Die Qualitätskontrolle in der Warmumformung erfolgt oft erst nach einer Abkühlung des Werkstücks: Herkömmliche Methoden der optischen Qualitätssicherung funktionieren bei heißen Teilen nur eingeschränkt, mit steigender Temperatur des Werkstücks wird die Unschärfe bei der Geometriebestimmung immer größer. Das führt bei prozessbedingten Qualitätsmängeln zu einer hohen Ausschussrate und damit zu unnötigen Kosten. Einen vielversprechenden Lösungsansatz verfolgt das Projekt GreenHiTemp mit Wärmebildaufnahmen, die zuverlässige Prognosen noch im Prozess anstelle nachgelagerter Kontrollen ermöglichen.
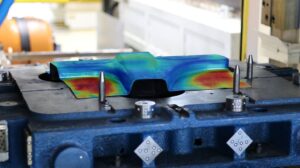
Das Fraunhofer IWU erforscht dabei gemeinsam mit der InfraTec GmbH die Vorteile der Thermografie im Anwendungsfall des Presshärtens. Dieses Verfahren kombiniert die Vorteile der Wärmebehandlung und der Umformung. Es erlaubt die Herstellung hochfester und gleichzeitig besonders leichter Karosserieteile. Ein Beispiel dafür sind
B-Säulen. Die in Wärmebildaufnahmen ermittelten Temperaturen des Werkstücks erlauben zuverlässige Rückschlüsse auf dessen Qualität.
100 Prozent der Teile können ohne Zeitverlust überprüft werden
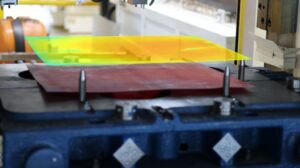
Über ein entsprechend trainiertes KI-Modell ist damit eine Härtevorhersage des Bauteils möglich. Mitarbeitende in der Produktion können anhand eines einfachen Farbschemas erkennen, welche Stellen des Bauteils nicht in Ordnung sind bzw. ob das gesamte Bauteil nach Ende des Umformprozesses als ›in Ordnung‹ oder ›fehlerhaft‹ gelten kann. Durch diese frühzeitige Transparenz werden Trends erkennbar, rechtzeitige Eingriffe in den Prozess sind möglich.
Ein kurzer Blick auf den Monitor ersetzt minutenlange Prüfprozedur
Bisherige Prüfungen müssen sich allein aus Zeitgründen auf Stichproben begnügen. Rund sieben Minuten würde es selbst bei einem vollautomatisierten Prüfprozess dauern, insgesamt 88 Messpunkte abzuarbeiten; teilweise käme nur eine zerstörende Prüfung in Betracht. Werden dabei Fehler entdeckt, muss mitunter ›sicherheitshalber‹ eine gesamte Charge vernichtet werden – mit GreenHiTemp lässt sich also Ausschuss in erheblichem Umfang vermeiden – für eine deutlich ressourcenschonendere und effizientere Produktion.
Kontakt: