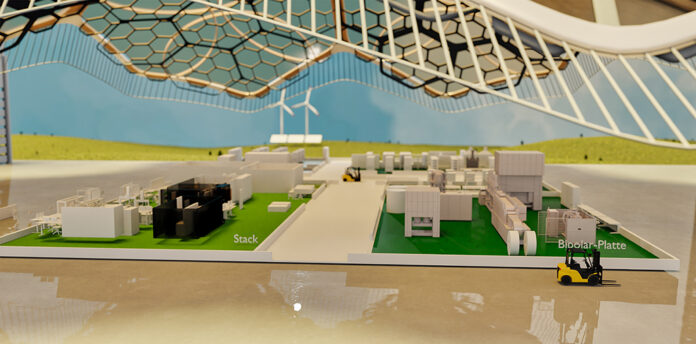
Wer über die Anschaffung einer Photovoltaikanlage für das heimische Dach nachdenkt, darf trotz aktueller Preisschwankungen mit einem deutlich kleineren Budget als vor zehn oder fünfzehn Jahren planen. Hocheffiziente, industrielle Großserienproduktion macht es möglich. Ein in Handarbeit gefertigtes Einzelstück würde heutigen Ansprüchen an Haltbarkeit, Wirkungsgrad oder Widerstandsfähigkeit gegenüber Hagelschlag kaum genügen und wäre schlicht unbezahlbar.
Ob hochkomplexe Produkte wie Autos und Smartphones oder Waren des täglichen Bedarfs: Erst die Herstellung in großer Stückzahl mit dafür geeigneten Produktionsverfahren macht diese Produkte erschwinglich. Nicht viel anders verhält es sich mit Wasserstoff. Damit Wasserstoff zu einer tragenden Säule in der klimaneutralen Energieversorgung werden kann, gilt es ihn zu marktwirtschaftlichen Preisen, in ausreichender Menge und klimaneutral herzustellen und mit hoher CO2-Minderungsquote zu verwenden.
Wesentliche Wasserstoffsysteme müssen dafür in die industrielle Serienproduktion überführt werden. Das betrifft insbesondere Elektrolyseure – in ihnen wird Wasser mit Strom z. B. aus Wind oder Sonne in Wasserstoff und Sauerstoff gespalten – und Brennstoffzellen, die den so gewonnenen Wasserstoff in elektrische Energie umwandeln.
Im Fokus der Referenzfabrik.H2 stehen Technologien, die eine industrielle Produktion mit erheblichen Fortschritten bei Verfahren, Digitalisierung und Kosten ermöglichen sollen. Mit Forschung zu günstigeren Werkstoffen, zur Qualität der Bauteile, zur Langlebigkeit, zu besseren Produktionstechnologien, zur Skalierbarkeit der Produktionsverfahren, ihrer Automatisierung, der Vernetzung von Produktionslinien, dem Aufbau effizienter Lieferketten und zur Fabrikplanung soll die Großserienfertigung rentabel werden.
Dr. Ulrike Beyer, Leiterin der Wasserstoff-Taskforce am Fraunhofer- Institut für Werkzeugmaschinen und Umformtechnik IWU und Koordinatorin des Projekts: »Die Produktion muss einen entscheidenden Beitrag leisten, um dem Wasserstoff zum Durchbruch zu verhelfen. Genau daran arbeiten wir in der Referenzfabrik.H2.« Für diese Herausforderung stehen Bundesmittel in Höhe von insgesamt 30 Millionen Euro zur Verfügung.
Adaptive Prozessketten: Die Fertigung als Ganzes zu betrachten hebt die Produktion auf ein neues Niveau
Eine moderne, effiziente Fabrik nimmt sich den Menschen zum Vorbild. Seine Fähigkeit, sich als lernendes System flexibel an wechselnde Umfeldbedingungen anzupassen, ist Vorbild für jedes Produktionssystem. In unserem Alltag gehen wir ständig mit Varianz um, können uns flexibel an Situationen anpassen.
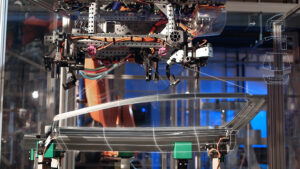
Essen und trinken muss jeder Mensch, er ist dabei jedoch nicht an einen exakt einzuhaltenden Zeitplan gebunden. War mittags keine Zeit für eine ausführliche Mahlzeit, fällt eben das Abendbrot etwas reichhaltiger aus. Ist die Schlange vor einer Kasse lang, lässt sich der Einkauf auch an einer anderen Kasse bezahlen. Abläufe und Routinen sind in der Fabrik Prozesse – und können hinsichtlich ihrer Anpassungsfähigkeit noch viel vom Menschen lernen.
Moderne Fertigungsprozesse als Ergebnis kontinuierlicher Optimierung
In der industriellen Produktion sind Robustheit, Effizienz, Stabilität und Fertigungsqualität wichtige Orientierungsgrößen. Einfache Prozesse kann der Mitarbeitende in der Produktion problemlos weiterentwickeln, Fehler eigenständig erkennen und abstellen. Soll die Fertigung komplexer Produkte in anspruchsvollen Lieferketten verbessert werden, helfen Sensorik beim Erkennen, künstliche Intelligenz beim Strukturieren und Aktorik beim Umsetzen von Verbesserungspotenzialen in dem betrachteten Fertigungsabschnitt.
Doch wie gut passt diese Verbesserung zur vorausgegangenen oder nachfolgenden Etappe? Es gilt, alle Wechselwirkungen in der gesamten Prozesskette einschließlich der Logistik zu verstehen sowie vor- und nachgelagerte Abläufe einzubeziehen. Doch was bedeutet verbessern? Das kommt ganz auf das Ziel an: Es kann durchaus sinnvoll sein, gezielt die Toleranzen einzelner Bauteile oder Komponenten zu hinterfragen, ohne die geforderte Qualität eines Produkts insgesamt in Frage zu stellen. So könnte die Abweichung in einem Einzelprozess akzeptiert werden, wenn sie später problemlos ausgeglichen werden kann.
Ist das gleiche (Gesamt-)Ergebnis mit weniger Aufwand erreichbar, kann dieser entsprechend reduziert werden. Weniger Stillstand, weniger Eingriffsbedarf und geringere Kosten wären die wünschenswerte Folge. Dr. Wolfgang Zorn, Leiter des Geschäftsfelds Adaptive Prozessketten am Fraunhofer IWU, bringt den Grundgedanken dieser adaptiven Prozessketten auf den Punkt: »Bauteile müssen nicht immer perfekt sein, aber sie müssen perfekt zueinander passen.«
Das Fraunhofer IWU sieht mit der Adaptivität von Prozessketten großes Potenzial für die Produktion von morgen. Gemeinsam mit zwölf Konsortialpartnern unter der Leitung der Grammer AG arbeitet das Fraunhofer IWU im Projekt »AdaProQ« an generischen Methoden zur Beherrschung der Fertigungsqualität innerhalb komplexer Prozessketten. Der Schwerpunkt liegt dabei auf Anwendungen des Automobilbaus. AdaProQ verfügt über ein Projektvolumen von 19,1 Millionen Euro und wird vom Bundesministerium für Wirtschaft und Klimaschutz gefördert. Das Fraunhofer IWU ist mit einer großen Bandbreite seiner Kompetenzen vertreten, die Dr. Wolfgang Zorn als Projektleiter koordiniert.
Für den Aufbau methodischer Kompetenz verfolgt das Fraunhofer IWU in seinem Geschäftsfeld eine langfristige Strategie. Die Komplexität dieser Aufgabe erhöht sich nochmals deutlich in einer Lieferkettenperspektive, die komplexe Logistikprozesse berücksichtigen muss. Künstliche Intelligenz, Sensorik, Aktorik und Datenmanagement bilden das Rückgrat adaptiver Prozessketten. Auf der Hannover Messe zeigt das Fraunhofer IWU in Halle 5 Stand A06 in drei ausgewählten Projekten erste Ansätze auf dem Weg zu adaptiven Prozessketten.
Intelligenter Werkzeughalter in der Zerspanung: »smartTOOL«
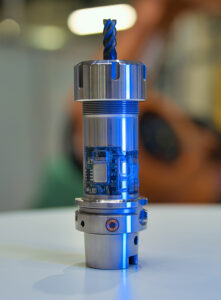
Temperaturen ausgestattet. (Bildnachweis: Fraunhofer IWU)
Für Qualität und Produktivität in der Zerspanung kommt es mehr denn je darauf an, Prozesse möglichst nah an der Wirkstelle überwachen zu können. Der intelligente Werkzeughalter smartTOOL ist eine sehr wirtschaftliche und wegen seiner unabhängigen Energieversorgung auch zur Nachrüstung geeignete Lösung, um nah am Bearbeitungsgeschehen wertvolle Prozessdaten aufzunehmen.
So können Prozesskräfte, Schwingungen und Temperaturen erfasst, mit den passenden Algorithmen ausgewertet und in Prozesskennwerte überführt werden. Diese Kennwerte dienen wiederum als Basis zur Überwachung oder gar adaptiven Prozessregelung – smartTOOL hilft damit, auch ältere Maschinen datenbasiert fit für die Fertigung der Zukunft zu machen.
Adaptive Profilschienenführung für mehr Wirtschaftlichkeit von Werkzeugmaschinen
Die Profilschienenführung in Werkzeugmaschinen einzustellen bedeutet, sich vorab auf eine Druckstärke, also eine Vorspannungsklasse, festzulegen. Im Betriebsalltag wird dann meist zu viel Vorspannung genutzt, was die Maschinen unnötig früh verschleißen lässt.
Das Fraunhofer IWU hat eine Lösung für dieses Problem entwickelt: Mittels Piezoaktorik lässt sich die Vorspannungsklasse hochdynamisch im Betrieb einstellen. So lässt sich der Anpressdruck je nach Bedarf steuern. Bestehende Werkzeugmaschinen können mit dieser Technologie nachgerüstet und damit wirtschaftlicher betrieben werden.
Miniaturisierte Aktoren als Schlüsselelemente von Produktionsanlagen
Aktoren sind Schlüsselelemente in nahezu jeder Produktionsanlage und Maschine. Dort, wo es für konventionelle Aktoren (z. B. Piezo-, Pneumatik- oder Hydraulikaktoren) zu eng wird, können Aktoren auf Basis von thermischen Formgedächtnislegierungen eingesetzt werden.
Im Projekt HochPerForm soll zusammen mit den Fraunhofer-Instituten IPM und IFAM der Abkühlvorgang mittels schaltbarer Heatpipes um den Faktor 100 beschleunigt werden. Die Arbeitsfrequenzen können dadurch auf über 1 Hz erhöht werden. Zur weiteren Miniaturisierung der Aktoren werden additive Fertigungsverfahren eingesetzt, die es ermöglichen sollen, den gegebenen Bauraum optimal auszunutzen.
Sichere und leistungsstarke Softrobotik für menschennahe Aufgaben
Beim Rasenmähen haben wir uns schon an ihre Unterstützung gewöhnt – bei anderen menschennahen Aufgaben etwa in Haushalt oder Pflege gibt es bislang kaum Ansätze für Roboter. Das Fraunhofer IWU vereint mit Hilfe neuartiger schaltbarer Steifigkeiten in den Robotern die benötigte Kraft mit der nötigen Sicherheit. Auf der Hannover Messe stellen die Forschenden einen Roboterarm vor, der Menschen künftig in ihrem unmittelbaren Umfeld unterstützen kann.
Interaktion³: Multimodale Wege der Mensch-Roboter-Interaktion
So einfach war Roboterprogrammierung noch nie: dank des vom Fraunhofer IWU entwickelten multimodalen Interaktionssystems können Mitarbeitende in der Produktion künftig spielend leicht mit ihren Fingern die Bewegungsabläufe eines Roboters programmieren. Die Programmierung per Fingertracking und Sprachsteuerung kann sogar remote, also ortsunabhängig erfolgen. Damit kann Robotik künftig noch viel flexibler und auch für die Losgröße 1 (z.B. lackieren und polieren im Handwerk) wirtschaftlich eingesetzt werden. Das Team um Dr. Mohamad Bdiwi freut sich auf Besucherinnen und Besucher, die auf dem Fraunhofer-Gemeinschaftsstand ganz intuitiv einen Roboter anlernen möchten.
Das Fraunhofer IWU auf der Hannover Messe in Halle 5, Stand A06.
Kontakt: