Die große Werkstück- und Materialvielfalt war bei der Investition in neue Gleitschlifftechnik einer der wesentlichen Punkte im Pflichtenheft der Eingliederungsstätte Baselland ESB. Außerdem sollte die Bearbeitung für die Mitarbeitenden einfacher und zeitgemäßer sowie insgesamt umweltgerechter werden. Diese Anforderungen setzte Rösler mit einer hochautomatisierten Gleitschlifflösung um. Sie besteht aus zwei Rundvibratoren mit automatischer Separierung und Teiletransport zum neuen energiesparenden Trockner sowie einer halbautomatischen Zentrifuge für die ressourcenschonende Kreislaufführung des Prozesswassers.
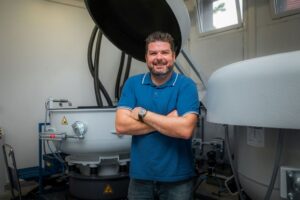
Die 1975 gegründete Eingliederungsstätte Baselland ESB mit Hauptsitz im schweizerischen Liestal ist eine private Stiftung im öffentlichen Auftrag. Die Aktivitäten des sozialen Unternehmens zielen darauf ab, Menschen mit Unterstützungsbedarf darin zu stärken, ein selbstbestimmtes Leben zu führen. Dafür stehen an 19 Standorten rund 100 Wohnmöglichkeiten sowie 480 Ausbildungs- und Arbeitsplätze in den Bereichen Montage und Verpackung, Mechanik, Metallbau, Elektronikfertigung und Betriebsunterhalte mit professioneller Betreuung, Begleitung und Beratung zur Verfügung.
Mechanische Bearbeitung und Gleitschleifen als Dienstleistung
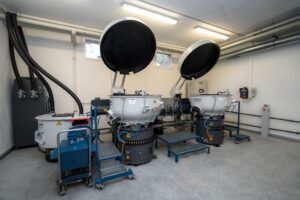
Dazu zählt der Betrieb in Liestal, in dem unter anderem die Bearbeitungsschritte Drehen, Fräsen, Bohren, Gewindeschneiden, Schleifen, Sägen und Reiben als Dienstleistung angeboten werden. Der moderne Maschinenpark ermöglicht dabei, dass Stahl, Aluminium, Buntmetalle und Edelstahl ebenso wie Kunststoffe verarbeitet werden können. Sowohl für die intern gefertigten Teile als auch für extern hergestellte Werkstücke umfasst das Leistungsportfolio darüber hinaus das Entgraten und Kanten entschärfen mittels Gleitschleifen.
Einfacher, komfortabler und umweltgerechter gleitschleifen
„Unsere Anlagen dafür waren jedoch in die Jahre gekommen und haben heutige Anforderungen an Arbeitskomfort, Ergonomie und Nachhaltigkeit nicht mehr erfüllt. So mussten beispielsweise die Teile manuell aus den Arbeitsbehältern entnommen werden. Außerdem wurden die Prozesse mit Frischwasser durchgeführt, was einen hohen Wasser- und Ressourcenverbrauch verursachte“, berichtet Sascha Berger, Co-Leiter des Betriebs in Liestal der ESB. Neben der Möglichkeit, das enorm breite Spektrum an Bauteilen, Geometrien und Materialien problemlos bearbeiten zu können, waren die Automatisierung des Prozesses sowie eine möglichst einfache Steuerung und Handhabung wesentliche Punkte im Pflichtenheft bei der Investition in neue Anlagen.
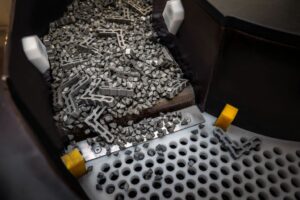
«Für uns war es essentiell, unsere Mitarbeitenden zu entlasten und sie in Neuem zu fördern», vertieft Sascha Berger. Eine weitere wichtige Vorgabe war die Kreislaufführung des Prozesswassers. Darüber hinaus musste die Einbringsituation berücksichtigt werden, da die Gleitschliffprozesse in einem Raum mit einer nur 1,20 m breiten Tür im Untergeschoss durchgeführt werden. Mit diesen Anforderungen wandte sich Sascha Berger an fünf Hersteller von Gleitschlifftechnik, darunter die schweizerische Tochtergesellschaft der Rösler Oberflächentechnik GmbH in Kirchleerau.
Optimal auf die Bedürfnisse und Wünsche abgestimmte Gleitschlifflösung
Nach intensiven Gesprächen über das Projekt hat sich ESB für die Lösung der Rösler Schweiz AG entschieden. Sie besteht aus zwei Rundvibratoren R 220 Euro mit automatischer Separierung, deren Siebe einfach und werkzeuglos getauscht und so für verschiedene Teile eingesetzt werden können. Die Vibratoren sind durch ein Transportband mit dem Trockner RT 150 Euro DH verbunden. Er verfügt über ein Wärmeblock-Heizsystem, das mit der Bodenplatte des Arbeitsbehälters direkt gekoppelt ist und dadurch im Vergleich zu klassischen Trocknern Energieeinsparungen von bis zu 40 % ermöglicht. Für die Kreislaufführung des Prozesswassers ist eine halbautomatische Zentrifuge Z 800 K-HA-TF in die Lösung integriert, deren Ausstattung auf die Materialvielfalt ausgelegt wurde. „Ausschlaggebend bei der Entscheidung war, dass Rösler sehr detailliert auf unser Pflichtenheft eingegangen ist und uns ausführlich zu unseren speziellen Anforderungen beraten hat. So informierte uns der Rösler-Mitarbeiter genau darüber, was bei der Aufbereitung des durch verschiedene Metalle verunreinigten Prozesswassers zu beachten ist“, erklärt Sascha Berger. Für die verschiedenen zu bearbeitenden Bauteile wurden im Customer Experience Center in Kirchleerau Versuche durchgeführt und anhand derer die jeweiligen Bearbeitungsparameter wie Einsatz der geeigneten Schleifkörper, Compound, Bearbeitungsintensität und -zeit definiert. Die dabei ermittelten Daten wurden als teilespezifische Programme in der Anlagensteuerung hinterlegt. „Während der Zusammenarbeit und der Versuche hat uns Rösler viel Know-how zum Gleitschleifen vermittelt. Dadurch wissen wir heute, was wir machen und was es braucht, damit wir Ziele beim Gleitschleifen optimal erreichen“, ergänzt Sascha Berger.
Vollautomatische Bearbeitung inklusive Teileseparierung und -Trocknung
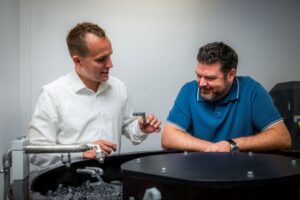
Im ersten Schritt wählt der Mitarbeitende das teilespezifische Bearbeitungsprogramm am Schaltschrank aus. Die Bedienung der Vibratoren erfolgt jeweils über eine Bediensäule mit drei Knöpfen für Start, die Freigabe der Separierung und einen außerplanmäßigen Stopp. Mit dem Druck auf den Startknopf beginnt der Arbeitsbehälter im sogenannten Belademodus leicht zu vibrieren und wird befüllt. Nach einer festgelegten Zeit wechselt der Vibrator in den Bearbeitungsmodus und der Schallschutzdeckel wird durch eine Zweihandsteuerung an der Bediensäule geschlossen. Am Ende der Bearbeitungszeit fragt die Anlage ab, ob direkt separiert werden kann. Ist das der Fall, wird die Separierklappe pneumatisch aktiviert.
Die Schleifkörper fallen durch das großflächige Separiersieb zurück in den Arbeitsbehälter und die Teile gelangen über das Transportband zum Trockner, in dem ein Naturprodukt als Trocknungsmedium eingesetzt wird. Es trocknet die Teile im Einmaldurchlauf, danach werden sie automatisch in ein vor dem Trockner platziertes Behältnis ausgegeben. Um eine Teilevermischung zuverlässig zu vermeiden, kann ein erneuter Separiervorgang für den Rundvibrator erst freigegeben werden, wenn das Behältnis entfernt wurde. Solange die Freigabe nicht vorliegt, vibriert der Arbeitsbehälter mit reduzierter Intensität weiter. Die Werkstücke bleiben in Bewegung, was insbesondere bei Stahlteilen ein Korrodieren verhindert.
Über 50 % höhere Produktivität und Wirtschaftlichkeit
Im Vergleich zu den bisherigen Anlagen ermöglicht die neue Gleitschlifflösung deutlich kürzere Prozesszeiten und einen mindestens 50 % höheren Durchsatz. Gleichzeitig konnte der Verbrauch an Frischwasser und Compound durch die Kreislaufführung des Prozesswassers spürbar reduziert werden. All dies trägt dazu bei, dass das Gleitschleifen wirtschaftlicher geworden ist. „Grundsätzlich steht bei uns der Mensch an erster Stelle und unseren Mitarbeitenden macht die Arbeit mit der neuen Anlage viel mehr Freude. Aber natürlich ist die Wirtschaftlichkeit auch ein Aspekt, auf den wir achten, und auch da haben wir einiges erreicht“, merkt Sascha Berger abschließend an.
Kontakt: