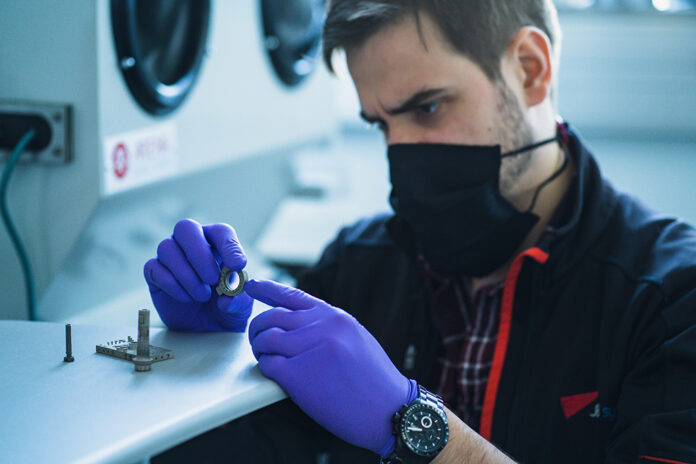
Im Rahmen seiner Zielsetzung, die Effizienz und Agilität seiner Produktionsprozesse zu erhöhen, hat JPB Système ein additives Fertigungsverfahren mehrere Monate lang getestet. Die Testergebnisse mit der MBJ-Technologie zur Fertigung flugtauglicher Teile werden den Erwartungen gerecht. Denn Ziel ist es, leichtere Alternativen schneller, einfacher und kostengünstiger als mit herkömmlichen additiven Fertigungsverfahren, wie Zerspanung und Guss, zu entwickeln. Mit dieser AM-Technologie ist es dem Unternehmen auch gelungen, äußerst komplexe Produkte mit neuen Geometrien zu fertigen und die Produktionseffizienz durch den Wegfall der Montage weiter zu steigern.
Kürzere Fertigungszeiten beschleunigen die Markteinführung
„Wie wir erwartet haben, beweisen unsere Tests nachdrücklich, dass die Vielseitigkeit und Fähigkeit der MBJ-Technologie zur Verringerung des Zeit- und Kostenaufwands enorme Vorteile für uns als Unternehmen und für unsere Kunden bieten“, erklärt Jocelyn Vecchio, Director of Engineering & Innovation bei JPB Système.
„Die höhere Produktionseffizienz wird deutlich, wenn man diese Technologie mit dem typischen Spritzgussverfahren zur Teilefertigung vergleicht“, fügt er hinzu. „Der Spritzguss hat nicht nur Einschränkungen in Bezug auf die erzielbaren Geometrien, sondern ist auch mit hohen Werkzeugkosten und langen Fertigungszeiten von etwa sechs Monaten verbunden – sogar noch länger, wenn ein Geometriewechsel vorgenommen werden muss und eine neue Spritzgussform erforderlich ist.“
„Im Gegensatz dazu konnten wir die gleichen Teile mit dem additiven MBJ-Verfahren innerhalb von nur ca. vier Wochen herstellen. Das entspricht einer Verringerung des Zeitaufwands um mehr als 80 %, wodurch wir letztendlich auch unsere Lieferzeit an Kunden verkürzen. Aufgrund der Flexibilität dieser Technologie nimmt die Fertigung von 100 verschiedenen Teilen nicht mehr Zeit in Anspruch als von 100 identischen Teilen.“
Ein weiterer großer Vorteil für JPB Système besteht darin, das sich mit diesem Verfahren weitaus leichtere Teile herstellen lassen. Durch robuste Hohlkörper und Gitterstützstrukturen haben die von JPB Système entwickelten Testteile die gleiche Festigkeit wie herkömmlich hergestellte Metallteile, doch einen weitaus geringeren Materialverbrauch. In einigen Fällen konnte das Unternehmen sogar das Gewicht um 30 % reduzieren.
„Das ist ein schlagendes Argument für OEM-Hersteller und Akteure weiter oben in der Lieferkette, die ständig versuchen, das Gesamtgewicht von Flugzeugen zu reduzieren“, so Benjamin Sangouard, Versuchsingenieur bei JPB Système. „Ein leichteres Flugzeug bedeutet geringerer Treibstoffverbrauch und infolgedessen auch geringere Kosten und Emissionen, was aus Sicht der Nachhaltigkeit natürlich eine große Rolle spielt.“
„Der Faktor Nachhaltigkeit wird auch durch das Prinzip der On-Demand-Produktion unter Beweis gestellt. Denn mit diesem additiven Fertigungsverfahren können Unternehmen wie wir die notwendigen Teile zum notwendigen Zeitpunkt kostengünstig herstellen – ein enormes Plus gegenüber herkömmlichen Verfahren mit ihren langen Produktionszeiten. Dadurch können wir unsere Flexibilität erhöhen und müssen keine großen Mengen mehr bevorraten“, erklärt Sangouard weiter.
Bessere Designmöglichkeiten
Außerdem profitiert JPB Système von der größeren Designfreiheit dieses additiven Fertigungsverfahrens, mit dem komplexe Produkte weitaus einfacher hergestellt werden können. So lassen sich beispielsweise zwei Teile leichter zu einem Teil zusammenfügen oder Produkte mit einem Bauteil in einem anderen Produkt herstellen – was mit konventionellen Fertigungsverfahren normalerweise nicht möglich ist.
So konnte das Team beispielsweise ein montiertes, mehrteiliges funktionales System herstellen, das durch den Einbau von drei Komponenten in einem mehrere Vorteile bietet. Aufgrund der geringeren Teilezahl wird die Lieferkette verkürzt und entfällt die Montagezeit. Aus Sicherheitssicht ist auch die Wahrscheinlichkeit einer möglichen Beschädigung durch Fremdkörper, wenn auch höchst unwahrscheinlich, nahezu gänzlich ausgeschlossen.
Für Jocelyn Vecchio bedeutet die mögliche Nutzung der AM-Technologie zur Entwicklung komplexerer Produkte mit weniger Teilen auch, dass JPB Système seine strategische Wettbewerbsfähigkeit durch neue Patente erhöhen könnte.
„Bislang hat sich unsere Erforschung neuer Anwendungsmöglichkeiten der MBJ-Technologie als sehr erfolgreich erwiesen und bietet enorme Möglichkeiten zur Innovation unserer Produktionsprozesse, um den Anforderungen unserer Kunden besser gerecht zu werden“, erklärt er abschließend.
Im Laufe des Jahres 2023 wird JPB Système ein neues, hochmodernes Werk in Villaroche südlich von Paris eröffnen. Über eine Initiative, die das Industriewachstum beschleunigen und Hersteller unterstützen soll, wurde der Bau dieses Werks teilweise aus staatlichen Mitteln finanziert. Die mögliche Integration der additiven Fertigungstechnologie und anderer disruptiver innovativer Technologien, die das Konzept Industrie 4.0 unterstützen, wird das Potenzial automatischer Produktionsanlagen nach der Inbetriebnahme des neuen Werks eindrucksvoll unter Beweis stellen.
Kontakt: