Mehrere Fraunhofer-Institute und die Brandenburgische Technische Universität Cottbus-Senftenberg arbeiten unter Federführung von Rolls-Royce Deutschland und weiteren Partnern wie die Forschungseinrichtung ACCESS an der Zukunft des hybridelektrischen Fliegens. Gefördert durch das Land Brandenburg sowie das Bundesministerium für Wirtschaft und Klimaschutz forschen die Partner an einem völlig neuen Antriebssystem für Mittelstreckenflugzeuge bis 35 Passagiere.
Die Clean-Sky-Programme der Europäischen Union und darin enthaltene Clean-Aviation-Perspektiven sind eine wichtige Richtschnur für die Branche, die durch den Luftverkehr verursachten Stickoxid- und Lärmemissionen deutlich zu reduzieren. Eine vielversprechende Technologie dafür ist das hybridelektrische Fliegen: Eine Gasturbine erzeugt elektrische Energie, mit der ein Zwischenbatteriespeicher geladen wird; für den Antrieb bezieht das Flugzeug seine elektrische Energie aus diesem Speicher. Größere sowie langsamer drehende Rotoren erzeugen weniger Lärm am Boden und verursachen einen deutlich kleineren Lärmteppich als Flugzeuge mit konventionellem Antrieb. Der modulare Aufbau des vorgeschlagenen Konzepts ermöglicht darüber hinaus, zukünftig auch alternative Treibstoffe oder völlig neue Stromquellen einzusetzen.
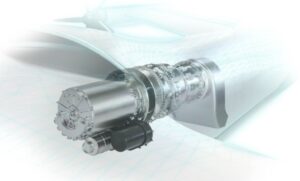
Bis Mitte 2026 wollen die Partner Fertigungstechnologien für die Herstellung hybridelektrischer Antriebskomponenten entwickeln, vorhandene Technologien qualifizieren und prototypische Komponenten herstellen. Dabei liegt der Fokus auf einer beschleunigten Entwicklung und Bereitstellung von Prototypen. In einem von hoher Wettbewerbsintensität geprägten Sektor sollen die Entwicklungszeiten erheblich verkürzt werden.
Beispielhaft dafür steht das Vorhaben, die Durchlaufzeiten vom fertigen Design eines Funktionsprototypen bis zur Übergabe an den Auftraggeber von derzeit mehreren Monaten auf wenige Wochen zu verkürzen. In weiteren Projekten entstehen hochflexible Produktionskonzepte, ohne die eine effiziente Serienfertigung nicht möglich wäre. Für Cottbus und die Lausitz eröffnen diese Projekte die Perspektive attraktiver Arbeitsplätze von der Entwicklung modernster Antriebssysteme (nicht nur in der Luftfahrt) bis zur industriellen Produktion.
Jedes der beteiligten Fraunhofer-Institute bringt seine spezifischen Kompetenzen ein, um dem Flugzeugbauer Lösungen für eine spätere Serienentwicklung verfügbar zu machen. Zahlreiche geplante Produktionstechnologien wie additive Fertigung (3D-Druck) und Umformung wurden bisher noch nicht im Flugzeugbau angewandt; sie für diese Branche mit ihren besonders strengen Anforderungen an Qualität, Zuverlässigkeit und Haltbarkeit zu qualifizieren ist eine Herausforderung, der sich die Institute nun stellen.
Die hohe Interdisziplinarität der Forschungsvorhaben erfordert, die Kompetenzen mehrerer Institute zu nutzen und technische Fragestellungen synergetisch zu diskutieren. Eine der wichtigsten Komponenten, an deren Entwicklung mehrere Institute beteiligt sind, ist die Brennkammer der Gasturbine.
Das Fraunhofer IWU übernimmt Koordination
Das Fraunhofer-Institut für Werkzeugmaschinen und Umformtechnik IWU hat sich über viele Jahre einen Namen in der Entwicklung modernster Herstellungsverfahren und Produktionssysteme gemacht. Auf Seiten der Forschungspartner übernimmt es die Koordinierung. Das Fraunhofer IWU ist insbesondere mit seiner Expertise in der Umformtechnik sowie der Hochleistungszerspanung und deren digitalen Prozessabbildung gefragt. Bei der Brennkammern-Gehäusefertigung bringt es sein Know-how in der Massivumformung sowie der flexiblen Blechteilfertigung ein. Weiterer Schwerpunkt ist die für einen effizienteren Betrieb bzw. höheres Drehmoment verantwortliche Anordnung oder Geometrie der Draht-Wicklungen (Spulen) elektrischer Antriebe. Insbesondere unterstützt das Fraunhofer IWU die für einen erfolgreichen Projektabschluss unabdingbare, durchgängige digitale Darstellung über den gesamten Entwicklungszyklus bis hin zur Serienfertigung.
Fraunhofer IWS und IFAM bringen additive Fertigung ein
Das Fraunhofer-Institut für Werkstoff- und Strahltechnik IWS setzt auf die laserbasierte additive Fertigung. Mittels Direct Energy Deposition (DED) wird punktuell Metall aufgeschmolzen und anschließend verschweißt; eine Düse bringt das Material nur dort auf, wo es gebraucht wird. So lassen sich Bauteile von bis zehn Metern Länge in Form und Größe frei bedrucken. Für die Herstellung der Brennkammer fiel die Wahl auf das Verfahren Laser Powder Bed Fusion (PBF-LB). Dabei schmilzt ein Laser Metallpulver Schicht für Schicht auf ein Bauteil auf. Materialsparend werden erforderliche Kühllöcher beim Drucken von vorneherein ausgespart.
Ein besonders innovatives metallisches 3D-Druckverfahren der israelischen Firma Tritone Technologies Ltd. wird am Fraunhofer-Institut für Fertigungstechnik und Angewandte Materialforschung IFAM weiterentwickelt. MoldJet führt zwei Fertigungsverfahren zusammen, die im Wechsel zur lagenweisen Bauteilfertigung arbeiten. Dabei wird in einer Lage zunächst die Form als Negativ zur Bauteilgeometrie aus einem wachsartigen Polymer mit sogenannten Inkjet-Druckköpfen hergestellt. Diese gedruckte Lage Formmaterial wird dann über eine Schlitzdüse und eine Rakel mit Metallpulverpaste befüllt. Durch den lagenweisen Aufbau ist die Fertigung von komplexen Bauteilen mit Hinterschneidungen oder auch innenliegenden Kanälen ohne Verwendung von Stützstrukturen möglich.
Forschungseinrichtung ACCESS e.V. mit an Bord
Keine Gasturbine kommt ohne gegossene Bauteile wie Turbinenschaufeln oder Gehäuse aus. ACCESS e.V. ist für die Entwicklung dieser Gusskomponenten verantwortlich. Am 2021 gegründeten Standort in Cottbus entstehen neueste additive Verfahren zur Beschleunigung der aus vielen Prozessschritten bestehenden Feingussroute. Hierdurch können zukünftig Feingussteile werkzeuglos in kürzerer Zeit, mit geringeren Investitionskosten und mit höherer Designfreiheit entwickelt werden.
Chesco sichert Kompetenzaufbau
Das Center for Hybrid Electric Systems (chesco) der Brandenburgischen Technischen Universität Cottbus-Senftenberg (BTU) übernimmt Entwicklungsumfänge und koordiniert zukünftig Aufträge der von Rolls-Royce Deutschland beispielsweise an die Fraunhofer-Institute erteilten Forschungs- und Entwicklungsprojekte. Gleichzeitig wird chesco den Kompetenzaufbau für eine spätere Serienfertigung hybridelektrischer Passagierflugzeuge in der brandenburgischen Lausitz sicherstellen.
Die neue Betriebsstätte am Siemens-Halske-Ring befindet sich auf dem Campus der BTU und damit in unmittelbarer Nähe zur BTU und chesco. Auch die operative Abstimmung mit den bereits in Cottbus ansässigen Fraunhofer-Instituten profitiert von der neuen Präsenz der drei Institute in der brandenburgischen Lausitz.
Rolls-Royce Deutschland
Rolls-Royce entwickelt und liefert komplexe Energie- und Antriebslösungen für sicherheitskritische Anwendungen in der Luft, zu Wasser und an Land. Rolls-Royce Deutschland ist seit 1990 mit eigenen Standorten in Deutschland präsent und in der Luftfahrtindustrie aktiv. Innerhalb des Konzerns hat Deutschland mit rund 10.000 Mitarbeitenden an einem Dutzend Standorten nach dem Vereinigten Königreich die zweitgrößte Belegschaft. Rolls-Royce Deutschland ist der einzige deutsche Flugtriebwerkshersteller mit Zulassung für die Entwicklung, Herstellung und Instandhaltung moderner ziviler und militärischer Turbinentriebwerke.