Das µm-genaue Zerspanen von Keramik ist eine Herausforderung, der sich nur wenige Unternehmen stellen. LouwersHanique erledigt solche Aufträge schon jahrzehntelang. Seit 2023 hat der Präzisionsbearbeiter die hochpräzise Bearbeitung von spröden Werkstoffen nochmals auf ein neues Niveau gehoben. Entscheidend dafür ist der Einsatz des von Kern entwickelten duktilen Schnittmodus in Kombination mit dem Highend-Bearbeitungszentrum Kern Micro HD.
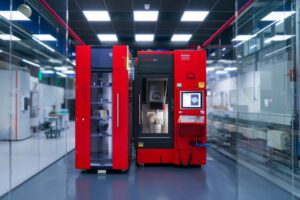
Im Jahr 2012 haben sich die Inhaber der Firmen „Louwers Glastechniek“ und „Pulles & Hanique“ entschlossen, ihr Know-how zu bündeln und gemeinsame Sache als LouwersHanique BV zu machen. Als Spezialisten für die Bearbeitung von technischem Glas, Quarz und technischer Keramik startete die neu gegründete Gesellschaft mit 70 Mitarbeitern. Inzwischen beschäftigt das erfolgreiche Unternehmen rund 185 Fachkräfte und produziert anspruchsvolle Bauteile für Kunden aus verschiedenen Branchen.
LouwersHanique wächst seit der Gründung kontinuierlich. Der leitende Produktionsingenieur Jan van Dingenen ist auch für die Zukunft sehr zuversichtlich: „Wir arbeiten sehr eng mit innovativen Unternehmen zusammen, die in Hightech-Märkten wie etwa der Halbleitertechnik Medizintechnik oder Analytik tätig sind. Dabei ist vor allem unser umfangreiches Wissen um die Bearbeitung besonders anspruchsvoller Materialien gefragt.“
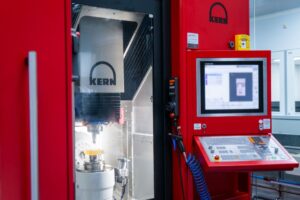
Der Hauptfokus der niederländischen Produktionsspezialisten liegt auf der Herstellung mechatronischer High-End-Baugruppen wie Endeffektoren, Spiegelblöcke, Isolatoren, Sensoren und Keramikgehäuse. „Wir sind stolz darauf, so hochwertige Bauteile herzustellen, die oft sehr wichtig für den Einsatz in Hightech-Systemen sind. Das macht uns zu einem wertvollen Partner für unsere Kunden“, ergänzt van Dingenen.
Keramik hat als Werkstoff einzigartige Vorteile
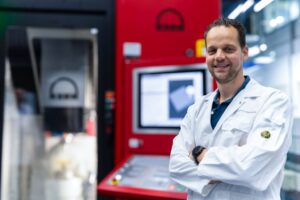
Unterstützung bietet LouwersHanique seinen Kunden von einer frühen Konzept- und Entwicklungsphase bis hin zur Serienfertigung. Entscheidend ist hierbei neben dem umfangreichen Know-how auch eine breite Palette an technischer Ausstattung, die hochautomatisierte und moderne CNC-Bearbeitungstechnologie mit fortschrittlicher Prüf-, Mess- und Reinigungstechnik kombiniert. Nur so sei es möglich, eine hundertprozentig gleichbleibende Qualität zu gewährleisten und dabei neuartige Produkte herzustellen wie etwa hermetisch dichte Durchführungen, 3D-gedruckte Bauteile aus Glas oder mikrobearbeitete Bauteile aus Siliciumcarbid.
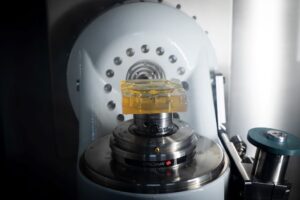
Eine Spezialität von LouwersHanique ist die Bearbeitung von Keramik. „Die Anlagen unserer Kunden werden oft in einer anspruchsvollen Umgebung eingesetzt“, sagt van Dingenen. Dort können die eingesetzten Bauteile und Bauteilgruppen starken Abriebkräften sowie Flüssigkeiten, Gasen oder Vacuum ausgesetzt sein, mitunter in Kombination mit hohen Temperaturen. „Hier haben Keramiken einzigartige Vorteile gegenüber Metallen oder Kunststoffen. Siliziumkarbid hält beispielsweise Temperaturen von mehr als 1200 Grad Celsius stand, ohne die chemische Struktur zu verlieren“, erklärt der Produktionsingenieur. Zudem gasen Keramikwerkstoffe nur minimal aus, sind hochsteif und haben einen niedrigen Wärmeausdehnungskoeffizienten.
Bearbeitung ist extrem anspruchsvoll
All diesen Vorteilen steht primär ein Nachteil gegenüber. Die hochpräzise Bearbeitung von Keramiken und vor allem von Hartkeramiken ist extrem anspruchsvoll. Die Gefahr, dass Risse, Abplatzer und ähnliche Beschädigungen entstehen, ist hoch. „So etwas wird natürlich von keinem Kunden akzeptiert“, erklärt van Dingenen. Gleichzeitig sind die Anforderungen an Genauigkeit und Oberflächengüte in den letzten Jahren enorm gestiegen, führt der Produktionsleiter aus: „Unsere Kunden geben heute teils Toleranzen von bis zu 1 µm und Ebenheiten für Oberflächen von unter 2 µm bei einem Durchmesser von 150 mm vor. Gleichzeitig haben wir bei manchen Keramikteilen eine Rauheit von unter Ra = 0,2 µm einzuhalten.“
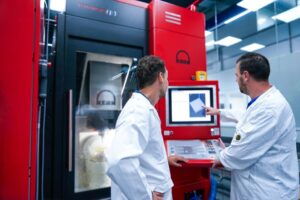
Anforderungen dieser Kategorien brachte die Produktionsexperten von LouwersHanique bis vor kurzem noch gehörig ins Schwitzen. Inzwischen sehen sie diese Anforderungen etwas gelassener. Denn Mitte 2023 wandte sich das Team von Jan van Dingenen an Kern-Vertriebsberater Didier Gony und John Snijders, von der niederländischen Kern-Handelsvertretung Encoma B.V.. „Beide unterstützten uns sofort mit sehr hilfreichen Informationen“, erzählt der Produktionsleiter. „Darüber hinaus realisierten sie bereits kurze Zeit später einen Besuch bei Kern in Eschenlohe.“
Dort hatten die niederländischen Produktionsexperten die Gelegenheit, die Bearbeitung ihrer eigenen Materialien umfangreich zu testen. Laut dem Ingenieur übertrafen die Ergebnisse ihre Erwartungen deutlich: „Als wir sehen konnten, was mit dem von Kern entwickelten und patentierten duktilen Schnittmodus auf der Kern Micro HD möglich ist, wussten wir, dass wir die perfekte Lösung für die Anforderungen unserer Kunden gefunden hatten.“
Perfekte Lösung: Duktiler Schnitt und Kern Micro HD
Als traditionelle Bearbeitungsprozesse für Keramik setzte LouwersHanique früher primär aufs Schleifen und Läppen. Mit dem duktilen Schnitt lassen sich nun selbst härteste Keramiken fräsend bearbeiten. Heißt: Spezielle PKD-Fräswerkzeuge mit geometrisch bestimmter Schneide erlauben es, das extrem spröde Material mit fließendem Span abzutragen. „Wir erreichen damit eine überragende Oberflächenqualität mit minimaler Rauheit, so dass auch an kritischen Stellen keine oder wenig Nacharbeit durch Polieren erforderlich ist. Damit können wir produktiv arbeiten und selbst anspruchsvollste Kunden zufriedenstellen.“
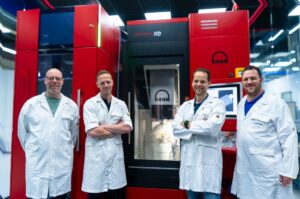
Neben dem von Kern entwickelten duktilen Schnittmodus ist für die hochpräzise Bearbeitung der Keramikbauteile von LouwersHanique eine extrem prozessstabile Maschine wichtig, die die geforderten höchsten Genauigkeiten erzielt. Hohe Steifigkeit und Laufruhe, eine schnell drehende Spindel und Beständigkeit gegen Keramikstaub sind Grundvoraussetzungen. Eigenschaften, die insbesondere die Kern Micro HD mitbringt. Ihre clevere Achsanordnung schützt die Mechanik vor dem abrasiven Staub und die Mikrospalthydrostatik sorgt für höchste Steifigkeit.
Die 15 kW-starke Hochgeschwindigkeitsspindel des Highend-Fünfachsfräszentrums erreicht Drehzahlen bis zu 42.000 min-1, was es ermöglicht, mit dieser Maschine auch Koordinatenschleifen zu realisieren. Bei Bedarf kann also ohne umzuspannen erst mit Schleifstiften geschliffen und anschließend mit PKD-Fräswerkzeugen duktil gefräst werden.
Für den leitenden Produktionsingenieur Jan van Dingenen ist die Entscheidung in Kern zu investieren, die absolut richtige gewesen. Dabei hebt er neben der herausragenden Technologie auch die gute Zusammenarbeit mit allen beteiligten Personen hervor, insbesondere mit Encoma-Inhaber John Snijders: „Er hat uns während des gesamten Kaufprozesses unterstützt und war sogar bei der Inbetriebnahme der Kern Micro HD dabei. Es hat alles wunderbar geklappt, und wir freuen uns, jetzt Teil der Kern-Familie zu sein.“
Kontakt: