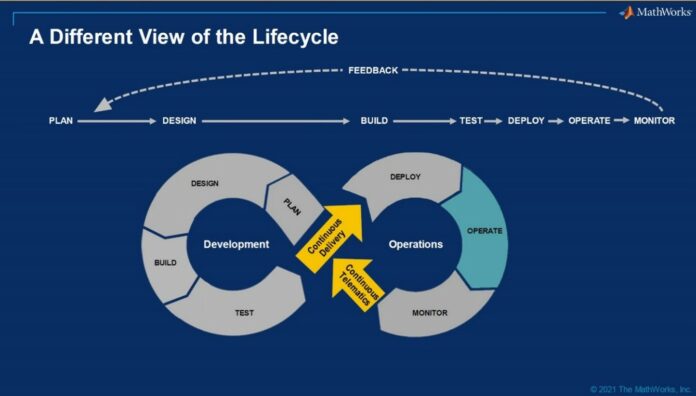
Die meisten Unternehmen sind derzeit auf der Suche nach Wegen, ihre individuelle digitale Transformation zu gestalten. Viele haben dafür bereits spezifische Ziele, KPIs und Strategien ausgearbeitet. Das allein reicht aber nicht, denn am Ende kommt es darauf an, digitale Transformation erfolgreich und pragmatisch umzusetzen. Wie das gelingen kann, erklärt Philipp Wallner, Industry Manager bei MathWorks, im Folgenden:
Digitale Transformation und die Zukunft der Massenproduktion
Vom Wandel hin zu datengetriebenen Prozessen, der Integration neuer und vorhandener Plattformen bis hin zur zunehmenden Komplexität von Software und Hardware – die Herausforderungen, vor denen Unternehmen heute stehen, sind vielfältig. Allen gemeinsam ist die Notwendigkeit, Systeme und Prozesse miteinander zu vernetzen. So lassen sich Daten nutzbringend zur Leistungsoptimierung, Kostensenkung und Entwicklung neuer Dienstleistungen einsetzen.
Hier können neue Blickwinkel hilfreich sein. Continuous Lifecycle- und DevOps-Ansätze etwa lassen sich auf mechatronische Systeme übertragen, die nicht ausschließlich auf Software basieren. Dies gestattet es, über den aktuellen Stand der Technik hinauszugehen, sich aber gleichzeitig auf bekannte und akzeptierte Konzepte zu stützen.
Die Fabrik der Zukunft soll nicht mehr nur einheitliche Produkte in großen Stückzahlen herstellen können. Sie soll vielmehr die Flexibilität und Personalisierung maßgeschneiderter Produkte mit den niedrigen Stückpreisen der Massenproduktion kombinieren. Voraussetzung dafür ist eine vernetzte, flexible und autonome Produktion mit durch Software rekonfigurierbaren Maschinen.
Die stetig wachsende Komplexität von Anlagen und deren Software stellt dabei jedoch eine zentrale Herausforderung dar. Ein Lösungsansatz ist der konsequente Einsatz von Modellen und Daten in der Entwicklung von Maschinen, Prozessen und Dienstleistungen.
Der digitale „Rote Faden“: Die systematische Nutzung von Modellen und Daten über den gesamten Lebenszyklus
Im Lebenszyklus von mechatronischen Systemen findet man Modelle typischerweise in zwei Phasen: der Konzeption auf der Systemebene und dem Entwurf von Teilsystemen
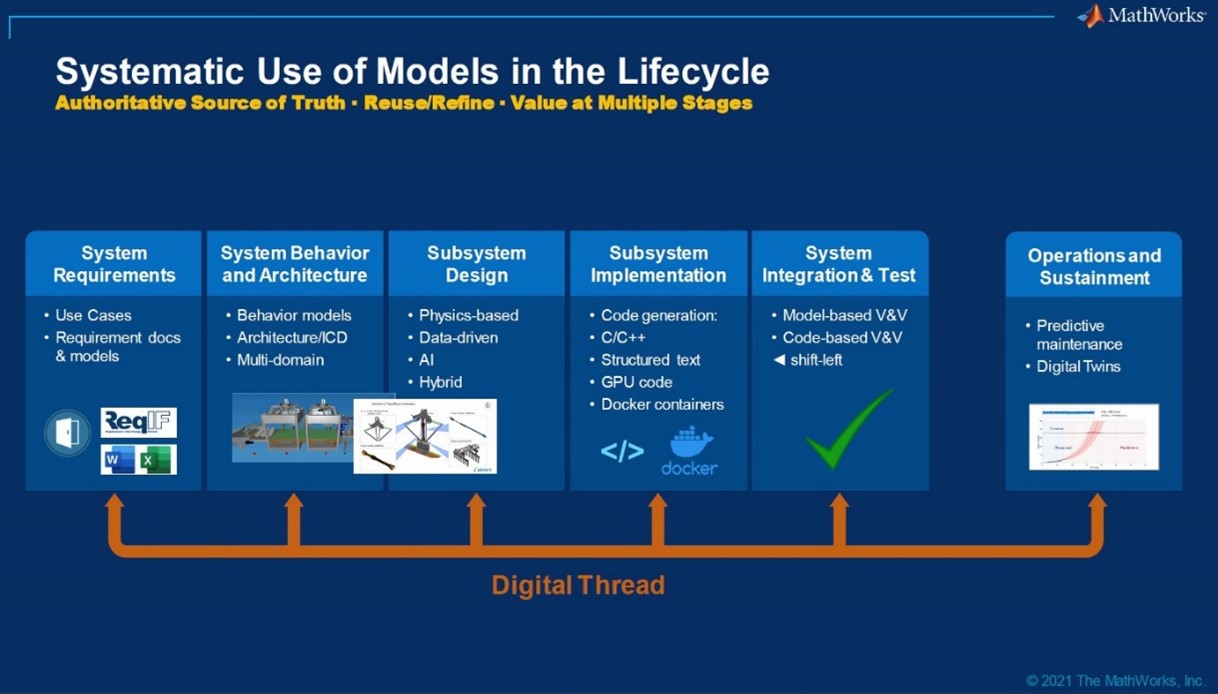
Eine echte digitale Transformation verlangt jedoch mehr. Sie erfordert die systematische Verwendung von Modellen über den gesamten Lebenszyklus einer Maschine oder Anlage (Abbildung 1). Modelle fungieren dabei als zentrale „Single Source of Truth“. Durch bidirektionale Verknüpfung dieser Modelle mit Anforderungen und Anwendungsfällen (Abb. 1 ganz links) entsteht eine Art digitaler Roter Faden aus Informationen und Rückverfolgbarkeit. So wird sichergestellt, dass Systeme das tun, was sie sollen.
Aus den gleichen Modellen wird im Anschluss automatisch die Software generiert, die auf dem fertigen Produktionssystem laufen wird (Mitte). Auch die Verifikation und Validierung stützt sich auf diese Modelle (rechts v. d. Mitte), die nun als goldene Referenz dienen. Bei einer auf Modelle gestützten Produktentwicklung kann dies von Anfang an stattfinden. Verifikation und Validierung werden damit zu einem durchgängigen Prozess und helfen, Integrationsprobleme und Fehler früher aufzudecken.
Während der Inbetriebnahme und sogar während des Betriebs können die Modelle als digitale Zwillinge genutzt werden und stellen eine wichtige Hilfe für den Betrieb und die Wartung von Maschinen und Anlagen dar. Zum Beispiel lassen sie sich zur virtuellen Inbetriebnahme und für Predictive Maintenance nutzen.
Perspektivwechsel: DevOps für mechatronische Systeme
„Für die digitale Transformation brauchen Ingenieure Fähigkeiten, die über diese Basis hinausgehen. Sie möchten etwa die Funktionalität bereits im Einsatz befindlicher Systeme schneller erweitern. Sie möchten Betriebsdaten von Systemen nutzen, um deren Leistung und Effizienz zu verbessern. Mit anderen Worten wünschen sich Betreiber kontinuierlich aktualisierbare Maschinen.“, stellt Jim Tung, MathWorks Fellow, in seinem Vortrag auf der munich_i fest.
Dafür müssen die Software-Entwicklung und Release-Zyklen agiler werden. Die Auswirkungen neuer Software oder Hardware auf die Systemleistung muss schnell bewertet und die von diesen Systemen erzeugten Daten müssen besser für die Entscheidungsfindung genutzt werden können.
Um dies besser zu verstehen, ist ein Perspektivwechsel erforderlich (Abbildung 2). Anstelle der in Abbildung 1 dargestellten linearen Sichtweise kann man sowohl Entwicklungs- als auch Betriebsprozesse als agile, miteinander verflochtene Kreisläufe betrachten. Verbunden werden sie in der einen Richtung durch kontinuierliche Auslieferung von Software-Upgrades, Continuous Delivery. In der anderen Richtung fließt kontinuierlich Anlagen-Telemetrie in die Entwicklung zurück. Dieses Bild ist Softwareentwicklern vertraut: Es handelt sich um einen DevOps-Zyklus.
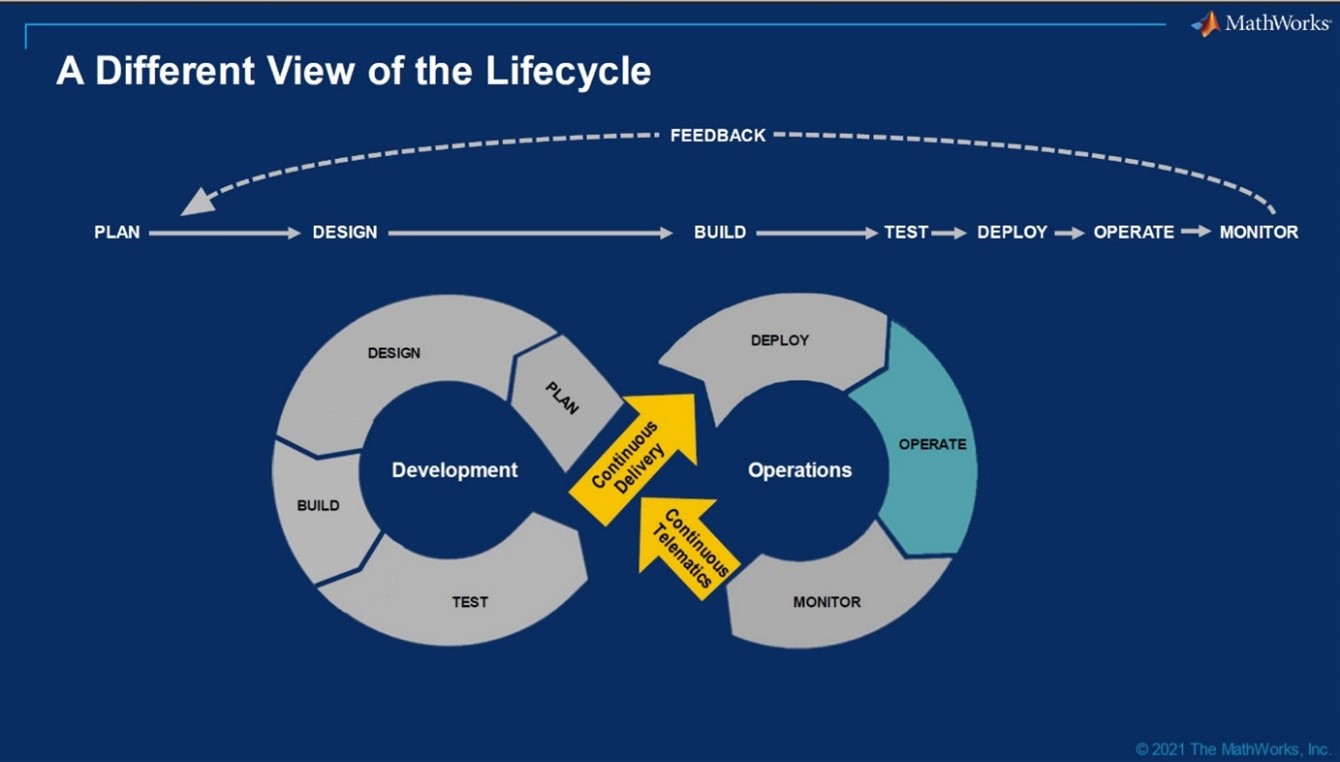
Ein Praxisbeispiel – Atlas Copco
Was dies in der Praxis bedeutet, lässt sich am besten anhand einer Fallstudie veranschaulichen. Atlas Copco ist ein belgischer Hersteller moderner Kompressorsysteme. Mit Model-Based Design wird dort Systemfunktionalität auf einer gemeinsamen Plattform der Ingenieurteams entworfen und implementiert. Auf der Vertriebsseite wiederum setzt Atlas Copco diese Modelle in Konfigurationstools ein.
Gemeinsam mit dem Kunden wird exakt das individuell angepasste System zusammengestellt, das er benötigt. Atlas Copco hat damit die eingangs erwähnte flexible Massenproduktion realisiert. Die gleichen Modelle sind zudem in das Fertigungssystem integriert. Einfließende Produktionsdaten und Testergebnisse dienen zur Qualitätssicherung.
Die Kompressoren von Atlas Copco verfügen über eine Datenaufzeichnung und eine Verbindung zu einem zentralen Server. Das ermöglicht es, sich abzeichnende Probleme schnell zu erkennen, mögliche Energieeinsparungen zu realisieren und eine maximale Betriebsdauer zu erreichen.
Atlas Copco verfügt damit über eine große Flotte digitaler Zwillinge, die Daten an den Entwicklungsprozess zurückliefern. Das wiederum erlaubt es dem Unternehmen, zuverlässigere und leistungsfähigere Systeme zu bauen und neue Dienstleistungen und Mehrwert für die Kunden zu definieren. Grundlage ist der erwähnte digitale Roten Faden, der den gesamten Produktlebenszyklus durchzieht.
Beispiele wie die von Atlas Copco zeigen uns, dass es anfangs zwar ein Umdenken bedeutet, Prozesse von Grund auf neu zu denken und neue Arbeitsweisen zu etablieren. Doch genau diese Schritte sind schließlich wegweisend, um digitale Transformation in der Produktion langfristig erfolgreich zu gestalten.
Kontakt: