer Komponenten bspw. aus dem Bereich Luft- u. Raumfahrttechnik oder Werkzeugbau. Verschlissene oder defekte Komponenten sind nach einer lokalen Reparaturschweißung mittels LMD wieder funktionstüchtig und müssen nicht mehr verschrottet werden.
LMD und LPBF sind mittlerweile aufgrund der verfahrensspezifischen Vorteile unverzichtbar für die metallbasierte additive Fertigung: LMD überzeugt mit einer hohen Produktivität, während LPBF sich für den 3D-Druck von äußerst filigranen und komplexen Bauteilen einsetzen lässt.
Völlig neue Wege gingen das Fraunhofer ILT und der Lehrstuhl für Digital Additive Production DAP der RWTH Aachen University im Jahr 2012 bei der Entwicklung des Extremen Hochgeschwindigkeits-Laserauftragschweißen EHLA. Bei dem patentierten Verfahren schmilzt ein Laser die Pulverpartikel bereits oberhalb des Schmelzbades auf. Auf diese Weise ließ sich die Prozessgeschwindigkeit von bisher 0,5 bis 2,0 (LMD) auf bis zu 200 m/min steigern und die Schichtdicke von 500 auf bis zu 10 µm senken. Pro Stunde lassen sich nun bis zu fünf Quadratmeter beschichten. Zudem wurden die Schichten glatter, die Rauheit wurde auf ein Zehntel des typischen Wertes beim Laserauftragschweißen reduziert.
Internationale Erfolge beim schnellen Beschichten
Die Erfindung kam an: So integrierte Hornet Laser Cladding B.V. aus Lexmond (Niederlande) in seine Drehmaschinen Laserstrahlquelle, EHLA-Bearbeitungskopf und Pulverzufuhrsystem für den industriellen Einsatz des EHLA-Verfahrens. Auch die TRUMPF Laser- und Systemtechnik GmbH aus Ditzingen nahm das Verfahren in das Angebotsportfolio auf und bietet Laseranlagen und -Systemtechniken für den EHLA-Prozess an.
Zu den ersten Anwendern zählen Firmen in den Niederlanden, China, Deutschland und der Türkei. Der Durchbruch gelang 2015 im Offshore-Bereich: Seitdem wurden viele Hundert meterlange Hydraulikzylinder für den weltweiten Einsatz in maritimen Umgebungen mit verschleiß- und korrosionsbeständigen Legierungen beschichtet.
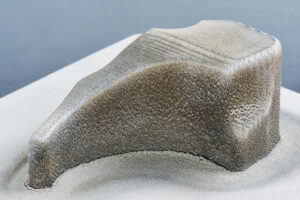
Nach weiteren Erfolgen beim schnellen und prozesssicheren Beschichten von Bremsscheiben, Kolben, Zylindern und Lagern folgte im Jahr 2019 der Schritt in die dritte Dimension: An der Weiterentwicklung beteiligte sich Jonathan Schaible, damaliger wissenschaftlicher Mitarbeiter am Fraunhofer ILT im Rahmen seiner Promotion, in der er sich mit der Frage beschäftigte, welche speziellen Anforderungen für Maschinen- und Systemtechnik zu erfüllen sind, um EHLA mit dem Highspeed-3D-Druck zu kombinieren.
Parallel setzte sein Nachfolger, Min-Uh Ko, die prozesstechnischen Untersuchungen an einer speziell modifizierten 5-Achs CNC-Anlage fort, die höchste Präzision und hohe Vorschubgeschwindigkeiten für die additive Fertigung, Freiformbeschichtung und Bauteilreparatur mittels EHLA vereint.
»EHLA 3D kombiniert die Produktivität von LMD mit ihren 500 bis 2000 µm dicken Schichten mit dem strukturell gezielten, präzisen Aufbau von LPBF mit 30 bis 100 µm dicken Schichten«, erklärt Min-Uh Ko, Gruppenleiter Additive Fertigung und Reparatur LMD am Fraunhofer-Institut für Lasertechnik ILT. »EHLA 3D bewegt sich hier mit 50 bis 300 µm im Mittelfeld.«
Nahe an der Endkontur
Für das Verfahren sprechen außerdem die geringe Aufmischungszone und die hohe Abkühlgeschwindigkeit. Dank dieser Eigenschaften lassen sich auch Bauteile aus schwer schweißbaren Werkstoffen und Multimaterialpaarungen additiv herstellen. Seine Stärken spielt das Verfahren im echten 3D-Druck aus.
Wissenschaftler Ko: »Mit EHLA 3D lassen sich produktiv Bauteile herstellen, die schon sehr nah an die Endkontur kommen. Außer dem sogenannten near-net-shaping ermöglicht das Verfahren auch den schnellen und präzisen Aufbau, sowie Beschichtungen von Freiformoberflächen.«
Anspruchsvolle Formen in Rekordzeit – Das gelingt nur mit entsprechend ausgelegter Maschinentechnik und angepasster Bahnplanung der CNC-Programme. Die Produktivität steht und fällt hier mit dem Zusammenspiel des sogenannten fly-in, bei dem der Laserkopf mit eingeschaltetem Laserstrahl zum Einsatzort fliegt, mit dem anschließenden fly-out, dem abgebremsten Herausfliegen aus der Bearbeitungszone.
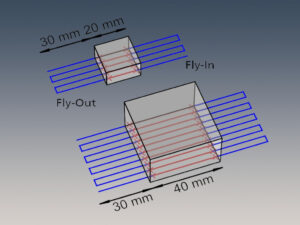
Der Wirkungsgrad ergibt sich aus dem Verhältnis von Bearbeitungszeit mit eingeschaltetem Laserstrahl zur gesamten Prozesszeit. Schaibles Untersuchungen belegen: Bei einer Beschleunigung von 50 m/s² und einem Vorschub von 50 m/min für eine Strecke von 100 mm beträgt der Wirkungsgrad M-PDE (Machine-Related Powder Deposition Efficiency) rund 80 Prozent. Bei einer Beschleunigung von 10 m/s² beträgt der M-PDE ca. 40 Prozent.
Der Aufwand für die Weiterentwicklung des EHLA-Verfahrens hat sich gelohnt, wie ein Blick auf erste erfolgreiche Demonstrationen bewies. Auf dem »AKL’22 – International Laser Technology Congress« in Aachen zeigte Wissenschaftler Ko bei seinem Vortrag im Frühjahr 2022 die aktuellen Fortschritte der EHLA 3D-Technologie.
So wurde in einem Video die produktive, additive Fertigung eines Formbauteils demonstriert, dessen Druckzeit um einen Faktor 2 im Vergleich zum LMD verkürzt werden konnte. Weitere Vorteile ergeben sich darüber hinaus durch die Verringerung des Aufwandes für die Fertigbearbeitung.
Zuverlässiger 3D-Metalldruck mit gebrauchtem Pulver
Hohe Wirkungsgrade zeichnet auch den 3D-Druck von Bauteilen aus dem Aerospace-Werkstoff Inconel 718 aus, die mit einer Auftragrate von mehr als 2 kg/h mit einer Dichte von über 99,5 Prozent entstanden. Die Aachener untersuchten außerdem, wie sich die Kennwerte verändern, wenn sie statt mit neuem mit recyceltem Metallpulver arbeiten. In beiden Fällen betrug die Zugfestigkeit Rm rund 1300 MPa.
Ko: »Die Zugfestigkeit fiel in beiden Fällen genauso gut wie beim Guss aus.« Gute Ergebnisse erzielte auch Wissenschaftler Schaible, der sich unter anderem mit der EHLA 3D-Prozessentwicklung von Bauteilen aus Edelstahl 316L und Aluminium-Silizium-Legierungen befasste. Auch hier entsprechen die erzielten mechanischen Eigenschaften denen, die in der Literatur für konventionell hergestellte Proben angegeben sind. Die aktuell mögliche strukturelle Auflösung von dünnwandigen Aluminiumbauteilen, die mittels EHLA 3D hergestellt werden, beträgt dabei rund 500 µm.
Bei der am Fraunhofer ILT befindlichen CNC-Anlage handelt es sich um einen speziell angepassten Prototyp, der zuverlässig, präzise und gleichzeitig hochdynamische Werkzeugbewegungen ausführen kann.
Die Fraunhofer-Institute auf der LASER World of PHOTONICS in Halle A3, an Stand 441
Kontakt: