Die Elektromobilität ist stark im Kommen. E-Autos fahren mit Strom, der aus erneuerbaren Energiequellen produziert werden kann, und reduzieren somit CO2-Emissionen – ein wichtiger Schritt in Richtung Klimaschutz. Dass der Trend zum Elektrofahrzeug nachhaltig sein würde, haben die Verantwortlichen des mittelständischen Unternehmens Hugo Benzing GmbH & Co. KG in Korntal-Münchingen schnell erkannt. Dem weltweit führenden Sicherungselementehersteller war ebenfalls klar, dass sein Know-how für den Bau von E-Autos nützlich sein würde. So starteten die Sicherheitsexperten die Entwicklung von Berstmembranen und Berstscheiben für die E-Mobilität. Die patentierten Sicherheitsventile geben bei thermischer Überhitzung in der Batterie Druck an die Umgebungsluft ab. Indem sie einen Druckanstieg in der Batterie verhindern, gewährleisten sie die Sicherheit des Elektroautos.
Hohe Sicherheitsanforderungen im Produktionsprozess
Um dieses Entlüftungsventil herzustellen, sind hohe Sicherheitsanforderungen und ständige Qualitätskontrollen im Produktionsprozess nötig. Das Ventil besteht aus drei Teilen, die bei Benzing in einer automatisierten Fertigungszelle zusammengesetzt werden. „Wir haben die Teile zunächst händisch gebaut“, blickt Geschäftsführer Christian Benzing zurück. Doch bald war klar, dass die Nachfrage nach diesen Entlüftungsventilen aus der Automobilindustrie sprunghaft ansteigen würde. „Wir brauchten also hohe Stückzahlen“, sagt Benzing. Die enorme Steigerung der Kapazität konnte nur durch Automation erreicht werden. Zudem konnten die Sicherheitsprüfungen der einzelnen Teile nun standardisiert nach festgelegten, programmierten Prozessen und mithilfe modernster Technik erfolgen. Hier kam das Expertenwissen des Maschinenbauers und Automatisierers, der WAFIOS Tube Automation GmbH aus Simonswald im Schwarzwald, ins Spiel.
Zwei Millionen Sicherheitsventile pro Jahr
„Den Auftrag für die erste Automatisierungszelle erhielten wir im Oktober 2019. Im Jahr darauf ging sie dann in Korntal in Betrieb“, erinnert sich Boris Kühn, Geschäftsführer der WAFIOS Tube Automation, an die Anfänge. Seit 2023 sind nun zwei überwiegend baugleiche Zellen im Einsatz, die pro Jahr insgesamt zwei Millionen Ventile produzieren. In jeder Einheit kooperieren jeweils sechs KUKA-Roboter. Die KR AGILUS setzen das Entlüftungsventil aus drei Einzelteilen – einem Trägerteil, einer Feder und einem Verschlussteil – zusammen. Dabei schwenken die Roboter auch um 360 Grad. Dass sie während der Arbeitsprozesse nicht kollidieren, ist exakt berechnet und nach definierten Abläufen programmiert. Der Schlüssel hierfür sind Übergabestationen, an denen die einzelnen Roboter die Teile ablegen und wieder aufnehmen. So garantiert das aufeinanderfolgende Verrichten von Pick-and-Place-Tätigkeiten störungsfreies Arbeiten in der Zelle.
Dank modularer Bauweise ist die Zelle mobil
Dass der Automatisierer für den Auftrag von Benzing auf KUKA-Roboter zurückgriff, hat zwei Gründe: Zum einen ist WAFIOS Tube Automation seit 2013 Systempartner des Augsburger Roboterspezialisten, zum anderen hatte auch Benzing bereits für andere Automationsprozesse auf KUKA gesetzt und sehr gute Erfahrungen gemacht. In der sieben auf fünf Meter großen Zelle laufen in hoher Taktung viele unterschiedliche Prozesse ab. Dafür brauchte es einen präzisen, schnellen und kompakten Roboter. Die Wahl fiel auf den sehr genauen und auf höchste Arbeitsgeschwindigkeiten ausgelegten KR AGILUS, in sechsfacher Ausfertigung pro Zelle. Neben dem flexiblen Roboter ist auch die gesamte Anlage mobil im Betrieb: Sie ist im Werk nicht an einen festen Ort gebunden, sondern steht auf drei Stahlplatten und kann innerhalb kürzester Zeit komplett umgezogen werden. „Für uns war das ein wichtiges Argument, weil Abläufe in der Produktion durchaus immer wieder angepasst werden müssen. Durch diese mobile Lösung entstehen uns dann keine Produktionsausfälle“, freut sich Christian Benzing.
Roboter schleusen die Einzelteile durch die Zelle
Die Sicherheitsventile werden bei Benzing im Drei-Schicht-System gefertigt. Ein Mitarbeiter initiiert zunächst den automatisierten Produktionsprozess, indem er die Trägerteile über ein Palettiersystem in die Anlage einführt. Dort nimmt der KR AGILUS ein Trägerteil auf und übergibt es an eine Lichtprüfung, die durch eine bildverarbeitende Kamera geschieht. Diese Kameras sind ein wichtiger Teil des Prüfprozesses. Nach dem Trägerteil wird die Feder zugeführt, die vor ihrer Verwendung ebenfalls vermessen wird. Schließlich kommt noch das Verschlussteil dazu und wird ebenfalls überprüft. Ist ein Teil fehlerhaft, sortiert der KR AGILUS es aus – in eine eigens dafür vorgesehene Box.
Der Maschinen-Bediener kann jederzeit eingreifen
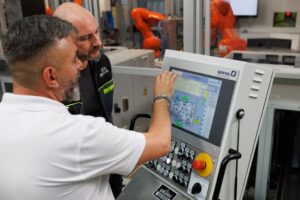
Wenn alle Bauteile geprüft sind, übergeben die Roboter sie in die Montagestation. „Dort werden sie mittels Ultraschall, also durch eine hohe Frequenz, verschweißt“, erklärt Dietmar Dengler, ebenfalls Geschäftsführer bei WAFIOS Tube Automation. Die dabei entstehenden Dämpfe werden zum Schutz der Mitarbeitenden abgesaugt. Ein Roboter übergibt die geschweißten Teile nun an die Entgratstation, die die Überreste vom Schweißen entfernt. Hier ist nochmals eine Prüfstation integriert. Erfüllt das fertige Bauteil die Anforderungen, geht es in eine Dichtheitsprüfung, die in einem Heliumstand vorgenommen wird. „Wenn dann alles passt, wird das Bauteil per Laser beschriftet und ist fertig“, sagt Dengler. Der Bediener kann während des Prozesses auch einzelne Bauteile zur Begutachtung anfordern, wenn er dies für nötig hält. Nach Abschluss aller automatisierten Produktionsschritte entnimmt er die fertig produzierte Menge an Sicherheitsventilen.
Die Greifer erfordern höchste Präzision
Eine Herausforderung waren die Greifer, mit denen die Roboter die sensiblen Einzelteile aufnehmen und wieder ablegen. „Die Federn haben sechs Arme, die sich schon verbiegen, wenn man sie nur zu fest in die Hand nimmt“, erläutert Dengler. Doch bei WAFIOS Tube Automation kennt man sich mit diesen Anforderungen von Greifwerkzeugen aus und hat sie für die Montagezelle daher selbst entwickelt. Auch die übergreifende Steuerung, mit der die Anlage inklusive der sechs KR AGILUS über ein Panel bedient wird, wurde selbst entwickelt und ist bereits seit Jahren bei Kunden im Einsatz. „Der Bediener programmiert lediglich die Steuerung, muss aber keine Roboterkenntnisse haben“, betont Kühn.
Bei der Belegschaft der Hugo Benzing GmbH & Co. KG kommt die Automation gut an. Durch die „Roboter-Kollegen“ haben die Mitarbeiter mehr Ressourcen für andere Tätigkeiten in der Produktion. Zumal eine händische Herstellung der Sicherheitsventile aufgrund der Komplexität der Montage, der vielen Prüfprozesse und des stark gestiegenen Outputs gar nicht sinnvoll wäre.