In vielen Bearbeitungszentren zum Fräsen, Schleifen, Bohren oder Drehen werden Spindeln eingesetzt. Täglich unterliegen diese einer starken Beanspruchung durch Werkzeugwechsel oder Verunreinigung. Verschlissene Werkzeuge müssen schnell instandgesetzt werden, um Maschinenausfallzeiten zu vermeiden. Reparaturen lassen sich mittels Laserschweißen schnell und unkompliziert ausführen.
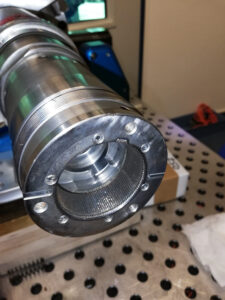
Mit dem Verfahren Draht- oder Pulverauftragsschweißen können Spindeln und Wellen rasch wieder instandgesetzt werden. Mit einem programmierten Verfahren wird Draht von alleine aufgeschweißt und die Spindeloberfläche aufgebaut und das ohne nennenswerten Verzug des Werkstücks. ALPHA LASER bietet dazu eine Reihe von Schweißlasern und Zubehör.
Um jedoch Reparaturzyklen zu minimieren, kann die Standzeit der Werkzeuge verlängert werden, indem die Randschicht der beanspruchten Stellen gezielt gehärtet wird mittels Laserrandschichthärten. Ein weiterer Vorteil: Laserhärten führt zu einer deutlicher Energieeinsparung im Vergleich mit anderen Härteverfahren.
Das Laserstrahlhärten ist ein sehr kostengünstiges und schnelles Verfahren zur Randschichthärtung, da es die partielle Härtung von ausgewählten, beanspruchten Funktionsflächen auf der Werkstückoberfläche ermöglicht. Die schnelle Selbstabschreckung verringert den Materialverzug beim Laserhärten, denn Randschichthärten mittels Laserstrahl funktioniert annähernd verzugsfrei. Dadurch, dass der Laserhärteprozess wärmeüberwacht wird, können auch Schnittkanten und schmale Radien, ohne Gefahr von Anschmelzungen gehärtet werden.
Die Energieeinsparung beim Laserrandschichthärten ist enorm: Zum Beispiel der Vergleich Vakuumhärten/ Laserrandschichthärten. Ein identisches Bauteil wurde jeweils vakuum- und lasergehärtet. Beim Laserhärten konnte eine Energieeinsparung von 95% festgestellt werden. Bei den heutigen Energiepreisen macht das viel aus. Aber nicht nur Energie wird gespart, sondern auch massiv Arbeitszeit.
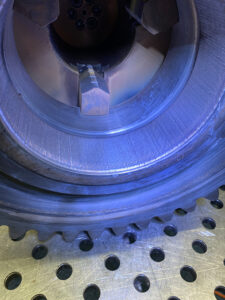
Der AL-ROCK mobil ist der erste mobile Roboter zum gezielten Härten von Metalloberflächen. Das zu härtende Bauteil muss nicht mehr zwingend ausgebaut werden, da der Laser direkt zum Werkstück gefahren werden kann. Der weit ausladende Roboterarm erreicht problemlos schwer zugängliche Stellen. Erforderlich ist lediglich der freie Zugang des Laserstrahls auf die zu härtende Werkstückoberfläche. Pulverauftragsschweißen ist mit diesem System ebenfalls möglich.
Das ALPHA LASER System AL-ROCK modular ist eine flexible stationäre Roboteranlage mit bis zu 16 synchronisierten Achsen zum gezielten Randschichthärten von Metalloberflächen an einer Vielzahl unterschiedlicher Bauteile, oder zum automatisierten Pulverauftragsschweißen.
Zum Ansteuern aller Achsen wir nur eine Steuerung benötigt. Dadurch ist die Bedienung der Härteanlage – auch mit Zusatz Pulverauftragsschweißen – sehr einfach und schnell erlernbar. Bearbeitet werden können Bauteile von unterschiedlichster Größe: von klein bis sehr lang.
Die ALPHA LASER GmbH auf der AMB 2022 in Halle 8, Stand D21
Kontakt: