„In den vergangenen acht Jahren haben wir bei Industrie 4.0-Projekten festgestellt: Technologisch und planerisch haben wir das gut konzipiert, aber es muss vom Mitarbeiter auch akzeptiert werden“, gibt Prof. Gisela Lanza, Leiterin des wbk Instituts für Produktionstechnik im Karlsruher Institut für Technologie und Mitglied der WGP (Wissenschaftliche Gesellschaft für Produktionstechnik), die Parole aus. Das Thema Arbeit 4.0 hat sich wie selbstverständlich auf die Agenda gesetzt, die Wissenschaftler mussten über Akzeptanz, Motivation und neue Rollenverteilungen in der digitalisierten Fabrik nachdenken.
Eindeutiges Ergebnis bislang: 100 Millionen Euro schwere Förderprogramme für Autonomik und Smart Services, 26 vom Bundeswirtschaftsministerium geförderte Mittelstandskompetenzzentren und über 300 Anwendungsbeispiele in der Produktion bestätigen auch im Zeitalter von Algorithmen und künstlicher Intelligenz die 2.500 Jahre alte Weisheit des griechischen Philosophen Protagoras: Der Mensch ist das Maß aller Dinge.
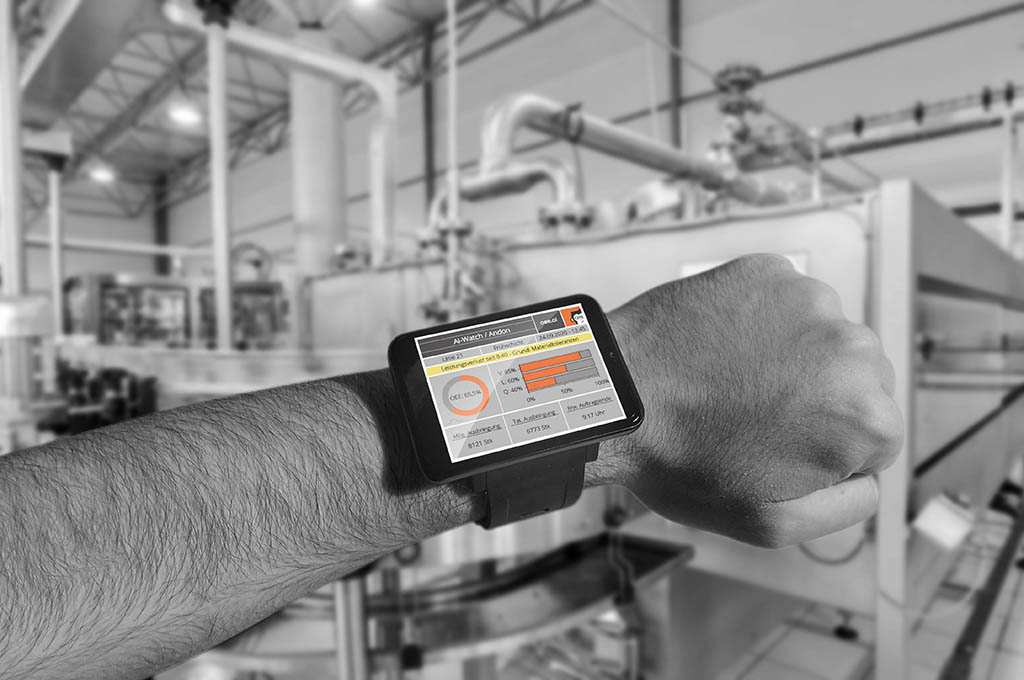
Intelligente Systeme fördern auch die Motivation
In der Produktion erfordern vor allem die Ist-Zeit-Steuerung und Algorithmus gestützte Überwachung schnelle Entscheidungen. Die ifp-Software GmbH in Aachen bietet ein Programm für die Vernetzung und Optimierung von Produktionsstraßen an. Die Firma nutzt die METAV digital gerne, um potenziellen neuen Kunden die Möglichkeiten aufzuzeigen. Mithilfe von Zeitreihen errechnet ein Algorithmus wahrscheinliche Fehlerquellen und sendet sie in Sekundenschnelle zum Mechaniker. Das System erreicht bis zu 30 Prozent höhere Anlagenleistung – und motiviert zudem die Mitarbeiter.
Jörn Steinbeck, Co-Founder des Unternehmens, erläutert die Auswirkungen auf den Alltag im Shopfloor: „Wir arbeiten in Ist-Zeit, ein gut trainierter Algorithmus kann Sekunden später Lösungsvorschläge aufzeigen.“ Wenn aber der Arbeiter mit dieser Information erst zum Meister laufen müsse, um dessen Weisung einzuholen, dann sei „der Zeitvorsprung wieder verspielt“.
Heißt im Klartext: Um die Möglichkeiten von KI-Anwendungen in der Praxis voll auszuschöpfen, „muss der Mitarbeiter weitreichender entscheiden dürfen, aber auch mehr vom Gesamtsystem verstehen.“ Steinbecks Schlussfolgerung: „Wir kommen weg von der Kontrolle, hin zum Kontext“. Oder in den Worten von Lanza: „Der Mitarbeiter braucht mindestens so viel Eigenverantwortung, um den Fehler selbst sofort zu beheben. “
Sebastian Weski, Vertriebsleiter der Exapt Systemtechnik GmbH in Aachen, macht ähnliche Erfahrungen. Die Firma entwickelt und vertreibt seit 1967 CAM-Systeme und bietet zusätzlich eine intelligente Betriebsmittelverwaltung für die zerspanende Industrie. Das komplexe Programm hat unter anderem intelligente Arbeitsabläufe hinterlegt, so dass Werkzeuganforderungen, Lagerbewegungen und Rüstoptimierungen automatisch ablaufen. Dadurch erreicht die Softwareschmiede heute schon bis zu 30 Prozent Produktivitätssteigerung, auf der METAV digital können sich Interessierte die Lösungen vorführen lassen.
Auch hochmoderne CAM-Anwendungen laufen nur dann effektiv, wenn der Mensch an der Maschine eine größere Verantwortung und unmittelbare Entscheidungsbefugnis hat. „Unser System erlaubt einen Probelauf mit einem digitalen Zwilling. Der Mechaniker kann sehr schnell sehen, ob die eingesetzten Werkzeuge beispielsweise die Oberfläche verkratzen oder ob der Vorschub zu groß ist. Dann meldet er das sofort an die CAD-Programmierer zurück. Wir verbinden mit unserer Software die Menschen an den unterschiedlichsten Stationen im Zerspanprozess“, erläutert Weski. Und das heißt: Mehr Verantwortung, mehr Kompetenz, mehr Entscheidungsgewalt für den Werker an der Maschine.
Kleine Losgrößen profitabel produzieren
„Tausende verschiedener Produkte und Varianten bis zu Losgröße eins zu fertigen, ohne kostspielig Anlagen umzurüsten“ – das ist die Vision bei Bosch Rexroth. Die Bosch Gruppe steigerte 2019 ihren Umsatz mit vernetzten Industrie-4.0-Lösungen für Fertigung und Logistik um 25 Prozent auf 750 Mio. Euro. Diese Vision ist nur mithilfe von intelligenten Assistenzsystemen zu erreichen. Doch auch die neueste Generation von kollaborierenden Industrierobotern (Cobots) erfordert eine neue Unternehmenskultur und flachere Entscheidungsstrukturen.
Die Müller Maschinentechnik GmbH aus Düren vertreibt Leichtbauroboter, die in den unterschiedlichen Bereichen den Mechaniker unterstützt. Rund um die Apparate hat sich ein „Ökosystem“ aus verschiedensten Werkzeugen entwickelt – die eisernen Helfer laden, palettieren, schweißen, fräsen, schleifen, je nach Anforderung. Interessierte können sich die ganze Bandbreite der Einsatzmöglichkeiten gerne auf der METAV digital vorführen lassen.
Pascal Klee, Verkaufsleiter Automation, betont: „Ein Cobot soll mit dem Menschen zusammenarbeiten. Gemeinsam können sie dann statt nur einer Maschine eine ganze Produktionseinheit bedienen.“ Es gehe um „Networking“, nicht darum, den menschlichen Kollegen zu ersetzen. Im Gegenteil: Die Möglichkeit, in Kooperation auch kleine Losgrößen profitabel herzustellen, geben dem Unternehmen den entscheidenden Wettbewerbsvorteil.
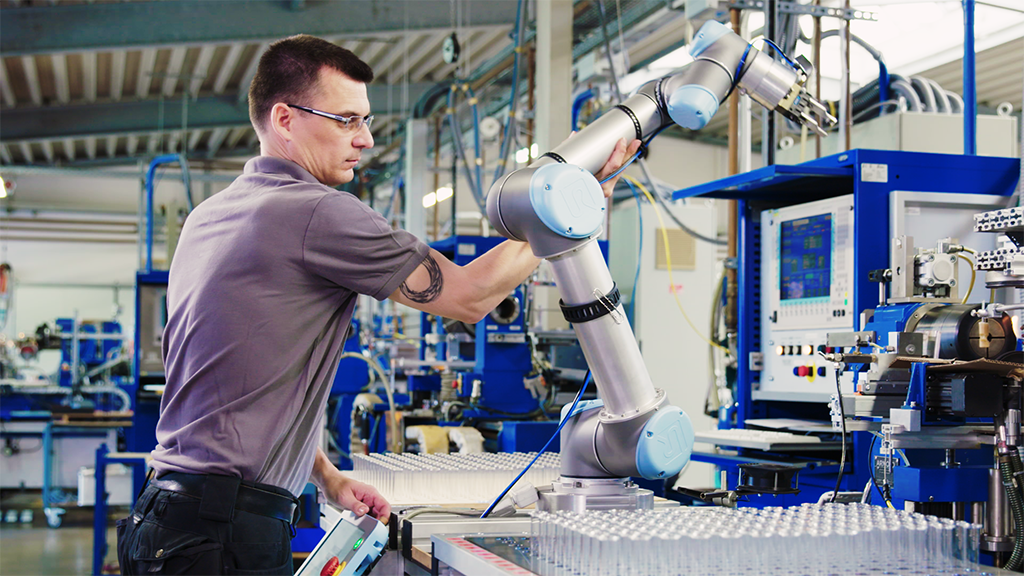
KI-Agent entlastet von Routine
Doch nicht nur der Produktionsmitarbeiter, auch sein Vorgesetzter sieht sich mit grundsätzlich neuen Anforderungen konfrontiert. Im interdisziplinären Verbundprojekt teamIn versuchen Forscher der WGP in Kooperation mit zwei Industrieunternehmen herauszufinden, wie digitale Technologien und KI sinnvoll in den Produktionsprozess integriert werden können.
Die Wissenschaftler haben vor allem die neue Rolle der Führungskraft im Fokus und verfolgen vier Teilziele: Es gilt, geeignete digitale Leitungsinstrumente zu entwickeln, einen KI-Agenten, der Vorgesetzte von alltäglicher Routine entlastet. Zudem hat sich das Team vorgenommen, moderne Führungssysteme zu gestalten und die Auswirkungen auf Rollenbilder und Kompetenzanforderungen zu untersuchen. Im letzten Schritt entwerfen die Wissenschaftler einen kompletten Transformationsprozess. Die Ergebnisse werden in Lernwerkstätten eingespielt und sind dann allen in Deutschland ansässigen Unternehmen zugänglich.
Gisela Lanza erläutert: „Firmenvertreter können hier mit den Pilotfirmen in den Austausch gehen, sich inspirieren lassen. In einem Best-Practice Beispiel sieht der Betrieb, welche Elemente und Tools es gibt, um sie dann an die eigene Problemstellung anzupassen.“ In den Werkstätten simulieren die Forscher sogar in einer Spielumgebung neue Hierarchiemodelle, wenn zum Beispiel kein Chef mehr da ist und die Mitarbeiter den Shopfloor selbst organisieren müssen.
Optimalität trotz Dezentralität
Einige Trends können die Wissenschaftler heute schon ausmachen: Die Systemgrenzen für den Einzelnen werden ausgeweitet. „Der Mechaniker, der bisher nur eine Maschine bedient hat, wird in Zukunft die ganze Linie orchestrieren“, fasst Lanza zusammen, „der Meister wird statt nur der Linie das ganze Werk betreuen, und der Werksleiter ist verantwortlich für die gesamte Supply Chain.“
Jörn Steinbeck steuert Erfahrungen aus der Praxis bei: „Unsere intelligenten Systeme sammeln Erfahrungswissen an, das früher beim Meister angesiedelt war. Ein gut trainierter Algorithmus demokratisiert Fachwissen.“ Das hat natürlich Auswirkungen auf die Unternehmenskultur. Klassische Top-Down-Entscheidungswege und komplexe Hierarchien sind für agile, von Algorithmen und intelligenten Assistenzsystemen unterstützte Produktionsgruppen zu schwerfällig. Schon die Qualitätssicherung bringt herkömmliche Instrumentarien an ihre Grenzen – Monatsreports taugen wenig, wenn die Software Fehler und Anomalien in Ist-Zeit meldet.
Die Führungskraft selbst wandelt sich vom Anweiser zum Coach. Die lernenden Systeme übernehmen mehr und mehr die klassische Lösungskompetenz des Meisters, die Arbeiter an der Maschine lösen viele Probleme selbst. Dafür brauchen sie den Vorgesetzten weniger als Kontrollinstanz, eher als Assistenz und Hilfestellung. Lanza postuliert: „Früher dachten wir, nur zentrale Einheiten arbeiten effektiv, in Zukunft aber entsteht Optimalität trotz Dezentralität.“
Kontakt: