Die Großserienfertigung von Bipolarplatten für Brennstoffzellen erfolgt im Sekundentakt. Um eingesetzte Umformwerkzeuge vor Verschleiß zu schützen, werden sie aus hochwertigen Metalllegierungen gefräst. Im Nationalen Aktionsplan Brennstoffzellen-Produktion (H2GO) geht das Fraunhofer-Institut für Lasertechnik ILT in Aachen neue Wege: Statt die Werkzeuge aus dem Vollen zu fräsen, bringt es mithilfe des Extremen Hochgeschwindigkeits-Laserauftragschweißens (EHLA) verschleißfeste Funktionsschichten endkonturnah auf günstigen Baustahl auf. Die Kosten, Bauzeit und der Verschleiß der Werkzeuge sinken signifikant. Außerdem ist der EHLA-Prozess zur Reparatur beschädigter und verschlissener Werkzeuge nutzbar – und leistet damit einen wesentlichen Beitrag für die Circular Economy.
»Wir verfolgen einen ganz neuen Ansatz«, berichtet Dora Maischner, Projektleiterin am Fraunhofer ILT. »Bisher wurden Umformwerkzeuge für Bipolarplatten in stundenlangen Prozessen aus hochwertigem Werkzeugstahl gefräst. Wir bringen eine verschleißfeste Funktionsschicht endkonturnah auf kostengünstigen Werkstoff auf.« Die Forscherin bearbeitet ein Teilprojekt von R2HP (Ready to Hydrogen Production). Es ist Bestandteil des groß angelegten Forschungsvorhaben H2GO – Nationaler Aktionsplan Brennstoffzellen-Produktion, an dem bundesweit 18 Institute der Fraunhofer-Gesellschaft beteiligt sind. Das Fraunhofer ILT entwickelt darin gemeinsam mit dem benachbarten Fraunhofer-Institut für Produktionstechnologie IPT und dem Fraunhofer-Institut für Werkzeugmaschinen und Umformtechnik IWU aus Chemnitz das neue Verfahren zur Fertigung von Bipolar-Halbplatten. Das Ziel ist es, die Standzeiten der hoch beanspruchten und präzise strukturierten Umformwerkzeuge zu erhöhen, dabei zugleich ihre Kosten und Bauzeiten zu senken – und obendrein ein effizientes Reparaturverfahren für beschädigte oder verschlissene Werkzeuge zu etablieren. Der Schlüssel dazu ist das am Fraunhofer ILT entwickelte Extreme Hochgeschwindigkeits-Laserauftragschweißen (EHLA).
Revolutionärer Ansatz für die Werkzeugproduktion
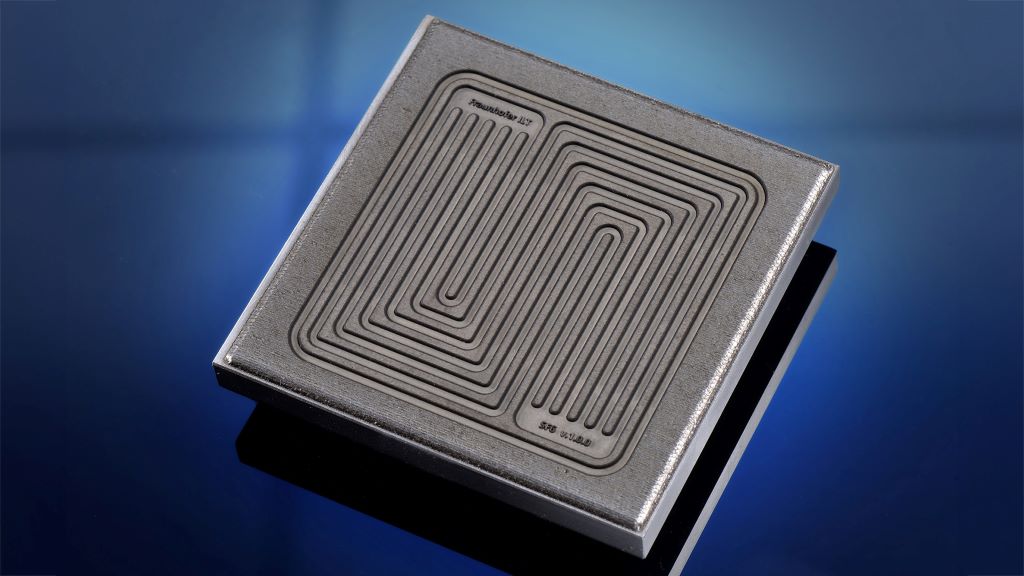
Moderne ELHA-3D-Anlagen erreichen Geschwindigkeiten von mehr als 30 Metern pro Minute. Auf Basis digitaler Prozessketten lassen sich die verschleißfesten Funktionsschichten mit dem additiven Verfahren schnell und effizient aufbringen. Außerdem lässt sich der dreidimensionale Materialaufbau so exakt steuern, dass die auf kostengünstigen Baustahl aufgeschweißte höchst verschleißfeste Schicht der beabsichtigen Endkontur schon sehr nahekommt. Statt diese wie bisher in einem stundenlangen, werkzeugintensiven Prozess aus dem Vollen zu fräsen, muss das Umformwerkzeug also nur noch gezielt endbearbeitet werden. Die neue EHLA-basierte Prozesskette minimiert also zugleich die Kosten, weil nur noch eine dünne Funktionsschicht aus hochwertigem Material aufgebracht werden muss. Zugleich senken der endkonturnahe Materialauftrag und der dadurch minimierte Aufwand der mechanischen Bearbeitung die Bauzeit und die Werkzeugkosten für die vom hochfesten Material stark beanspruchten Fräsköpfe.
Das Besondere am EHLA-Verfahren ist, dass das Pulver bereits oberhalb des Werkstücks im Laserstrahl schmilzt – sich also bereits flüssig auf dessen Oberfläche ablagert. »Im EHLA-Prozess absorbiert nicht das Bauteil, sondern das Pulver einen Großteil der Laserenergie, ehe es auf das Werkstück trifft«, erläutert Viktor Glushych, Gruppenleiter Beschichtung LMD und Wärmebehandlung am Fraunhofer ILT. Das patentierte Verfahren beschleunige den Auftragsprozess gegenüber herkömmlichen Laserauftragschweiß-Prozessen erheblich, minimiere die thermische Belastung der Bauteile und schaffe obendrein homogenere Gefügestrukturen in den Metallschichten. Das wiederum wirkt sich positiv auf die Verschleißfestigkeit aus.
Verschleißbeständigkeit erhöht
Als Beschichtungsmaterialien dienen in dem laufenden Forschungsprojekt der Schnellarbeitsstahl 1.3343 und die martensitische Edelstahllegierung Ferro55, die sich durch hohe Härte und Verschleißfestigkeit auszeichnen. Maischner: »1.3343 erreicht eine Härte von etwa 830 HV0,5 und Ferro55 etwa 820 HV0,5. Damit liegen sie im Bereich des üblichen Werkzeugstahls 1.2379, der sowohl gehärtet als ungehärtet zum Einsatz kommt.« Der Verschleißschutz lässt sich mit der Beschichtungsgeschwindigkeit von 30 Metern pro Minute auftragen. Pro Lage wird eine Schichtdicke von ca. 1,2 Millimetern erzielt. Durch mehrlagigen Auftrag kann die geforderte Schichtdicke, bei der vorliegenden Aufgabenstelle eine Schichtdicke von einem Millimeter, eingestellt werden. Die digitale Steuerung gewährleistet einen präzisen und selektiven Materialaufbau, der es erlaubt robuste Verschleißschutzschichten herzustellen. Deren Struktur ist nach Erkenntnissen des Teams für den Verschleißschutz wichtiger als die Härte des Werkstoffs. »Denn die Verschleißbeständigkeit hängt in sehr hohem Maß vom Gefügezustand des Materials ab«, sagt Glushych. »EHLA erzeugt extrem feinkörnige Mikrostrukturen, dank derer sich die mechanischen Eigenschaften verbessern und so den Abrieb deutlich verringern. Die feinkörnige Struktur verleiht den Schichten eine hohe Beständigkeit gegen Abnutzung, selbst bei starker Belastung.«
Die Stunde der Wahrheit schlägt beim Gleitreibverschleißtest

Um die Verschleißbeständigkeit präzise zu bewerten, setzt das Fraunhofer ILT einen Gleitreibverschleißtest der TU Clausthal ein, der realistische Abnutzungsszenarien für den Anwendungsfall simuliert. Die Anlage drückt unter definierter Kraft einen Pin auf ein Gegenblech und bewegt ihn darauf hin und her. Anschließend lässt sich sehr exakt messen, wie viel Material abgetragen wird. Die bisherigen Ergebnisse deuten auf signifikante Vorteile der per EHLA beschichteten Testkörper gegenüber herkömmlichen Werkstoffen hin.
Um die neue EHLA-basierte Prozesskette praxisnah zu demonstrieren, hat das Team einen Demonstrator aufgebaut, auf dem es einfachen Baustahl (St37) im EHLA-Prozess mit dem Schnellarbeitsstahl 1.3343 endkonturnah beschichtet hat. Für die Endbearbeitung werden am Fraunhofer ILT sowohl das konventionelle Fräsen als auch das Strukturieren mit Ultrakurzpulslasern eingesetzt. Aufgrund des hohen Werkzeugverschleißes bei der mechanischen Endbearbeitung von Werkstoffen hoher Härte, ist das berührungslose Laserverfahren von hohem industriellem Interesse. »Es geht uns im Projekt um den Nachweis, dass die gesamte Prozesskette von der Beschichtung bis zur Strukturierung der Biopolarplatten bereits mit seriennahen Verfahren hinterlegt ist«, erklärt Maischner. Die Forschenden wollen bereits bis Ende dieses Jahres auf einem Versuchsstand des Fraunhofer IPT die Belastbarkeit und Verschleißfestigkeit unterschiedlicher Umformwerkzeuge testen. Dabei nehmen sie seriennahe Umformprozesse in den Fokus, bei denen es gilt, eine Bipolarplatte pro Sekunde zu stempeln – wie es eine effiziente industrielle Produktion erfordert. »Die Methode erlaubt es uns, die Standzeit von EHLA-beschichteten Werkzeugen realistisch zu testen«, erklärt Maischner.
Re-Use: Werkzeuge mit mehreren Leben
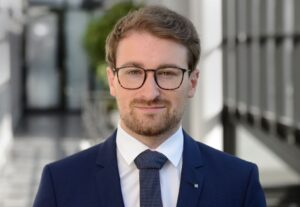
Ein weiterer Fokus liegt auf der effizienten Fertigung und Wiederverwendung der Werkzeuge. »Wir sind bereits im Austausch mit Unternehmen, die Werkzeuge für Bipolarplatten fertigen und erhielten sehr positive Resonanz«, erklärt Glushych. Gerade die Möglichkeit, Funktionsschichten endkonturnah mit den EHLA-typischen Prozessgeschwindigkeiten aufzubauen, und dadurch die bisherige zeitaufwendigen Zerspanung mit hohen Abtragvolumen entscheidend zu verkürzen, wecke Interesse.
Daneben stoße die Option zur Aufbereitung verschlissener Werkzeuge mit demselben EHLA-Prozess auf positives Feedback. Denn statt Werkzeuge nach Ablauf ihrer Lebensdauer einschmelzen zu müssen, lassen sich die defekten oder verschlissenen Konturen per EHLA, gemäß des digital gespeicherten Bauplans, erneut aufbauen und mechanisch endbearbeiten.
Damit kann die neue Prozesskette den Weg zum wiederholten Re-Use ebnen; solche Kreislaufprozesse sind gefragt, weil sie einem Downgrading hochwertiger Legierungen vorbeugen und obendrein auch das energieintensive Einschmelzen abgenutzter Werkzeuge und zahlreiche Transportwege entfallen. Sobald das Werkzeug verschleißt, können Anwender die Schicht vor Ort auf eine definierte, digital gespeicherte Kontur zurückfräsen und erneut per EHLA beschichten. »Dieses Vorgehen schont Ressourcen und erlaubt eine langfristige Nutzung der Werkzeuge«, betonen der Fraunhofer-Forscher.
EHLA-Beschichtung senkt Feinstaubbelastung
Erfolge im Pkw-Bereich machen vielleicht weiteren potenziellen Anwendern Mut, in diese neue Form des Werkzeugbaus einzusteigen. EHLA hat sich hier als effektives Verfahren zur Verschleißschutzbeschichtung bewährt: Bei Bremsscheiben konnten die dünnen fest haftende EHLA-Schutzschichten den Abrieb deutlich minimieren. Der Vorteil kommt nicht nur den Autohaltern zugute, sondern trägt auch zur deutlichen Reduktion von Feinstaub bei. Dieses Know-how bildet die ideale Grundlage, um die Massenproduktion hauchdünner Bipolarplatten für Nutzfahrzeuge voranzutreiben.
H2GO – Nationaler Aktionsplan Brennstoffzellen-Produktion
Das H2GO-Projekt startete im Mai 2022 und läuft bis zum November 2025. Das vom Bundesministerium für Digitales und Verkehr (BMDV) mit 80 Millionen Euro geförderte Verbundprojekt koordiniert das Fraunhofer-Institut für Werkzeugmaschinen und Umformtechnik IWU aus Chemnitz. 18 Fraunhofer-Institute entwickeln kostengünstige Produktionsmethoden für Brennstoffzellen, um den Schwerlastverkehr auf emissionsfreie Antriebe umzustellen. »Mit unserer Förderung wollen wir helfen, aus Forschung marktfähige Produkte zu generieren – und das im industriellen Maßstab«, erklärte Verkehrsminister Dr. Volker Wissing beim Projektstart.
EHLA-Verfahren – Eine Innovation des Fraunhofer ILT
Das Fraunhofer-Institut für Lasertechnik ILT entwickelt seit 2012 das patentierte Extreme Hochgeschwindigkeits-Laserauftragschweißen (EHLA) für immer neue Anwendungsfälle weiter. Damit lassen sich Oberflächen effizient und umweltfreundlich vor Verschleiß und Korrosion schützen. Beim EHLA-Verfahren wird das Pulver direkt im Laserstrahl vor dem Auftreffen auf das Bauteil geschmolzen. Dadurch absorbiert das Pulver den Großteil der Laserenergie, was die thermische Belastung des Grundmaterials erheblich reduziert. Die Beschichtungsgeschwindigkeiten erreichen mehrere Hundert Meter pro Minute und es werden Schichten mit einer Dicke von 30 bis 400 Mikrometer hergestellt.
Für das Verfahren spricht auch das wirtschaftliche Beschichten, denn bis zu 90 Prozent und mehr des eingesetzten Materials gelangen tatsächlich auf das Bauteil. Anwendungen finden sich in der Automobil- und Luftfahrtindustrie sowie in Offshore-Anlagen, wo eine hohe Verschleiß- und Korrosionsbeständigkeit gefragt ist.
Vielseitiger wurde das Verfahren durch die Erweiterung zu EHLA3D: Das Fraunhofer ILT transferierte das Verfahren in Zusammenarbeit mit den Maschinenherstellern Ponticon und Makino auf Hochgeschwindigkeits-Kinematiken. EHLA3D ermöglicht nun nicht nur das schnelle Beschichten, sondern auch die präzise additive Fertigung komplexer, dreidimensionaler Geometrien mit verschiedenen hochfesten Materialien wie Werkzeugstählen, Titan und Aluminium.
EHLA wurde mehrfach ausgezeichnet, darunter 2017 mit dem Joseph von Fraunhofer-Preis und 2018 mit dem zweiten Platz beim Stahl-Innovationspreis in der Kategorie »Stahl in Forschung und Entwicklung«, sowie dem ersten Berthold Leibinger Innovationspreis.
Kontakt: