Haldex, ein führender Anbieter von Bremssystemen für Lkws und Lkw-Anhänger, hat seine Produktivität deutlich gesteigert. Bevor mit LiCON eine bessere Lösung gefunden wurde, bestand das Standardbearbeitungskonzept aus robusten Einspindelmaschinen mit vier Achsen. Die Turm-Spannvorrichtungen erforderten lange Werkzeuge, die bei der Bearbeitung des GJS 600-Materials zum Rattern neigen. Mit dem doppelspindligen LiCON-Bearbeitungszentrum in 5-Achs-Ausführung werden diese Herausforderungen nun perfekt gemeistert.
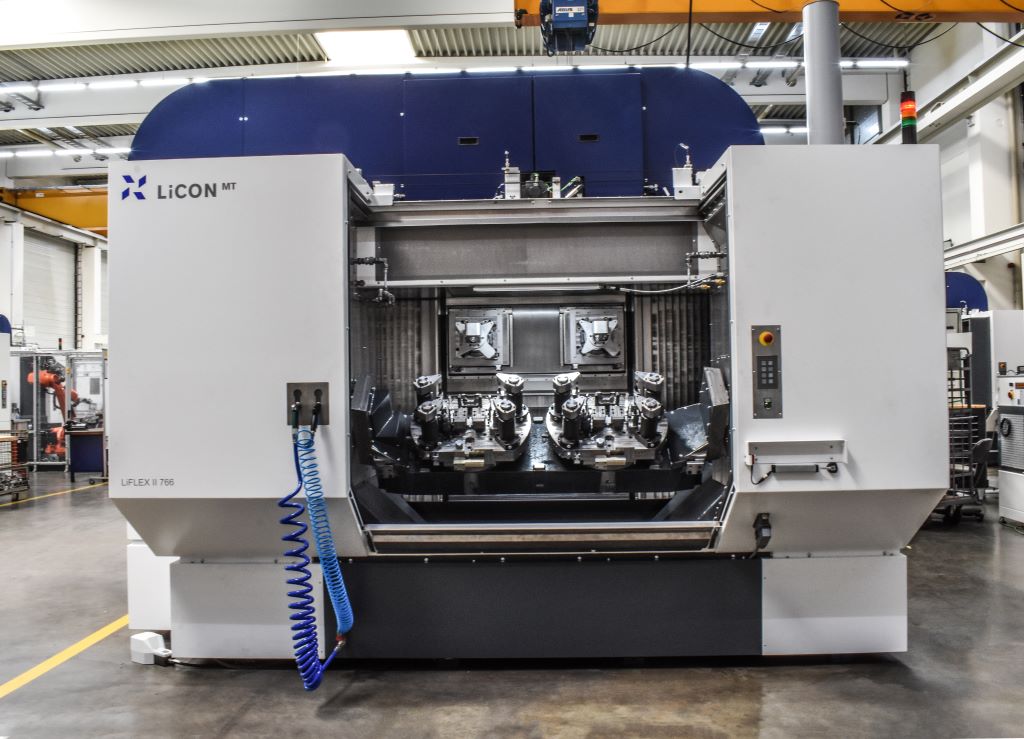
Projektanforderungen und Lösungen im Überblick:
- Signifikante Kapazitätserhöhung in der bestehenden Halle
Doppelspindler mit deutlich höherer Produktivität pro Stellfläche - Simultanproduktion mit doppelspindliger Bearbeitung
- Reduzierte Komplexität mit automatisierter Direktbeladung durch Roboter
- Erfüllung spezifischer Projektanforderungen durch Flexibilität
- Verbesserte Leistung mit kürzeren Werkzeugen und Fünf-Achs-Maschine
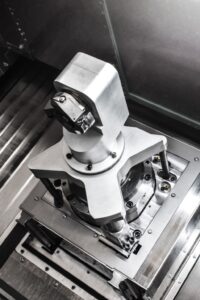
Kapazitätserweiterung in der bestehenden Halle
Haldex-Geschäftsführer Philip Andersson erklärt die Strategie zur deutlichen Erweiterung der Kapazität in der bestehenden Halle: „Mit zehn doppelspindligen LiCON-Maschinen erhöhen wir die Produktion von Messschiebern um 40 % und müssen nicht einmal zusätzliche Hallenfläche schaffen. Wir haben ein Standardkonzept mit automatisierten Roboterzellen, bestehend aus jeweils fünf Bearbeitungszentren, Roboterbeladung, Rohteilentnahme mittels „Griff in die Kiste“ vom Roboter und einer integrierten CMM-Maschine. Wir sind froh, die robusten LiCON-Maschinen als Kernstück unserer strategischen Kapazitätserweiterung zu haben.“
Simultanproduktion mit Doppelspindelbearbeitung
Aufgrund ihrer steifen Bauweise erbringt die LiFLEX II 766 ihre Leistung zweispindlig mit 500 Nm pro Spindel und einer Vorschubkraft von 10.000 N. „Mit einer so leistungsstarken Maschine bearbeiten wir jetzt zwei Bremssättel aus GLS 600-Material in der Zeit von einer und sparen zudem viel Hallenplatz. Die LiFLEX-Maschinen sind für Schwerzerspanung gebaut“, sagt Björn Kihlberg, Produktionsingenieur bei Haldex, der die gesamte Umstellung mit vorangetrieben hat.
Reduzierte Komplexität
Per Holmqvist ist Globaler Leiter der Fertigungstechnik bei Haldex. Er ergänzt: „Darüber hinaus haben wir jetzt eine direkte Beladung, die die Anzahl der zu prüfenden Vorrichtungsnester auf ein Minimum reduziert. Die Beladung durch den Roboter ist so schnell, dass die direkte Beladung die beste Lösung für diese Anwendung ist, da alle Vorrichtungsnester stets in Produktion sind.“
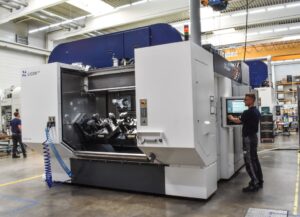
Erfüllung der spezifischen Projektanforderungen mit Flexibilität
Thorsten Scheid, Global Project Manager Operations bei Haldex, ist beeindruckt: „Alle unsere individuellen Anforderungen wurden berücksichtigt und perfekt umgesetzt.“ LiCON hat die perfekte Größe, um großartige Maschinen zu bauen und dabei dennoch flexibel auf die Kundenbedürfnisse eingehen zu können.
Verbesserte Leistung
Die Konstruktion des Bremssattels erfordert das Fräsen eines Merkmals, das für ein Standardwerkzeug unzugänglich ist, da es sich im Inneren des Werkstücks verborgen befindet. Um den Bremssattel auf einer vierachsigen Maschine zu bearbeiten, musste in der Vergangenheit ein z-förmiger Doppelwinkelkopf verwendet werden, der sehr aufwändig zu warten war. Haldex suchte nach einer wirtschaftlicheren Alternative, die LiCON mit der fünfachsigen Lösung lieferte. Jetzt ist ein wesentlich robusterer 90°-Winkelkopf im Einsatz. Die hohen Kräfte während des Fräsprozesses werden von drei starken Bolzen aufgenommen, die an den 500 Nm Spindeln angebracht sind und den Winkelkopf fest abstützen. Auf diese Weise wird eine ratterfreie Produktion bei hohen Vorschubgeschwindigkeiten erreicht – und dies mit gleichzeitig zwei Werkstücken. „Es ist uns gelungen, den z-förmigen Winkelkopf zu vermeiden, da wir den Bremssattel in der fünfachsigen Maschine in der besten Arbeitsposition platzieren können,“ freut sich Fadil Fazlic, Leiter der Haldex-Zerspanungswerkzeugabteilung.
Autor: Nils Baumgartner
Kontakt: