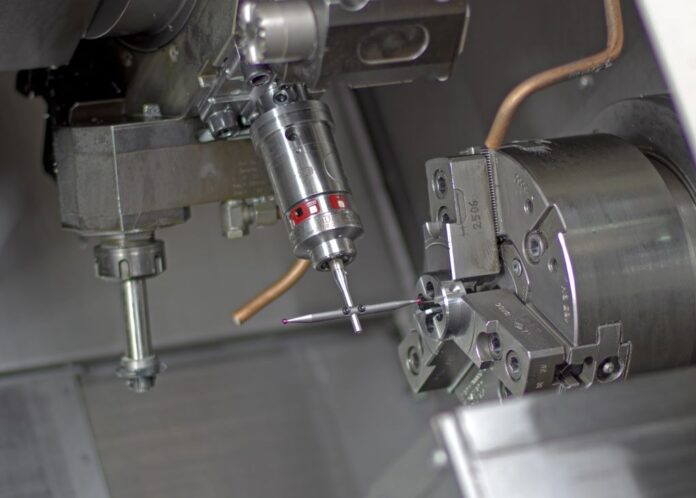
Hersteller von Gewindewerkzeugen sind gerade in Europa rar – die große Konkurrenz aus Billiglohnländern hat das Geschäft für viele unrentabel gemacht. Eine Ausnahme stellt Johannes Boss (JBO) dar, denn das Albstädter Unternehmen zählt durch seine außergewöhnliche Qualität und Präzision sowie Innovation und Kundenorientierung zu den weltweit führenden Anbietern von Präzisionswerkzeugen für die Herstellung und Prüfung von Gewinden. Bei der automatisierten sowie extrem präzisen Fertigung der JBO-Werkzeuge spielen Messtaster von Blum-Novotest eine wichtige Rolle.
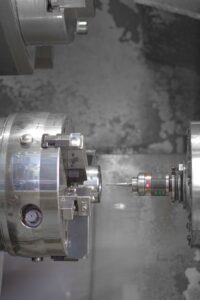
Bereits Ende der Fünfzigerjahre dachte man bei JBO über eine effiziente Fertigung nach und richtete eine Automatisierungsabteilung ein. Bis heute sind die daraus resultierenden Linear– und Dreheinheiten ein fester Bestandteil des Verkaufsprogramms. Selbstverständlich wird in Albstadt weiter an der Optimierung von Präzision und Effizienz in der Fertigung gearbeitet. „Diese beiden Faktoren hängen eng zusammen. Beispielsweise mussten wir früher wegen unseres extrem widerspenstigen Materials nach etwa zehn bis fünfzehn gefertigten Teilen die Bearbeitungsmaschine anhalten, die gefertigten Teile nachmessen und bei Bedarf die Bearbeitungsparameter anpassen“, erinnert sich Prozessingenieur Markus Beisel. „Da ein Bediener mehrere Maschinen beaufsichtigt, standen diese oft erst einmal eine Weile, bevor die Messung personalbedingt möglich war. So kamen wir auf ein durchschnittliches Produktions- und Messintervall von ca. 30 Minuten – das reduziert natürlich die Effizienz der Fertigung enorm.“
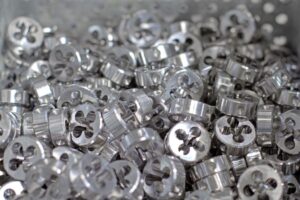
Im Jahr 2018 kam die Idee auf, die Messung in den laufenden Prozess zu verlegen. Es wurden Messtaster angeschafft, die direkt auf dem Werkzeugrevolver der Mehrspindel-Drehautomaten montiert waren. Diese ersten Messtaster zeigten, dass die Idee richtig war, sie konnten aber den sehr rauen Bedingungen im Bearbeitungsraum der Drehmaschinen nicht standhalten:
Die Taster waren aufgrund der starken Vibrationen und Schläge, die bei Drehmaschinen auftreten, sowie aufgrund der physikalischen Belastung durch herumfliegende und hängenbleibende Späne nach nur drei bis fünf Monaten defekt. Denn die Messwerke enthielten einfache Kugelpaare, die aufgrund von Verschleiß mit der Zeit nicht mehr in die Ausgangsstellung zurückgegangen sind.
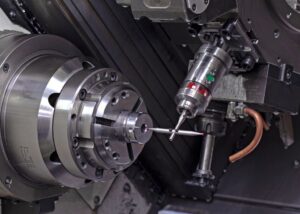
Der BLUM-Vertriebstechniker Erhard Strobel machte die Prozessspezialisten auf den Messtaster TC54-10 T – einer speziellen Version des BLUM-Messtasters für den rauen Einsatz in Drehmaschinen – aufmerksam. „Das patentierte, planverzahnte shark360-Messwerk bietet höchste Messgenauigkeit auch bei außermittiger Antastung sowie ziehende und – wichtig bei JBO – torsionsbeaufschlagte Messungen. Zusätzlich werden bei JBO ein Schwingungsdämpfer zwischen Werkzeugrevolver und Messtaster sowie schwingungsgedämpfte Batteriefächer eingesetzt“, berichtet Erhard Strobel.
„So widersteht der Messtaster den Umweltbedingungen nun schon seit vier Jahren. Die auf vier Drehmaschinen eingesetzten Messtaster sind mit einem kreuzförmigen Tasteinsatz ausgestattet, der das Messen von Werkstücken auf Haupt- und Gegenspindel erlaubt.“
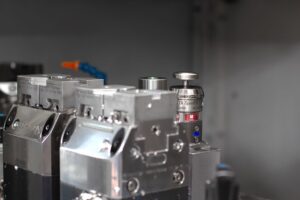
Diverse Messungen werden direkt nach der Bearbeitung durchgeführt: Neben bestimmten Maßen, die je nach Werkstück unterschiedlich sind, erfolgt die Kontrolle der Zentrierbohrungen, die bei späteren Prozessschritten benötigt werden. Der Zentrierbohrer bricht gerne mal, da ist es wichtig, zu überprüfen, ob die Bohrung korrekt gefertigt wurde. Je nach Werkstück wird jedes Teil oder auch jedes dritte oder vierte gemessen. Auf jeden Fall sind die Messungen im Prozess viel zeitsparender als die frühere externe Messung.
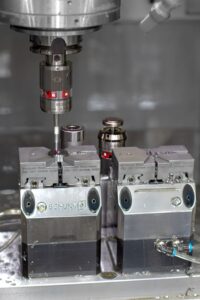
Da die meisten Werkstücke aus hochlegiertem Werkzeugstahl bestehen, ist der Verschleiß der Werkzeuge groß und muss während der Bearbeitung kompensiert werden. Beziehungsweise die Bearbeitung stoppt, wenn anhand der Werkstückmessung erkannt wird, dass das Werkzeug zu stark verschlissen ist. Dennoch ist JBO dank der Messung im Bearbeitungsraum erstmals in der Lage, eine mannlose Geisterschicht in der Dreherei zu fahren. „Die BLUM-Messtaster auf den Maschinen messen direkt nach der Bearbeitung und arbeiten so lange, bis kein Rohmaterial mehr da ist, Späne hängenbleiben, die Fehlmessungen verursachen oder manuell ein verschlissenes Werkzeug gewechselt werden muss“, beschreibt Thomas Fritsch, Teambetreuer und Koordinator Dreherei. „Das können drei bis vier Stunden sein, wir hatten aber auch schon Werkstücke, bei denen die Fertigung die ganze Nacht und den halben Vormittag lang mannlos gelaufen ist. So steigern wir den Output massiv!“
Dank der BLUM-Messtaster produziert Johs. Boss fast ausschließlich Gutteile, da teilweise im mannlosen Betrieb jedes Teil gemessen wird. Früher wurde zum Teil erst jedes 10. Stück gemessen, da konnten im Worst Case neun Werkstücke Ausschuss produziert werden, bis das Problem bei der nächsten Messung auffiel und die Bearbeitung abgebrochen wurde. Heute steht die Maschine, sobald ein Messwert nicht stimmt.
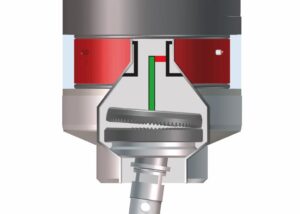
„Wir arbeiten mit den Messprogrammen, die BLUM mit seinen Tastern liefert, und passen diese an unsere Anforderungen an“, erklärt Thomas Fritsch, der für die Programmierung der NC-Programme zuständig ist. „Wir haben kleine Losgrößen mit 50 bis 2.000 Teilen, aber immer wieder ähnliche Geometrien. Deshalb können wir ein Standard-Messprogramm auf Basis der BLUM-Programme nutzen, das wir über Makros auf die jeweilige Variante anpassen.“ Kühlschmiermittel und Verschmutzung stören die Messung praktisch nie: Die Maschinen werden jeden Freitag geputzt und dabei Taster und Infrarot-Empfänger abgewischt. Mit der Datenübertragung per Infrarot gab es noch nie Probleme.
Nicht nur beim Drehen, sondern auch auf den Fräszentren optimieren die BLUM-Messtaster die Prozesse, hier sind es Taster des Typs TC52. Diese Systeme werden in den Fräsmaschinen einerseits zur Werkstücknullpunkterfassung, anderseits auch zur Temperaturkompensation eingesetzt, um die Veränderungen der Maschinen durch deren Erwärmung bei der Bearbeitung auszugleichen. Schließlich verändern sich die Achsen um bis zu fünf hundertstel Millimeter, wenn die Maschinen zehn Minuten stehen. Da ist ein Einmessen mit dem TC52 an einem Referenzwerkzeug hinter dem Spannbereich sinnvoll, wenn man gleichbleibende Qualität haben möchte. Neben dem Referenzwerkzeug sitzt übrigens ein Werkzeugmesstaster ZX-Speed IR, der ebenfalls von BLUM kommt und für die Werkzeuglängen- und Radiusmessung genutzt wird.
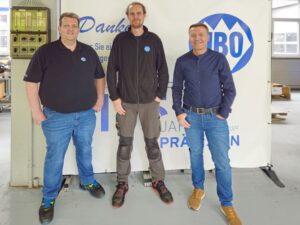
Mit den Messtastern und den Messungen im Prozess konnte JBO mehr Konstanz in diesen Prozess bekommen. Nach dem Fräsen werden die Teile gehärtet und schließlich weiterbearbeitet, während es früher bei diesem Schritt öfter Probleme gab, wenn die Teile größere Schwankungen in den Messergebnissen hatten. Das ist mittlerweile vorbei, die Teile bleiben zuverlässig innerhalb der Toleranz. Und ganz wichtig: Alle Teile sind innerhalb der Toleranz sehr eng beieinander. Auch deswegen ist man in Albstadt mit den BLUM-Tastern sehr zufrieden, zumal sie auch bereits seit mehreren Jahren absolut zuverlässig arbeiten.
„Dank BLUM produzieren wir in besserer Qualität und mit weniger Ausschuss als früher. Mehr kann man nicht verlangen“, fasst Markus Beisel zusammen. „Unser ‚schlimmstes‘ Problem ist, wenn der Maschinenbediener beim Putzen nicht aufpasst und den Tasteinsatz verdreht. Mit dieser hohen Zuverlässigkeit spart uns das Messen im Prozess mit den BLUM-Messtastern jeden Tag viel Zeit und ermöglicht Geisterschichten, die früher nicht möglich gewesen wären.“
Kontakt: