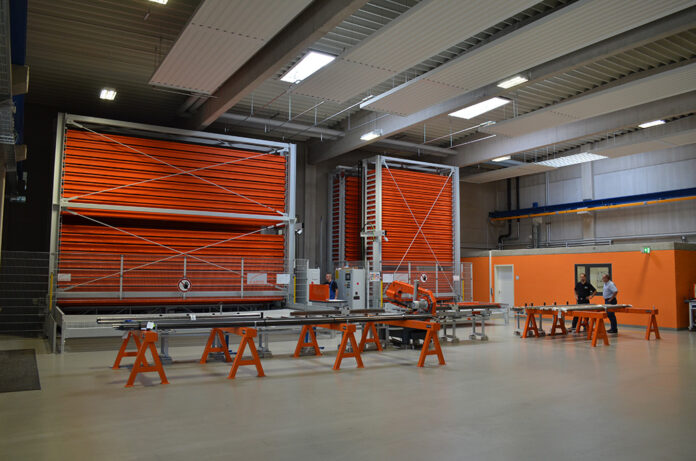
„Was wir hier sehen, war noch vor kurzem über mehrere Hallen unseres Standortes verteilt“, beschreibt ein sichtlich stolzer Heinz Weitner, Geschäftsführer der Werner Weitner GmbH, bei einem Rundgang durch die neue Produktions- und Lagerhalle des Unternehmens. Alles ist hell, aufgeräumt, sauber und verhältnismäßig ruhig – ein angenehmes Arbeitsklima. Die Halle ist das Schmuckstück der „Weitner Engineering World“ – so nennt der Spezialist für Maschinenbau und Werkstattausrüstung seinen Stammsitz im oberbayrischen Eichstätt.
1968 als Metallbaubetrieb gegründet, ist Werner Weitner mittlerweile ein gefragter Partner der internationalen Automobilindustrie und Medizintechnik-Branche. Mit rund 250 Mitarbeitern stellt das Unternehmen hauptsächlich Spezialwerkzeuge her, die etwa in den Vertragswerkstätten zahlreicher Autohersteller zum Einsatz kommen.
Organisches Wachstum fordert die Logistik
Dabei setzt Werner Weitner seit jeher auf einen umfangreichen Maschinenpark. Dieser war allerdings bislang aufgrund der räumlichen Gegebenheiten in verschiedenen umliegenden Gebäuden untergebracht. „Wir sind organisch gewachsen und haben dadurch auch unsere Kapazitäten nach und nach erweitert“, berichtet Heinz Weitner.
Dies sei jedoch immer mehr auch zu einer logistischen Herausforderung geworden: „Der Aufwand, um die benötigten Teile und Materialen zwischen den einzelnen Bearbeitungsschritten hin und her zu transportieren, nahm mit der Zeit überhand.“ Daher entschied sich die Firma dazu, einen Großteil seiner Prozesskette in einer eigens errichteten Halle zu zentralisieren.
Der Maschinenbauer verarbeitet in seiner Fertigung hauptsächlich Stähle und verschiedene Legierungen, aber auch Aluminium und Kunststoffe. Das Portfolio reicht dabei vom Prototypen bis zur Großserie. „Daraus ergibt sich eine ziemlich große Materialvielfalt, für die wir auch entsprechende Lagerkapazitäten benötigen“, schildert Heinz Weitner. „Schließlich erwarten unsere Kunden kurze Lieferzeiten und eine hohe Verfügbarkeit der Produkte.“ Viele Materialien bestellt das Unternehmen daher auf Vorrat, um bei Bedarf schnell reagieren zu können.
„Weitner 4.0“: Der Weg in eine effizientere Zukunft
In der Vergangenheit nutzte Werner Weitner zur Aufbewahrung des Rohmaterials verschiedene manuell bediente Lagerbereiche – das machte die Handhabung jedoch äußerst ineffizient: „Das Ein- und Auslagern sowie der Transport zu den verschiedenen Bearbeitungsmaschinen nahm eine Menge Zeit und Arbeitskraft in Anspruch“, erzählt Florian Winhard, Abteilungsleiter der Sägerei.
Im Zuge des Hallenneubaus sollte deshalb auch die Lagertechnik automatisiert werden. „Diese Entscheidung war Teil unseres internen Projekts ‚Weitner 4.0‘, mit dem Ziel, sämtliche Prozesse im Unternehmen für die Zukunft nachhaltig zu optimieren“, ergänzt Daniel Miehling, Controlling und IT bei Werner Weitner.
Als Partner für dieses Vorhaben fiel die Wahl auf KASTO Maschinenbau. „In der Sägetechnik setzen wir bereits seit vielen Jahren auf diesen Hersteller und sind damit sehr zufrieden“, begründet Weitner die Entscheidung. „Dass KASTO auch automatische Lagersysteme für Langgut und Blech anbietet, war uns ebenfalls bekannt. Also haben wir uns zusammengesetzt, um gemeinsam eine Lösung für unsere Anforderungen zu finden.“
Kompakte Turmlager für Rohmaterial bis 6 Meter Länge
Um den Materialfluss in der neuen Halle möglichst effizient zu gestalten, empfahl KASTO die Installation von zwei Turmlagersystemen vom Typ UNITOWER. Der UNITOWER 1.0 ist dabei zur Aufnahme von Langgut bis drei Meter, der UNITOWER 2.0 für Materialien bis sechs Meter Länge geeignet. Beide sind freistehende Doppeltürme.
Mit 52 beziehungsweise 41 Kassetten bieten die Lager genügend Platz für die Rohmaterialbestände von Werner Weitner – und das auf einer äußerst geringen Fläche. „Die Turmlager nutzen den vorhandenen Platz optimal aus“, findet Florian Winhard. „Im Vergleich zu unseren bisherigen Lagerflächen ist nun alles wesentlich kompakter, ordentlicher und übersichtlicher.“
Welcher Artikel sich in welcher Kassette befindet, ist im Lagerverwaltungssystem elektronisch hinterlegt. Dieses ist über eine individuell angepasste Standard-Schnittstelle an die bei Werner Weitner verwendete ERP-Software proALPHA angebunden. Die Bedienung erfolgt entweder über ein Pult direkt am Lager oder über ein mobiles Handgerät.
Ein Regalbediengerät (RBG) stellt die benötigten Kassetten nach dem Prinzip „Ware zum Mann“ vollautomatisch an der jeweiligen Ausgabestation bereit. „Der Arbeitsablauf ist dadurch wesentlich ergonomischer und Zuordnungsfehler nahezu ausgeschlossen“, freut sich Weitner. Die kurzen Zugriffszeiten des UNITOWER ermöglichen es dem Unternehmen, anstehende Aufträge zügig abzuarbeiten.
Angeliefert, zugeschnitten, eingelagert
Zwischen den beiden Einlagerstationen der Türme befindet sich eine Schwenkrahmen-Bandsäge vom Typ KASTOmicut E 4.6. Sie ist für Abläng- und Gehrungsschnitte bei Rohren, Profilen und Vollmaterial konzipiert – und erfüllt bei Werner Weitner im Wesentlichen eine Aufgabe: „Unsere Materialien werden in der Regel alle mit einer Länge von sechs Metern angeliefert“, erklärt Winhard.
„Mit dieser Säge trennen wir alle Artikel, die wir nur mit maximal drei Metern Länge benötigen, um sie anschließend im kleineren UNITOWER 1.0 einzulagern.“ Der dadurch eingesparte Umweg über die Sägerei rechnet sich bei dem großen Materialspektrum von Werner Weitner und steigert die Effizienz beim Einlagerungsprozess deutlich.
Um auch alle anderen Sägeaufgaben schnell erledigen zu können, hat die Sägerei ebenfalls einen zentralen Standort in der neuen Halle bekommen. Der Maschinenpark umfasst sechs weitere Modelle aus dem Hause KASTO – die meisten davon aus der universell einsetzbaren Bandsägeautomaten-Baureihe KASTOwin. „Vor dem Neubau waren auch unsere Sägen dezentral auf dem Gelände platziert – das verursachte viele unnötige Wege“, erinnert sich Winhard. „Diese Situation konnten wir nun verbessern und haben außerdem drei Sägen ausgetauscht, so dass wir hier jetzt gut und modern aufgestellt sind.“
Die KASTOwin-Maschinen sind für eine Vielzahl von Materialien und Abmessungen geeignet, für besondere Herausforderungen steht den Mitarbeitern außerdem die Hochleistungs-Bandsäge KASTOwin pro zur Verfügung. „Wir sind seit vielen Jahren mit den KASTO-Sägen zufrieden, und jedes neue Modell überzeugt uns wieder mit solider Leistung und einem hohen Funktionsumfang“, betont Geschäftsführer Heinz Weitner.
Lager- und Sägetechnik aus einer Hand
Seit Ende 2019 ist die neue Halle mitsamt der Lager- und Sägetechnik in Betrieb. Rund 45 Kassetten pro Tag werden im Lager durchschnittlich bewegt, insgesamt waren das bislang rund 5.000 Vorgänge. „In der Vergangenheit durchlief ein Material auf dem Weg bis zum fertigen Sägeabschnitt bis zu acht Handhabungsschritte“, rechnet Weitner vor. „Diese Zahl konnten wir durch die Turmlagersysteme und die effizientere Organisation halbieren – wir sparen also eine Menge Zeit und Arbeitsaufwand.“
Auch den Lagerbestand an Rohmaterial konnte das Unternehmen durch die Zentralisierung mehr als halbieren – damit ist weniger Kapital gebunden und mehr Platz für wertschöpfende Tätigkeiten zur Verfügung.
„Der große Vorteil an der Zusammenarbeit mit KASTO ist, dass wir alles aus einer Hand bekommen haben und auch bei der hard- und softwareseitigen Integration der Lager und Sägen in unseren Produktionsablauf kompetente Unterstützung hatten“, freut sich Daniel Miehling. „Dank eingehender und leicht verständlicher Schulungen hatten auch unsere Mitarbeiter keinerlei Berührungsängste mit der neuen Technik und können diese problemlos bedienen.“
Störungen seien an den UNITOWER-Lagern seit Inbetriebnahme so gut wie keine aufgetreten, betonen die Verantwortlichen bei Werner Weitner – und selbst wenn, können sich die KASTO-Experten vom Hauptsitz im badischen Achern aus per Fernwartung jederzeit auf die Anlage schalten und Fehler schnell und unkompliziert beheben.
„Bei KASTO stimmt nicht nur die Produktqualität, sondern auch der Service“, bringt es Weitner auf den Punkt. „Wir haben also mehr als genug Gründe, auch in Zukunft weiter zusammenzuarbeiten – und das nicht nur, weil wir eine Ein-Lieferanten-Strategie für jeden Maschinentyp verfolgen. KASTO unterstützt uns dabei, unser Unternehmen effizient und zukunftssicher aufzustellen.“
Kontakt: